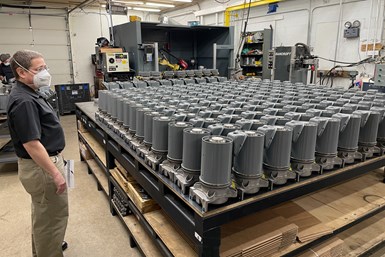
La zona de ensamblaje de MTH Pumps sirve actualmente de almacén para las bombas de freón terminadas. Las células de soldadura robotizada de la empresa (visibles en la parte trasera) no solo automatizan el proceso de ensamblaje, sino que también realizan operaciones que serían imposibles a mano.
MTH Pumps está a tope. El fabricante de bombas de Plano, Illinois, ha equipado su taller y el edificio adyacente con máquinas-herramienta, estanterías de almacenamiento, dispositivos de control de calidad, robots de soldadura y otros elementos.
Limitada en su capacidad de ampliar su flota de máquinas para satisfacer la creciente demanda de los clientes, la empresa recurre a una serie de soluciones creativas —incluida la automatización, pero no limitada a ella— para aumentar la productividad y el rendimiento.
La incorporación de robots de asistencia a sus máquinas multitarea Mazak Integrex fue el primer paso en el camino de la automatización de la empresa, pero para satisfacer las crecientes demandas de los clientes también ha sido necesario perfeccionar los procesos y las estrategias en torno a las máquinas y el herramental redundantes, la repetibilidad de los procesos y las configuraciones de puesta en escena de las piezas a medida. Estas estrategias no solo han permitido a MTH Pumps aumentar la producción y lograr una automatización sin luz, sino que lo ha hecho sin depender de grandes gastos en equipos de capital.
Calderas, enfriadores y freones
MTH Pumps abrió sus puertas por primera vez en 1965. El dueño de la segunda generación, Tim Tremain, se inició en la empresa en los años ochenta y ha estado al frente de los esfuerzos de automatización de la empresa desde que programó un centro de mecanizado horizontal de dos pallets al principio de su carrera.
La empresa utiliza piezas de fundición para crear más de 3,000 números de piezas, aunque la mayor parte de su trabajo consiste en variaciones de tres piezas para la línea de bombas de turbina regenerativas de la empresa. Estas bombas se componen de carcasas (formadas por componentes de la tapa y el soporte del motor) e impulsores, con anillos para las bombas de varias etapas.
Las carcasas suelen ser de bronce, acero inoxidable o hierro fundido, mientras que los impulsores suelen ser de bronce o de una aleación de alto contenido en níquel ASTM A494. Aunque la demanda de estas bombas se ha mantenido estable en los mercados de alimentación de calderas y enfriadores de larga duración, MTH ha observado un enorme aumento de la demanda de versiones sin sello de sus bombas para centros de datos de computadoras y otros clientes que utilizan sistemas de refrigeración con freón.
Incluso en las piezas sin el requisito de la ausencia de juntas, muchas de las piezas mecanizadas de MTH necesitan mantener tolerancias extremas, como sus impulsores, que requieren tolerancias de 0.0005” para la perpendicularidad, el paralelismo y la planitud en espesores de 0.082”.
En 2006, el impulso de la empresa hacia la mejora de la calidad la llevó a adquirir su primer torno-fresadora, una Mazak Integrex 200-IIIST de segunda mano, para contrarrestar las retenciones e imprecisiones resultantes de la transferencia de piezas entre máquinas.
Aunque el traslado de piezas entre husillos en la Integrex sigue requiriendo múltiples chucks, Tremain dice que la naturaleza automatizada del segundo chuck hace que la máquina multitarea tenga “un orden de importancia” mejor para la calidad que los dispositivos de posicionamiento y apriete manual de los HMC y los tornos utilizados antes por la empresa.
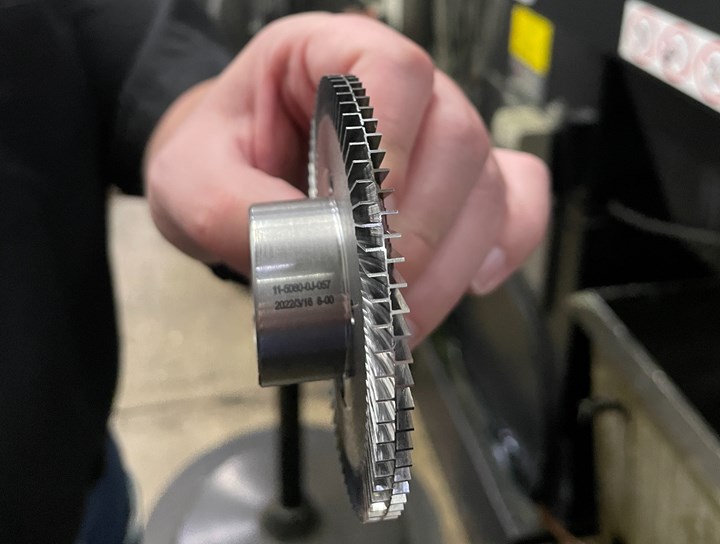
“El impulsor es el corazón de la bomba”, dice Tremain. Pero la ubicuidad del impulsor no hace que sus tolerancias de perpendicularidad y paralelismo de 0.0005” sean más sencillas de mecanizar, especialmente con un grosor de 0.082”. Las máquinas Integrex deben fresar los álabes de cada lado por separado, sin alterar la relación de tolerancia de perpendicularidad y paralelismo.
La primera máquina Integrex de MTH marcó tal diferencia en los procesos de la empresa, que el fabricante de equipos originales sustituyó gradualmente el grueso de sus máquinas de una sola operación por 12 máquinas Integrex multitarea de diversos tamaños y épocas. Cada una de estas máquinas incluye funciones de automatización incorporadas, como cepillos de desbarbado y robots de pórtico de tres ejes.
La empresa, que también ha emparejado una de sus máquinas con un robot de seis ejes, de Agile Robotic Systems, combina el robot de pórtico y el robot de asistencia a la máquina en una sola célula que facilita tramos de automatización sin luz durante la noche y durante todo el fin de semana.
Para poner en perspectiva la productividad de las máquinas multitarea, la empresa produjo 62,000 piezas en 2009 (un año después de que el equipo de MTH hubiera adquirido suficiente experiencia con el Integrex para empezar a utilizarlo en la producción completa). En 2016 —con el mismo número de operarios, pero con la mayoría de las fresadoras y tornos más antiguos sustituidos por torno-fresados— la empresa produjo 145,000 piezas, duplicando con creces su producción durante este periodo.
Sin embargo, incluso este aumento de la productividad no es suficiente para hacer frente a la demanda de bombas de freón. No solo han acudido a MTH nuevos clientes para estas bombas, sino que el mayor cliente de bombas de freón de la empresa tiene previsto cuadruplicar sus pedidos mensuales.
Con sus anteriores metodologías de producción, este aumento habría requerido que MTH Pumps duplicara el número de sus máquinas-herramienta. Pero cuando MTH comenzó a evaluar las tasas actuales de utilización de las máquinas, quedó claro que aumentar la utilización de las máquinas era la mejor opción para la empresa.
Un estudio sobre la utilización de las máquinas en 2021, mediante el software de monitorización de las máquinas de Vimana, descubrió que las máquinas de MTH alcanzaban una tasa de utilización del 25 % en un periodo de 24 horas al día.
Durante años, este nivel de utilización no había sido un problema porque el fabricante mantenía una impresionante tasa de entrega a tiempo del 95 %, logro que se debe en gran medida a que MTH es propietaria de una pequeña fundición que le permite a la empresa eludir los retrasos a los que se enfrentan otros fabricantes que producen piezas a partir de piezas fundidas. Pero con un aumento significativo de los pedidos de los clientes, la utilización del 25 % de las máquinas sería insostenible.
La constatación de la cantidad de capacidad de la máquina que no se utilizaba llevó a MTH a la optimización del proceso. Su primer movimiento fue comenzar a monitorear las métricas de producción del taller y establecer puntos de referencia a través de la plataforma Vimana para solucionar problemas cada vez que los tiempos de ciclo de una pieza se alargan por encima de los estándares históricos.
A continuación vino la tarea de determinar cómo mantener las máquinas de MTH en funcionamiento durante más tiempo, con el objetivo final de lograr un mecanizado desatendido durante todo el fin de semana. Acercarse a este objetivo requería múltiples cambios que reforzaran la repetibilidad del mecanizado sin luz, desde el establecimiento de redundancias de máquinas y herramientas hasta la experimentación de estrategias de sujeción.
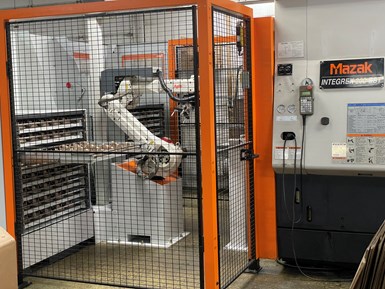
MTH Pumps consigue una automatización sin luz durante la noche mediante el emparejamiento de sus 12 Mazak Integrex con pórticos de carga automática. Una Integrex también está emparejada con un robot de asistencia a la máquina de Agile Robotic Systems, y la combinación de robot de asistencia a la máquina y cargador de pórtico amplía las operaciones sin supervisión de esta máquina durante el fin de semana.
Redundancias insustituibles
Antes del impulso de perfeccionamiento, MTH Pumps tenía un taller de dos turnos cinco días a la semana, con un tercer turno de automatización sin luz. Ampliar esta automatización durante el fin de semana requería dos cambios fundamentales.
En primer lugar, la empresa necesitaba programar las sondas Renishaw RMP600 de sus máquinas para que determinaran automáticamente cuándo realizar los cambios de herramientas redundantes. Con este fin, las sondas miden las piezas y activan la compensación del cortador y los ajustes de longitud de la herramienta para tener en cuenta el desgaste de esta, remecanizando las características de la pieza inmediatamente si están fuera de tolerancia.
Cuando la herramienta alcanza un determinado límite global de ajuste del tamaño de la herramienta, la máquina realiza un cambio de herramienta redundante y pone a cero el límite de ajuste.
El segundo cambio se basa en el primero: MTH necesitaba almacenar suficiente herramental redundante en cada máquina para asegurarse de que pudiera funcionar el mayor tiempo posible, ya sea durante la noche o desde el cierre del viernes hasta el comienzo del primer turno del lunes.
Un consultor independiente ayudó a MTH a realizar la primera tarea de forma sencilla. A primera vista, las máquinas Integrex, de MTH Pumps, parecía que harían la segunda tarea —proporcionar herramental redundante para largos tramos de mecanizado sin luz— igualmente sencilla. Dependiendo del modelo, las máquinas Integrex contienen almacenes de 110 o 120 herramientas, y el costo de suministrar herramental redundante no era una gran preocupación dado el aumento de la producción que estas herramientas permitirían.
Los retos surgieron de los metales duros que la empresa mecaniza. Mientras que la automatización de las piezas de bronce durante el fin de semana no requiere muchos cambios de herramientas, las piezas de acero inoxidable (como las de la bomba de freón) y las de hierro fundido consumen herramientas a un ritmo mucho mayor. ¿Otra dificultad? Aunque las Integrex tienen grandes almacenes de herramientas, el aumento de la productividad requiere que todas las piezas sean compatibles con dos o tres máquinas, de modo que la producción pueda flexibilizarse para los grandes pedidos o compensar los tiempos de inactividad por mantenimiento.
Como parte de la garantía de compatibilidad, cada máquina que pueda ser asignada a una pieza específica debe contar con el herramental y los programas para esa pieza. Para ello, la empresa ha estandarizado sus mezclas de herramental en todas las máquinas, con ubicaciones de herramientas idénticas entre las máquinas siempre que sea posible.
Tremain dice que las máquinas que trabajan con piezas de acero inoxidable aún no han completado un fin de semana entero de producción sin supervisión, pero su éxito al duplicar el tiempo de ejecución durante la noche y triplicar el tiempo de ejecución durante el fin de semana ha sido un impulso significativo para la utilización y la productividad de MTH.
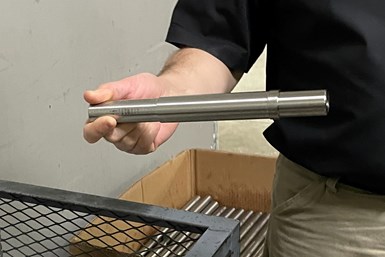
Aunque las máquinas multitarea de MTH pueden realizar el taladrado profundo vital para producir ejes de bombas de freón, Tremain describe el uso de la Integrex de 12” de chuck para mecanizar un eje de 1” de diámetro como “excesivo”. Por ello, el OEM busca máquinas de tipo suizo con capacidad de taladrado profundo para producir la pieza.
Consolidación y tiempos de ciclo
Al frente de este esfuerzo de estandarización y optimización está Charlie Ruetsche, freelancer que dirige la empresa de consultoría Refined Manufacturing. Ruetsche es un antiguo ingeniero de aplicaciones de Mazak, lo que le hace idóneo para mejorar la repetibilidad del programa y los tiempos de ciclo en las Integrex de MTH.
Los primeros perfeccionamientos de Ruetsche para la bomba de freón comenzaron con los esfuerzos de consolidación de herramientas de MTH, durante los cuales programó las operaciones de palpado y experimentó con diferentes insertos y geometrías para encontrar la mejor combinación de rendimiento y durabilidad en cada operación.
Asimismo, ha perfeccionado los programas de la empresa mediante las funciones avanzadas de su software CAM ESPRIT, como el fresado de beneficios, que crea programas de desbaste con un ligero compromiso radial y una profundidad de corte total para reducir los tiempos de ciclo y mejorar la vida de la herramienta.
Estos perfeccionamientos del herramental y de la programación han permitido mejorar enormemente el tiempo de ciclo. Alcanzar el objetivo de 75 bombas de freón al día solía ser imposible —incluso con la automatización nocturna—, ya que las operaciones de mecanizado solo para la carcasa duraban 62 minutos por pieza. Las alteraciones de Ruetsche redujeron los tiempos de ciclo de esta pieza casi a la mitad y hacían que el objetivo del OEM fuera alcanzable con dos máquinas trabajando simultáneamente en la pieza.
Según los datos de MTH de marzo de 2022, los perfeccionamientos de la automatización de la empresa han dado como resultado un aumento del 60 % en los soportes del motor, las cubiertas y los impulsores por hora de trabajo, y hay más por venir.
Apilar un conjunto completo
La mayoría de los cargadores de pórtico de MTH utilizan un sistema de mesa de estilo apilador o de estilo pallet. Los sistemas de mesa de pórtico de estilo apilador pueden sostener materia prima apilable, como las piezas en bruto de los impulsores, de las que caben hasta 320 a la vez.
Los sistemas de mesa de pórtico de estilo pallet con tableros de anidamiento sostienen piezas fundidas no apilables, como cubiertas y soportes de motor. En la mayoría de las máquinas, los tableros del sistema tipo pallet solo pueden albergar hasta 36 piezas a la vez.
La máquina con el robot de seis ejes amplía el sistema de estilo pallet a uno de bandejas de estilo cajón que alimenta las piezas no apilables al robot de pórtico, que luego carga la máquina. MTH utiliza actualmente este sistema de estilo cajón para facilitar la producción de hasta 320 cubiertas o soportes de motor a la vez, para su modelo más pequeño de bomba de turbina regenerativa.
Si bien el sistema de cajones le permite producir tapas o soportes de motor sin luz durante el fin de semana, en una proporción de uno a uno con los impulsores, aún debe mecanizar el componente de la carcasa correspondiente durante la semana debido a las diferencias de sujeción entre la tapa y el soporte del motor. Esto obliga a MTH Pumps a mantener los dos lotes de 320 componentes en el inventario hasta que se complete el lote de componentes restante.
Tremain afirma que el siguiente paso para optimizar la configuración del sistema de sujeción de su empresa es asegurarse de que sus tapas y soportes de motor se fabrican en una proporción totalmente proporcional.
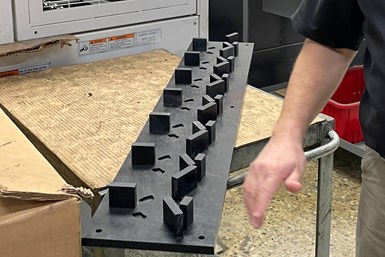
MTH Pumps diseña y mecaniza internamente algunos de sus tableros de pórtico personalizados.
Para ello, la empresa planea colocar más de un tipo de componente en cada tablero de pórtico anidado. Aunque los tableros de pórtico estándar no están diseñados para su uso con múltiples piezas, MTH ya está acostumbrada a utilizar tableros de pórtico personalizados con ranuras para encajar los pies de las piezas. Cuando visité MTH en marzo de 2022, su personal de ingeniería interno había desarrollado un patrón prototipo para el tablero de pórtico multicomponente y fabricaba tableros de pórtico de prueba con un pequeño centro de fresado en su sala de herramientas.
En última instancia, MTH espera poder montar las dos mitades de una carcasa de bomba en el mismo tablero de pórtico, y alternarlas. Siempre que la sujeción y las pinzas del cargador de pórtico sean las mismas entre las piezas —y siempre que el centro de mecanizado tenga la programación y la mezcla de herramental adecuadas— esto podría hacerse realidad.
Si el fabricante de equipos originales puede dar un paso más y añadir impulsores, entonces podría incluir una unidad completa en sus cargadores de pórtico. Esto supondría un gran cambio para el inventario de MTH Pumps, puesto que la empresa ya no necesitaría mantener un stock de piezas extra a la espera del resto de componentes.
El factor P es el factor X
En el periodo transcurrido entre la auditoría de utilización inicial de MTH Pumps y mi visita, el fabricante de equipos originales ya había aumentado los índices de utilización de sus máquinas del 25 al 30 %. Un aumento del 5 % puede no parecer mucho, pero junto con una reducción del 50 % del tiempo de ciclo en varios componentes principales, esto ha dado lugar a un gran impulso de la productividad.
Esta marcada diferencia entre la utilización y las mejoras del tiempo de ciclo es en realidad bastante normal, dice Robert McCrory, director de operaciones de MTH. Explica que hasta que la demanda aumente, las reducciones del tiempo de ciclo pueden hacer que la utilización parezca desfavorable al reducir la cantidad de tiempo que la máquina tendrá que funcionar para obtener la misma producción.
Por tanto, ni la utilización ni el tiempo de ciclo son por sí mismos una métrica perfecta para medir la mejora de MTH Pumps. Por ello, McCrory ha empezado a preferir una métrica que mide las piezas producidas por hora de trabajo, a la que llama “factor P”. Según los datos de MTH de marzo de 2022, los perfeccionamientos de la automatización de la empresa han dado lugar a un aumento del 60 % en el factor P de los soportes del motor, las cubiertas y los impulsores, y aún hay más por venir.
“Probablemente tenemos menos operarios ahora que en los años ochenta —dice Tremain, en referencia a los primeros días de los esfuerzos de automatización de MTH Pumps—. Pero hoy fabricamos fácilmente 15 veces más piezas”.
Contenido relacionado
Cómo maximizar los procesos de mecanizado en duro
Este informe recopila algunos de los aspectos críticos que deben considerarse al realizar procesos de fresado en duro. Herramientas dedicadas, portaherramientas precisos, software CAM especializado y una máquina robusta son los componentes esenciales para lograr los mejores resultados.
Leer MásQué es el torno fresado y cómo lo puede aplicar en su taller
Explore cómo el torno-fresado puede mejorar la eficiencia en la eliminación de metal y el manejo de cortes interrumpidos.
Leer MásMazak presenta avances clave en tecnologías de mecanizado en IMTS 2024
En la IMTS 2024, Mazak destacó tres innovaciones en su línea de máquinas-herramienta: el centro de mecanizado horizontal HCN-4000 Neo, el torno multitarea HQR 200/3 Neo y la serie de máquinas tipo suizo Syncrex 25/8. Estas tecnologías están diseñadas para maximizar la productividad y precisión en una amplia gama de aplicaciones, desde la producción de piezas pequeñas y complejas hasta el mecanizado pesado.
Leer MásCinco estrategias para el éxito en el mecanizado aeroespacial
El mecanizado aeroespacial es un sector de la manufactura exigente y competitivo, pero este taller demuestra cinco formas de alcanzar el éxito en el sector aeroespacial.
Leer MásLea a continuación
Cuando el mecanizado desatendido no deja cabos sueltos
Este taller se esfuerza por garantizar que cada parte cruce su patrón con un robot, cobot o cambiador de pallets.
Leer MásLos efectos desatendidos de la automatización en un taller de mecanizado CNC
El mecanizado automatizado y la recolección de datos han ayudado a Custom Tool no solo a hacer crecer su negocio mediante más producción desatendida, sino también a establecer un pensamiento de mejora continua que le ha permitido ser más eficiente en numerosas áreas.
Leer MásMaquinado desatendido, ¿mito o realidad?
Es aconsejable tener tiempos de ciclo prudentes para garantizar la fiabilidad del mecanizado sin la supervisión de un operador. Lograr este nivel de fiabilidad implica reducir la velocidad para un maquinado estable.
Leer Más