Industria 4.0 en el mecanizado de implantes médicos
Contenido patrocinadoConozca cómo LINK, fabricante de implantes médicos, utiliza soluciones de mecanizado y automatización de DMG MORI para una producción desatendida, eficiente y de calidad.
Compartir
Waldemar LINK, empresa con más de 70 años de experiencia, se ha convertido en un referente en la fabricación de implantes médicos de alta calidad. Con una firme convicción en la innovación y la eficiencia, la empresa alemana utiliza soluciones de manufactura de última generación para ofrecer productos que mejoran la vida de miles de pacientes alrededor del mundo.
En este artículo, exploramos cómo esta compañía, en colaboración con DMG MORI, ha logrado optimizar su producción mediante la automatización, la digitalización y la Industria 4.0.
Innovación en la producción de implantes médicos: eficiencia y precisión
Desde su fundación en 1948, la empresa ubicada en Norderstedt, cerca de Hamburgo (Alemania), ha pasado de ser una empresa especializada en suministros hospitalarios a un fabricante internacional de implantes e instrumentos médicos.
Los desarrolladores y diseñadores de LINK colaboran constantemente con cirujanos para desarrollar productos de mayor calidad. Con aproximadamente 1,300 empleados en todo el mundo, la empresa está presente en los cinco continentes.
En cuanto a la producción, la empresa utiliza soluciones innovadoras de manufactura que cumplen con los requisitos de ingeniería para la producción de implantes médicos.
Más de 50 máquinas-herramienta CNC de DMG MORI se utilizan en tres turnos en las instalaciones de la empresa, y el uso de soluciones de automatización ha ido aumentando durante varios años. Las últimas máquinas instaladas incluyen dos centros de torneado y fresado NTX 1000 con Robo2Go para mecanizar copas acetabulares y un NTX 1000 para fabricar vástagos femorales.
El desarrollo demográfico y los avances quirúrgicos son dos factores importantes que promueven el crecimiento continuo en la ingeniería médica. Las endoprótesis alivian el dolor de hombro, cadera y rodilla. Al mismo tiempo, las modificaciones son cada vez más frecuentes debido al aumento de la esperanza de vida, entre otros factores.
Con una gama casi completa de productos, LINK se diferencia de competidores del mismo tamaño y establece estándares en endoprótesis, especialmente para los pacientes:
“Cada caso médico brinda esperanza a alguien para una vida con movilidad y sin dolor”, enfatiza Thomas Kuhlmann, gerente de producción en LINK. Se trata de mejorar la calidad de vida de los pacientes en todo el mundo. “Nunca detenerse: eso motiva a nuestros empleados cada día”.
Estrategias para una manufactura desatendida y eficiente
Esta pasión se combina con creatividad en el departamento de producción, donde se han utilizado soluciones de manufactura cada vez más modernas durante muchos años, la mayoría de las cuales son de DMG MORI.
“Hemos presenciado todos los hitos en primera persona, desde las primeras máquinas CNC hasta el mecanizado HSC de 5 ejes y el torneado y fresado de 6 caras, y seguimos confiando en las innovaciones”, dice Thomas Kuhlmann.
La producción automatizada, por ejemplo, se ha vuelto estándar. “De esta manera, queremos fabricar durante al menos 48 horas sin supervisión, con poca presencia del operador, para dar a nuestros especialistas libertad adicional para organizar otros trabajos”.
Thomas Kuhlmann (derecha) director de producción, y Carsten Schöttler director de fabricación en LINK.
Fuente: DMG MORI,
También se fomenta el trabajo en equipo: “En el pasado, cada uno era responsable de su propia máquina, pero ahora solo hay unas pocas personas encargadas de un gran número de máquinas, lo que requiere una coordinación considerable”.
La experiencia de la producción influye en cada nueva inversión, especialmente porque LINK ya no se centra en la compra de una máquina-herramienta estándar sino en el proceso en torno a la manufactura de un componente, como muestran sus últimas adquisiciones de máquinas DMG MORI.
“Con nuestro MobileLink utilizamos copas acetabulares de manufactura aditiva”, explica Carsten Schöttler, gerente de producción en LINK. El gran desafío era el manejo de las piezas brutas impresas en 3D con sus superficies rugosas. “Después de todo, debemos garantizar una alta calidad constante en un proceso automatizado"”
Las últimas inversiones de LINK incluyen dos sistemas NTX 1000 con Robo2Go para la manufactura automatizada de copas acetabulares.
Fuente: DMG MORI.
DMG MORI implementó esta tarea de forma fiable con dos soluciones de producción, cada una de ellas compuesta por un NTX 1000 y un Robo2Go. La facilidad de operación también fue un factor decisivo: “No se requiere conocimientos programación para enseñar el Robo2Go”, agregó Carsten Schöttler.
El software guía de manera conveniente al operador a través del proceso. Seis NTX 1000 son responsables del procesamiento de las copas acetabulares en todas sus variantes en LINK. Cada máquina produce 6,000 piezas al año. “Esto significa que, a pesar de toda la automatización, aún debemos ser flexibles para poder manejar esta mezcla de producción”, dice Carsten Schöttler.
Digitalización y monitoreo en la era de la Industria 4.0
Para Thomas Kuhlmann, la optimización continua del proceso también incluye un avance hacia la digitalización: “El hecho de que DMG MORI equipe sus máquinas con IoTconnector como estándar nos brinda una buena base para futuros proyectos de digitalización”.
LINK también utiliza DMG MORI Messenger para monitorear la producción. “Esto se debe a que el monitoreo constante y análisis de la gran cantidad de datos que recibimos desde la producción también nos ayuda a planificar nuestros procesos de una manera aún mejor y, sobre todo, garantizar la calidad nuestros productos”.
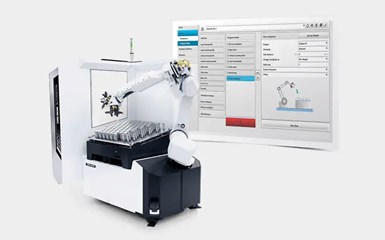
Robo2Go de segunda generación con bandeja de piezas de portabrocas. Interfaz de programación para el aprendizaje de piezas en menos de 15 min.
Fuente: DMG MORI.
El caso de Waldemar LINK demuestra que la innovación y la eficiencia son claves para el éxito en la industria de implantes médicos. La empresa alemana ha logrado posicionarse como un referente a nivel mundial gracias a su constante apuesta por la tecnología de última generación, la colaboración con socios estratégicos como DMG MORI y su compromiso con la calidad y la mejora continua.
El futuro de la manufactura de implantes médicos está marcado por la Industria 4.0, la automatización y la digitalización. LINK se encuentra a la vanguardia de esta transformación, adoptando nuevas tecnologías y estrategias que le permiten ofrecer productos cada vez más personalizados, eficientes y de alta calidad.
Si desea conocer las soluciones de DMG MORI para la industria médica, visite su sitio web.