Compartir
Lea a continuación
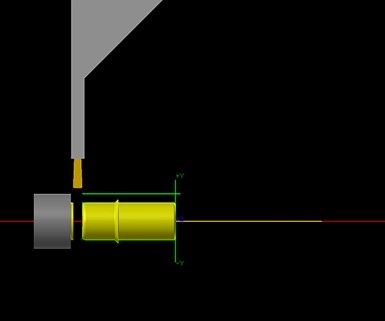
“Refrento el orificio del reductor con una herramienta de ranurado, torneo el diámetro exterior y lo termino con una herramienta de ranurado. Luego perforo los dos agujeros y termino”, dice Darren Vosper de U.K. Precision, quien realiza toda la operación a través de la función Verificar de Mastercam para asegurarse de que funcione.
Durante los últimos cinco años, el U.K. Precision Inc. se ha dedicado a la ejecución orificios reductores de latón para concentradores de oxígeno. En circunstancias normales, estas máquinas portátiles se utilizan para administrar oxígeno a las personas que tienen enfermedades relacionadas con la respiración, como en el caso de afecciones crónicas como asma o enfermedad pulmonar obstructiva crónica (EPOC), o incluso afecciones a corto plazo debido a cirugía o gripe. Recientemente, los dispositivos han jugado un papel crítico en el tratamiento de pacientes con COVID-19. Filtran el aire circundante, lo comprimen a una densidad específica y entregan oxígeno purificado al paciente a través de una cánula nasal o máscara. Sin embargo, el oxígeno puede fluir rápidamente, y los orificios reductores ayudan a regular su velocidad.
A medida que se incrementó la demanda de este equipo médico, U. K. Precision respondió. Este pequeño taller de Dallas, Georgia, fabrica piezas complejas en aluminio, titanio, acero inoxidable 17-4 y 18-8, y materiales exóticos, utilizando varios centros de mecanizado de tres a cinco ejes, una pequeña máquina de corte por plasma CNC, una rectificadora superficial y otro equipo manual. Mecaniza los orificios reductores de latón en su torno CNC Colchester Storm, programado con el software Mastercam CAD/CAM de CNC Software Inc.
“Es una pieza muy simple con dos diámetros exteriores, posterior y frontal, entre la brida que sella el diámetro interior del tubo flexible de media pulgada”, dice el dueño del taller, Darren Vosper. Debido a que los orificios del reductor son necesarios para el funcionamiento preciso del concentrador, deben ejecutarse según las especificaciones. Cada orificio regulador tiene un orificio # 17 (de 0.173 pulgadas de diámetro) en un extremo y un orificio # 50 (de 0.070 pulgadas de diámetro) en el otro. “La refrento con una herramienta de ranurado, torneo el diámetro exterior y lo termino con una herramienta de ranurado. Luego perforo los dos agujeros, lo separo y listo”, explica.
“La brida del diámetro exterior es acabada en un diámetro de 0.297 pulgadas, y estoy usando un material de 3/8 de pulgada, por lo que realmente no estoy quitando mucho material. Puedo mecanizarlo todo con una pequeña herramienta”.
Vosper tiene muchos años de experiencia trabajando con Mastercam. Con el tiempo, desarrolló un sistema mediante el cual agrega entradas de código manuales al final de sus programas, creando efectivamente sus propias publicaciones. “Sé que cuando saco el código de mi máquina, hago piezas rápidamente”. También agrega notas manuales debajo de cada trayectoria de herramienta. Observa la geometría de la pieza cuando comienza el proceso de mecanizado y la cantidad de material que se elimina en varias etapas, todo hasta el punto en que toca la parte delantera de la pieza después de refrentarla. En ese momento, él sabe hasta dónde puede alimentar el material a la máquina cuando se corta la última pieza. Incluso puede determinar cuántas piezas puede cortar, dependiendo de la longitud del material alimentado a la máquina.
“Lo agrego como una nota en mi archivo de geometría para que lo sepa de inmediato y pueda configurar y ejecutar la operación en menos de 10 minutos”, dice Vosper. Cada pieza tarda unos 90 segundos en mecanizarse.
Vosper pudo entregar el primer lote de 50 orificios reductores en dos días en lugar de la semana que había propuesto originalmente. Además, debido a que el montaje es tan sencillo, pudo producir 150 piezas adicionales al día siguiente, y 175 piezas después de eso usando el material restante.
“No estamos en la primera línea, pero nos complace hacer nuestra parte”, dice.
Proporcionando una mejor cobertura
Otro cliente de Mastercam, Century Mould, ubicado en Rochester, Nueva York, normalmente produce piezas para la industria automotriz. La compañía de moldeo por inyección se especializa en componentes debajo del capó para enfriamiento del motor, gestión del flujo de aire, sincronización del motor y para sistemas HVAC. Sin embargo, redirigió su trabajo cuando Rochester Regional Health llamó con una solicitud urgente de mejores máscaras protectoras para su personal médico. Usando Mastercam, el equipo de Century Mould diseñó rápidamente una nueva máscara que expande el área de protección envolviendo de oreja a oreja y cubriendo la cara del usuario, incluso más allá de la barbilla.
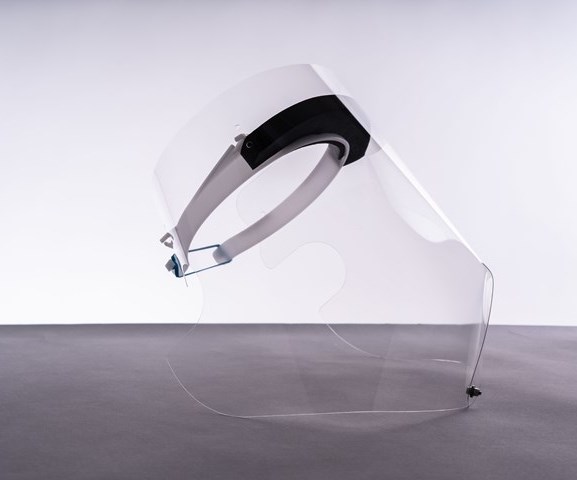
Century Mold usó Mastercam para diseñar una nueva máscara facial para brindar una mejor cobertura a los trabajadores de la salud locales.
En 24 horas, Century Mold tenía una máscara prototipada. Solo nueve días después de comenzar el proyecto, el moldeador por inyección comenzó la producción en masa de las mascarillas protectoras mejoradas. La compañía utiliza máquinas de tres y cinco ejes programadas con Mastercam para ejecutar sus pedidos. Actualmente, el taller funciona los siete días de la semana, produciendo 2,500 máscaras cada día. El objetivo es producir 1 millón de máscaras.
“Estamos agradecidos por todos los que están en la primera línea luchando contra el coronavirus y estamos felices de poder contribuir de alguna manera. También estamos extremadamente orgullosos y verdaderamente agradecidos por nuestro equipo de Rochester que ha estado trabajando interminables horas, poniéndose en riesgo y pasando tiempo lejos de sus familias”, dice Jeff Ricotta, Gerente de Desarrollo de Negocios.
Trabajando todo el día
Un cliente de Mastercam, desde su fundación en 1999, Mechanical Drive Components Inc. en Chicopee, Massachusetts, conoce bien lo que son los largos días de manufactura. El presidente y propietario, Joseph Giffune, a menudo realiza la mayor parte de la programación para fabricar piezas mecanizadas de precisión para las industrias médica, de equipos industriales, automotriz y aeroespacial.
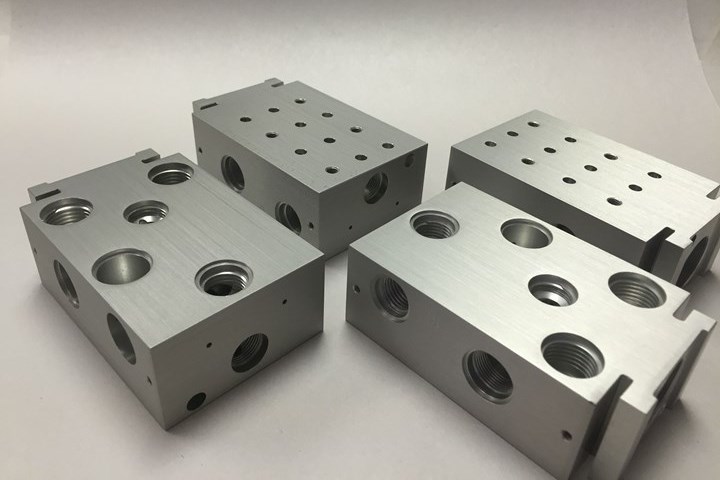
Mechanical Drive Components confía en el fresado CNC para producir mezcladores múltiples, que se utilizan en ventiladores mecánicos para cuidado médico.
El taller certificado con ISO 9001: 2015 y AS9100D mecaniza una variedad de materiales que incluyen aluminio, titanio, aceros inoxidables, plásticos, cobre, latón y bronce. Además de producir piezas, este taller contratista también ofrece procesos llave en mano para sus clientes, incluido el diseño de accesorios y procesos en Mastercam, la producción de accesorios, la programación de piezas en Mastercam y el muestreo de preproducción.
Recientemente, la compañía ha cambiado la mayor parte de su enfoque a la producción de componentes para su uso en dispositivos de mezcla de gases en ventiladores mecánicos utilizados para tratar pacientes con COVID-19. El taller ha estado funcionando los siete días de la semana con empleados que trabajan 60 horas cada semana. “Nuestro objetivo es permanecer en esto el mayor tiempo posible”, dice Giffune. En este momento, dice que el taller ha producido componentes para ventiladores durante los meses de junio y julio.
Aprendizaje gratuito disponible de Mastercam
Si bien muchos aspectos de la vida han cambiado drásticamente desde que surgió el coronavirus, el software CNC está tratando de recuperar la sensación de normalidad. Varios cursos en Mastercam University se han ofrecido de forma gratuita hasta el 30 de junio, junto con una descarga gratuita de Mastercam Home Learning Edition. Los cursos gratuitos incluyen: STEM – Principios de mecanizado, Mastercam Essentials, 2D Mill (Mastercam 2019 y 2020), 3D Mill (Mastercam 2019 y 2020) y Torno (Mastercam 2019 y 2020).
COMPAÑÍAS U.K. Precision Inc. Century Mold Mechanical Drives Component Inc. PROBLEMA: Era necesario para producir rápidamente componentes y suministros médicos. SOLUCIÓN: Software Mastercam CAD / CAM de CNC Software Inc. RESULTADOS: Los talleres pudieron adaptarse rápidamente a nuevas condiciones de trabajo |
Contenido relacionado
Actualización del software GibbsCAM con conectividad digital
GibbsCAM 2024 incorpora una serie de mejoras, incluida la conectividad digital, y se integra con la biblioteca de herramientas CoroPlus de Sandvik Coromant.
Leer MásSoftware CAD/CAM en IMTS 2024: potencia la precisión y la productividad
Las innovaciones de software CAD/CAM presentadas en IMTS 2024 hicieron hincapié en el papel fundamental que desempeñan las herramientas digitales avanzadas en la manufactura moderna.
Leer MásEl software CAD/CAM actualizado de Cimatron agiliza el diseño de moldes
La versión Cimatron V16, de Cimatron, cuenta con nuevas características en todas las áreas del producto, incluida una nueva interfaz de usuario limpia.
Leer MásCGTech, desarrollador de Vericut, celebra 35 años en el mercado
Según CGTech, Vericut fue el primer método ampliamente disponible para probar rutas de máquinas-herramienta en un entorno virtual.
Leer MásLea a continuación
Un posprocesador CNC resalta un torno-fresador de doble cabezal de herramientas
Una máquina multitarea con doble cabezal de herramientas hacía difícil, si no imposible, la coordinación de las trayectorias de herramienta. Un nuevo posprocesador para su uso con el Mill-Turn Mastercam dio como resultado una programación fluida de las trayectorias de herramienta con tolerancias estrechas para ambos cabezales.
Leer MásCómo alcanzar “la zona” en el mecanizado de cinco ejes
Al invertir en tecnología de mecanizado de cinco ejes, Advance CNC Machining ha hecho más que agregar nuevas capacidades a sus pendientes. Encontró una manera de lograr algo por lo que la mayoría se esfuerza: una forma de trabajar “en la zona”.
Leer MásPrograma de entrenamiento en máquinas CNC resocializa exconvictos en EE. UU.
Este programa de entrenamiento de operarios de máquinas CNC ayuda a personas con problemas a prepararse para un empleo sostenible y así reingresarse exitosamente en la sociedad y salir de la vida de pandillas.
Leer Más