Digitalización de máquinas-herramienta: entre oportunidad y desafío
Al buscar soluciones tecnológicas, la atención de los talleres metalmecánicos se centrará en formas prácticas para salir de la crisis, en el crecimiento de las ventas y el ahorro de costos, todo esto a través de una mayor productividad y eficiencia de los sistemas y máquinas que les permita prepararse para la reactivación.
Compartir
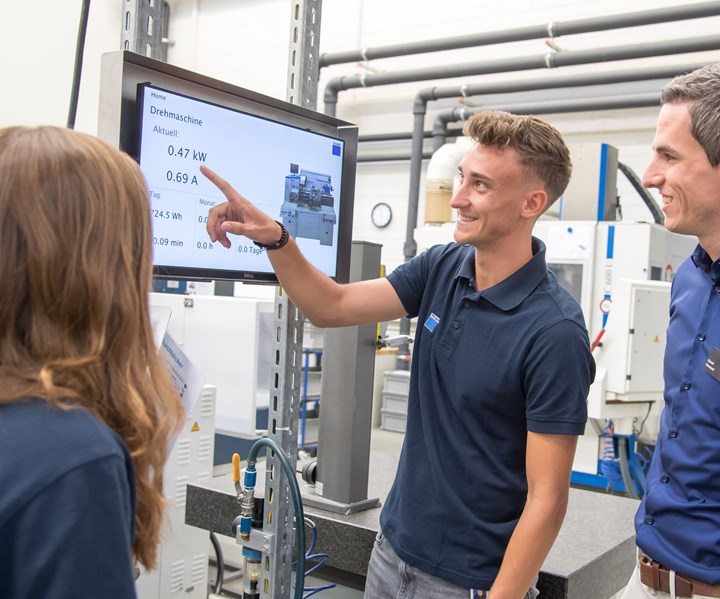
Los aprendices aprenden cómo las soluciones digitales mejoran la producción en el centro de capacitación TRUMPF. Foto: Grupo TRUMPF.
En medio de la crisis por coronavirus, y entre las restricciones al movimiento y al contacto, una palabra clave que parece ser un remedio universal para la industria y la economía está dando vueltas: la digitalización.
La importancia de las herramientas digitales conocidas para la comunicación y la visualización remota está aumentando significativamente a la luz de la necesidad de aislamiento y distanciamiento físico, y se están utilizando en todos los sectores económicos.
La industria conoce desde hace tiempo el potencial de la digitalización. Las esperanzas y los objetivos son variados, ya sea el desarrollo más rápido de máquinas más flexibles, una mayor confiabilidad y un mantenimiento sin problemas (remoto), una mejor documentación, un mayor grado de automatización, y la capacidad de autoaprendizaje: la lista de posibilidades es infinita.
Cuando se enfrentan a los desafíos actuales, muchas personas desearían que se hubiese avanzado más en la digitalización y en la expansión de las redes necesarias, como el nuevo estándar de radio móvil 5G.
“El 5G industrial abre la puerta a la extensa red inalámbrica de producción, mantenimiento y logística. Las altas tasas de datos, la transmisión extremadamente confiable y los períodos de latencia ultracortos permitirán un aumento significativo en la eficiencia y una mayor flexibilidad en el valor agregado industrial”, dice Eckard Eberle, CEO de Siemens Business Unit Process Automation.
Eberke es responsable del Centro de Pruebas 5G de Siemens. De hecho, una máquina-herramienta (todavía) no se puede ver aquí, pero el camino para la red inalámbrica de la fábrica del futuro está claramente trazado. En los últimos meses, Siemens ha estado probando la banda de frecuencia de 3.7 - 3.8 GHz en Nuremberg con componentes logísticos en un entorno industrial real, por ejemplo, con controles Simatic y dispositivos IO.
Para determinar, por ejemplo, las fuentes de errores para problemas de calidad con piezas de trabajo de forma libre, Siemens utiliza un software que analiza todos los puntos neurálgicos de la cadena de procesos y verifica las estaciones entre el sistema CAD y las herramientas utilizadas.
Porque las fuentes de errores pueden ser múltiples: la salida del sistema CAD en sí, la salida del sistema CAM o el postprocesador, la configuración de parámetros del CNC y el controlador de accionamiento, la mecánica de la máquina, las herramientas, el agente de enfriamiento, y en teoría incluso el material de la pieza de trabajo.
El programa Analyze MyWorkpiece/Toolpath verifica los datos de salida de las partes individuales del sistema, como el archivo STL del sistema CAD, el archivo MPF del sistema CAM o el post-procesador, la grabación de los valores de posición y, finalmente, cómo la unidad de control y la mecánica de la máquina, así como la herramienta, implementaron los datos. De esta forma, el aseguramiento de la calidad de los datos CAD/CAM de piezas de trabajo de gran formato ya puede realizarse antes de la producción.
Estos sistemas de optimización en las proximidades de la máquina-herramienta también desempeñarán un papel importante en las ferias que se aproximan, como la AMB 2020. Sus organizadores proyectan que en septiembre, fecha programada para este evento, la atención se centrará en encontrar formas prácticas de salir de la crisis, así como en el crecimiento de las ventas y el ahorro de costos, particularmente a través de una mayor productividad y una mayor eficiencia de los sistemas y máquinas, en preparación para cuando se llenen nuevamente los libros de pedidos.
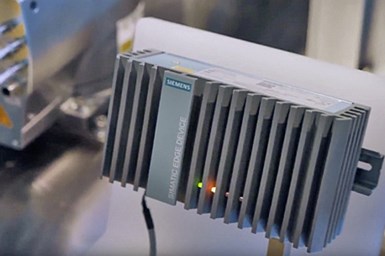
Edge Computing en las proximidades de la máquina es discreto, como este Edge Device de Siemens. Foto: Siemens AG.
Con nuevas soluciones como Edge Computing, la digitalización ofrece diversas oportunidades en los entornos de producción heterogéneos del sector metalmecánico. Pero también hay numerosos desafíos. Para que la digitalización esté disponible en todos los ámbitos, necesita estándares, dice Markus Horn, director gerente, de Paul Horn GmbH:
“La VDMA está promoviendo el problema en el marco de GTDE. Con mucho gusto acojo esto y, como empresa, estamos también desempeñando nuestro papel poniendo a disposición los datos correspondientes", agrega.
GTDE es la abreviatura de Graphical Tool Data Exchange-Standard Open Base e.V y actúa como centro de competencia, partes interesadas y proveedor de servicios en el área de intercambio de datos de herramientas. Los miembros y socios de la asociación incluyen fabricantes y usuarios de herramientas conocidos, compañías de software y la Asociación de Herramientas de Precisión (VDMA).
El objetivo es diseñar el intercambio de datos de la herramienta de una manera orientada hacia el futuro a través de estándares reconocidos internacionalmente, así como apoyar a las empresas relevantes en esta área. La asociación apoya la implementación para el intercambio de datos de herramientas y, por lo tanto, la provisión estandarizada de datos de herramientas a través de la operación de un servidor separado, a través del cual los fabricantes participantes pueden organizar la verificación de datos de herramientas, como propiedades de herramientas, gráficos 2D y 3D de acuerdo con DIN e ISO y hacer que los datos de la herramienta estén disponibles de forma gratuita.
Pero Horn también aclara: “El dinero se gana al límite. Complementado, no reemplazado, por medios digitales. Para nosotros, como fabricante de herramientas, esto significa: si la herramienta no ofrece la calidad y precisión que se requiere, entonces la digitalización tampoco ayuda”, señala.
En la actualidad, hay una gran cantidad de jugadores en el mercado que ofrecen servicios digitales: fabricantes de software, fabricantes de máquinas o fabricantes de herramientas. Sin embargo, sin estándares, generalmente es complejo y costoso realizarlos para el cliente y tampoco son flexibles en su uso.
“Los productos o servicios complementarios digitales solo deben usarse donde haya un beneficio real. En el futuro, también nos centraremos en la herramienta en sí, poniendo a disposición los datos correspondientes y ofreciendo soluciones digitales para las aplicaciones donde tendrán un efecto beneficioso”, dice Horn.
Sensores sensibles
Un objetivo importante donde las soluciones digitales pueden ayudar es en minimizar los rechazos. Por ejemplo, Paul Horn GmbH, junto con el Grupo Kistler, está explorando problemas en el mecanizado en forma de materiales defectuosos, materiales de corte desgastados o roturas de herramientas.
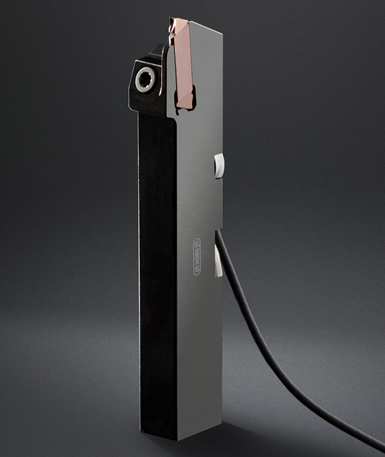
El sensor piezoeléctrico proporciona información sobre el estado de la herramienta durante el proceso de mecanizado y mide fuerzas de corte muy bajas con alta resolución. Foto: Paul Horn GmbH
Los expertos en tecnología de medición dinámica registran la presión, la fuerza, el par y la aceleración y, en estrecha colaboración con los ingenieros de Horn, han desarrollado una solución para el monitoreo en tiempo real de herramientas de micro-torneado. El sistema Piezo Tool (PTS) está compuesto por un sensor de fuerza que se inserta en la herramienta de torneado y proporciona información sobre el estado de la herramienta durante el proceso de mecanizado.
El sensor piezoeléctrico extremadamente pequeño mide fuerzas de corte muy bajas con alta resolución. El sistema es adecuado para su uso en aplicaciones de torneado, especialmente en el rango micro. Los métodos de medición alternativos, como el monitoreo de la potencia de accionamiento del motor del husillo principal, no son muy productivos debido a las pequeñas desviaciones.
Una medición del ruido transmitido por la estructura tampoco proporciona resultados satisfactorios constantes para piezas de trabajo pequeñas. El monitoreo visual también se descarta debido al uso de lubricantes refrigerantes, así como a las altas velocidades de rotación durante el proceso de mecanizado. La nueva solución no requiere ninguna intervención en los sistemas CNC y su aplicación es independiente de la máquina. Como resultado, los costos de producción de PTS se reducen y las capacidades de producción aumentan.
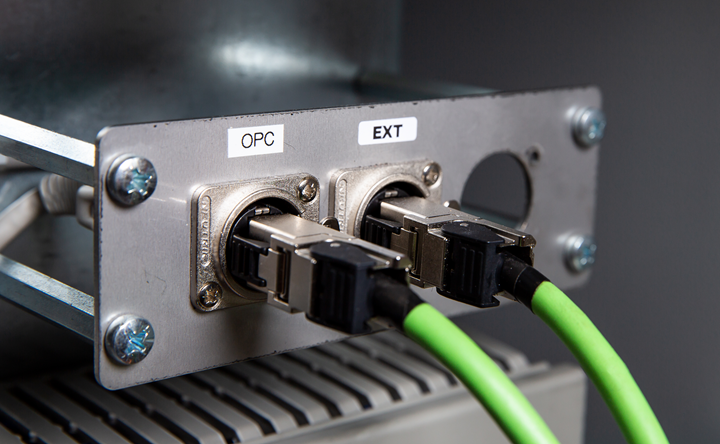
Horn utiliza OPC UA como un estándar global importante para la Industria 4.0 en el área de recubrimiento. Foto: Paul Horn GmbH
Rutas cortas hacia el cliente
Los fabricantes de máquinas también abordan la conciencia y la eficiencia de los costos. “La necesidad de productos digitales está acompañada por el fuerte enfoque de nuestros clientes en procesos eficientes. Las soluciones basadas en digital, entre otras, ayudan a mejorar la estructura organizativa de nuestros clientes. Los períodos de eliminación de fallas más cortos son tanto un problema como una mayor disponibilidad de la máquina”, dice el director gerente de Burkhardt y Weber, Olaf Furtmeier.
La ventaja de una empresa mediana es tener rutas cortas, abordar proyectos de desarrollo en equipos ágiles con el fin de aportar la mayor cantidad de puntos de vista posibles al proceso de desarrollo. “Sin embargo, es esencial buscar ayuda de socios calificados. Solo de esta manera podemos garantizar que se implemente una gama completa de conocimientos en los productos para producir un producto final que realmente ofrezca un valor agregado y, por lo tanto, también sea comprado por nuestro clientes ", agrega Furtmeier.
La comunicación fluida entre los elementos de producción individuales es también la base de la digitalización y la Industria 4.0 en Zoller cuando se trata de la configuración, medición y gestión de herramientas.
Hoy en día existen muchas rutas confiables y rápidas especialmente para el camino de transmisión de datos desde la herramienta de ajuste hasta la máquina. Los datos reales de la herramienta se preparan de manera fácil para el control de la máquina respectiva y se transfieren directamente por el dispositivo de ajuste y medición al sistema CNC. El software convierte los valores de medición en un formato relacionado con el control específico de la máquina y los genera. El software contiene una biblioteca de más de 230 formatos de salida estándar para varias máquinas.
Transferencia de conocimiento y entrenamiento
La razón por la que la digitalización se extendió relativamente tarde en la industria de las máquinas-herramienta y en el trabajo del metal, en comparación con otras industrias, radica no solo en los costos o el esfuerzo de la implementación, sino en que requiere nuevas formas de pensar y enfoques de los empleados en todos los ámbitos.
Trumpf demostró cuán importante es el tema de la transferencia de conocimiento y la capacitación para abordar la digitalización desde cero al comienzo del año: para adaptarse al cambio digital, Trumpf depende de las redes y capacita a su personal junior para primera vez a través de un “Entrenador de Industria 4.0”.
El programa coordina todo el contenido digital de los diversos campos de capacitación y apoya a los aprendices y estudiantes duales. “La digitalización se convertirá en un componente fundamental de la capacitación en nuestra empresa. Cualquier persona que estudie TI o complete un curso de capacitación en el área debe comprender lo que hace el ingeniero mecánico. Al mismo tiempo, el ingeniero mecánico debe saber qué software se necesita para la máquina en particular. Esto está creciendo en conjunto con la gestión empresarial, que debe incluir, por ejemplo, piezas de chapa y software para el cálculo de la máquina”, dice Katja Tiltscher, Gerente de Capacitación de Trumpf.
Contenido relacionado
Claves para comprender el proceso de escariado
El proceso de escariado es una técnica crítica para alcanzar la máxima precisión y acabado superficial en la producción de agujeros. Este informe explica el uso y las características de las herramientas de escariado, resalta los avances tecnológicos que han influido en este proceso y las estrategias que optimizan su aplicación para el mecanizado de piezas en diversas industrias.
Leer MásHerramientas de corte y portaherramientas para mecanizado desatendido
Conozca las nuevas características que ayuda a mejorar la estabilidad de la herramienta de corte, estandarizar el rendimiento y prolongar la vida útil de la herramienta.
Leer MásTipos de insertos de corte y su aplicación
Este informe ofrece una visión de los diversos tipos de insertos utilizados en el mecanizado de piezas metálicas y su importancia en los procesos industriales. Aborda desde los conceptos básicos hasta las aplicaciones específicas y las recientes tendencias tecnológicas. Además, profundiza en las propiedades técnicas, ejemplos de aplicaciones en diversas industrias y recomendaciones prácticas para maximizar la eficiencia y vida útil de los insertos.
Leer MásTIMTOS 2023: "Taiwán ha dado un paso adelante"
Con la presencia de la presidente de Taiwán, Ing-Wen Tsai, arrancó TIMTOS 2023 con más de 1,000 expositores de 18 países.
Leer MásLea a continuación
Comunicación 5G: datos que viajan a toda velocidad
Las redes móviles de quinta generación (5G) ofrecen beneficios inmejorables para los usuarios industriales, facilitándoles planificar su camino en el viaje hacia la Industria 4.0. La llegada de la red 5G a México es un evento esperado con anticipación.
Leer MásPor qué los talleres en México usan tornos tipo suizo
En México, el uso de tornos tipo suizo ha venido en crecimiento. Si bien empezó con aplicaciones dedicadas a la industria de la joyería y médica, ahora se utilizan para diversas aplicaciones en las industrias automotriz, electrónica, aeroespacial y de petróleo y gas.
Leer MásSistemas innovadores de sujeción para electroerosión y mecanizado de tres ejes
Con el propósito de aumentar el índice de ocupación de máquinas en el taller, este fabricante de moldes adaptó un dispositivo de sujeción en sus máquinas de tres ejes y su electroerosionadora de penetración para aumentar la flexibilidad de sus equipos y ser más competitivo.
Leer Más