4 consideraciones para el electropulido de partes mecanizadas
Los fabricantes que consideren este proceso de acabado sin contacto deberían esperar a hacer corridas de prueba y una colaboración cercana con los proveedores del servicio antes de comenzar la producción.
La corriente eléctrica generalmente supera los medios físicos en las operaciones de acabado final. Sin embargo, los talleres de metalmecánicos que consideren el electropulido deben ser cuidadosos para asegurar que las partes metálicas retengan niveles suficientes de material.
Según el proveedor Able Electropolishing, este proceso de acabado final sin contacto generalmente retira entre 0.0005 y 0.001 pulgadas de material. Qué tanto se retira depende de las metas del fabricante, que pueden variar desde lograr un cierto valor de rugosidad promedio (Ra), un acabado brillante, remoción de micro-rebabas, y/o pasivación para mejorar la resistencia a la corrosión, contaminantes o fatiga. Los fabricantes también deberían tener presente que la remoción de material con electropulido puede controlarse en el rango de 0.0001 a 0.0002 pulgadas. Al añadir este rango a las tolerancias de mecanizado se puede tener una indicación general de cuánto material dejar después del mecanizado.
Sin embargo, lograr el resultado deseado requiere pensar más allá de estos lineamientos generales. Otras consideraciones incluyen las siguientes:
Especificaciones de mecanizado
Los proveedores del servicio de electropulido deben entender cuáles áreas de una parte requieren la mayor precisión, porque el electropulido remueve material de forma indiscriminada. Los racks con las piezas de trabajo, cargadas positivamente para servir como ánodos, se sumergen en una solución de electrolitos junto con cátodos cargados negativamente. La corriente DC que fluye desde el ánodo hasta el cátodo retira diminutos fragmentos de material desde todas las superficies de la parte a la vez.
Según la geometría y otras características de la parte, la densidad de corriente en un punto dado en la superficie puede variar. Como resultado, algunas áreas de las partes montadas en el rack pueden desprender más material que otras. El diseño de fijaciones que asegure una densidad de corriente uniforme y evite dejar características críticas subdimensionadas –el verdadero arte del electropulido– requiere muestreo en preproducción.
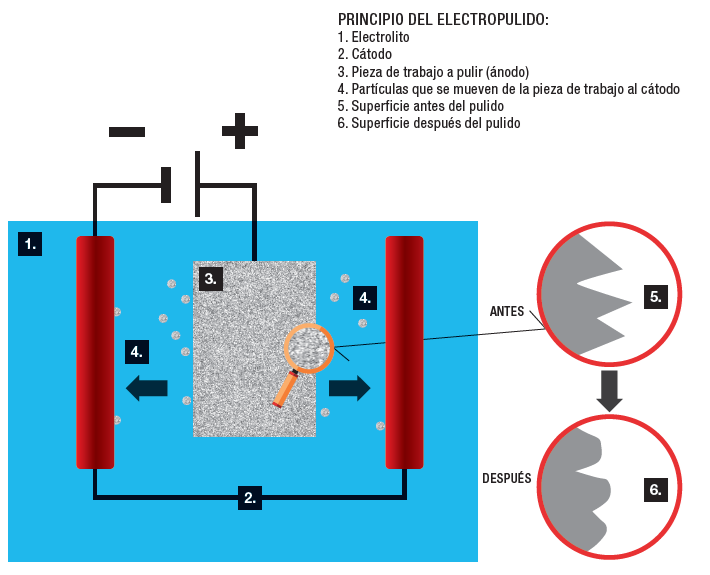
Principio del electropulido.
Material
El muestreo en preproducción también es crítico para revelar cómo reaccionan las diferentes formulaciones de aleaciones al proceso. Las aleaciones aptas para electropulido incluyen formulaciones con aluminio, bronce, materiales de cobre, acero al carbono, titanio y metales con base níquel y tungsteno. Generalmente, las aleaciones requieren retirar más material que las no aleaciones para lograr el resultado deseado, pero los niveles precisos dependen en gran medida de las especificidades de la formulación del material. Por ejemplo, una prueba fallida de resistencia a la corrosión por rocío salino después del muestreo puede llevar al fabricante a escoger una composición alternativa.

Aquí se muestra una cuchilla de un pelador de vegetales antes y después del electropulido.
Características deseadas de superficie
Decir que el electropulido brinda una “superficie suave y brillante” sería preciso, pero es importante distinguir entre esos dos términos. El efecto del electropulido en el brillo se afecta principalmente por la relación cromo a hierro del material. Sin embargo, una parte puede parecer brillante sin ser suave. La rugosidad promedio (Ra), una medida común de suavidad, se define por la distancia promedio entre los picos y valles microscópicos que constituyen todas las superficies.
El electropulido crea un efecto de nivelación (reduciendo así la Ra y haciendo
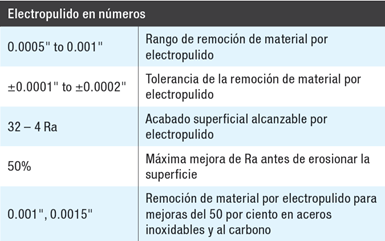
más suave la superficie) al recortar los picos. Entre más lento y más controlado sea el proceso, más suave será la superficie resultante. No obstante, no todas las partes brillantes deben ser suaves. Los fabricantes deben tener claras sus metas desde el principio.
Límites del nivel de material
Generalmente, entre más material se retire, mejores serán los resultados del electropulido, pero sólo hasta cierto punto. Una vez los picos de la superficie se han eliminado, la corriente comienza a cortar también los valles. La superficie comienza a erosionarse y se vuelve más rugosa, en lugar de más suave.
¿Qué significa esto para los talleres metalmecánicos? Entre más suave esté la parte antes del acabado, mejor será el resultado que puede lograrse con el electropulido. Por ejemplo, según el lineamiento del 50 por ciento en el cuadro de arriba, el mejor resultado posible con una parte que ha sido mecanizada hasta 32 Ra será 16 Ra. Si las especificaciones piden 8 Ra, la parte tendría que ser rectificada o pasar por otro proceso de acabado, para primero lograr por lo menos 16 Ra.
Basado en un artículo de Scott Potter, vicepresidente de ventas en Able Electropolishing Co.
Contenido relacionado
Herramienta de fresado de Trumpf proporciona una precisión repetible
La herramienta de fresado de cantos TruTool TKA 1500, de Trumpf, cuenta con características actualizadas para crear cantos de lámina con precisión repetible.
Leer MásHerramienta de Heule automatiza el proceso de desbarbado de agujeros cruzados
La herramienta COFA de Heule automatiza el desbarbado de orificios transversales, eliminando rebabas sin detener el husillo. Esta tecnología avanzada mejora la productividad en piezas con orificios difíciles de acceder, como horquillas y tubos con agujeros cruzados, proporcionando un acabado uniforme.
Leer MásClaves en el desbarbado de agujeros cruzados
Comparativa detallada entre herramientas neumáticas y mecánicas en el desbarbado con énfasis en la eficiencia y precisión para aplicaciones industriales.
Leer MásHerramientas de corte: demostraciones de tronzado extremo
Una mirada a los sistemas de tronzado de Iscar: comparativa entre Tang-Grip y Do-Grip. Ventajas, aplicaciones y resultados en condiciones extremas.
Leer MásLea a continuación
Entendiendo el electropulido
En comparación con otras opciones para desbarbar altos volúmenes de partes metálicas, se dice que este proceso es particularmente adecuado para las imperfecciones más pequeñas y las piezas de trabajo más frágiles.
Leer MásNuevas tendencias en instrumentos de medición e inspección
La precisión en la manufactura no es opcional, es una necesidad. Desde la integración de sistemas de medición en tiempo real hasta innovaciones en tecnologías sin contacto, la medición precisa resulta esencial para cumplir con las exigencias de tolerancias estrictas y optimizar los procesos de control de calidad. Exploramos los recientes avances en metrología y su impacto en industrias como la automotriz y la aeroespacial, donde la precisión es clave.
Leer MásMesas magnéticas optimizan la electroerosión en producción de piezas complejas
Evolución en Moldes venía asumiendo varios retos para el mejoramiento de sus procesos de manufactura de componentes complejos para sus moldes. La aplicación de mesas magnéticas optimizó el mecanizado por electroerosión y mejoró sus tiempos de entrega.
Leer Más