Si usted hubiera visitado Able Tool antes de 2003, un taller ubicado en el área de Cincinnati, nunca se hubiera dado cuenta de que fuera un taller que investiga de manera activa lo último en tecnología de manufactura. En ese entonces, una visita rápida al taller parecería como un equipo al estilo de un cuarto de herramientas. Sin embargo, eso comenzó a cambiar cuando Paul Hayes asumió la presidencia de la compañía.
Para impulsar el negocio, él sabía que la operación tendría que hacer un gran salto, adoptando mucho más que tecnología avanzada. Hoy, el taller de Able Tool consta de centros de mecanizado de cuatro y cinco ejes, y grandes electroerosionadoras horizontales y de hilo. Los husillos y las sondas de herramientas han reducido el tiempo de alistamiento en ese equipo y permiten la inspección en proceso para un control de proceso más efectivo.
El compromiso de la compañía de adoptar nueva tecnología no termina ahí. Hace unos seis años, Hayes decidió llevar la manufactura aditiva de un concepto que él había investigado a un proceso que él podría aplicar en su taller, pasándose rápidamente de la impresión 3D de partes plásticas a partes metálicas. Para estar seguro, hay un caso para imprimir cada tipo de material, dependiendo de la aplicación, dice él.
Aunque en ambos casos, Hayes cree que la tecnología aditiva le ha ayudado a su compañía a atender mejor a sus clientes al reducir el número de pasos necesarios para pasar del diseño a la parte producida. “Realmente, es apenas otra flecha de nuestra aljaba, por decirlo de alguna forma, hacer cosas de forma tan eficiente y rentable como sea posible”, dice él.
Para no adornarlo, invertir en manufactura aditiva fue un cambio arriesgado para Able Tool. Si bien existe un claro ROI para máquinas-herramienta más avanzadas y equipos relacionados, el ROI de la tecnología de aditivos es más oscuro, especialmente para un taller que no lo utiliza inmediatamente para la producción. Sin embargo, Hayes estaba decidido a asegurarse de que Able Tool estuviera en posición de ponerse al día nuevamente. Para adelantarse a la curva de aprendizaje aditivo, decidió dar un salto de fe.
Graduación en plásticos
Able Tool es un taller de fresado, mecanizado, fabricación y ensamble, que se especializa en una producción de alta mezcla/bajo volumen para una amplia gama de industrias, aplicaciones y materiales. Sus instalaciones cuentan con grandes fresadoras horizontales, centros de mecanizado vertical y tornos verticales. Cada vez más, el taller ha estado involucrado en ensambles completos de máquina, integración y prueba en lugar de sólo producción de partes individuales.
Aunque las capacidades aditivas son relativamente nuevas para Able, Hayes comenzó a investigar sobre la tecnología hace 15 años. Contrató incluso a una firma de consultoría para ver si la tecnología de impresión de metales en 3D era algo en que su compañía debería invertir, y dos grupos por separado le dijeron que no.
“Probablemente estaban en lo cierto, dado el ambiente de manufactura de ese momento, por lo que hace nuestra compañía y el valor asociado con la tecnología aditiva”, dice Hayes. “Ninguna de esas cosas se alineaba”.
Para no disuadirse, Hayes continuó estudiando la tecnología, convencido de su potencial. Hace seis años, decidió comprar una impresora de plásticos 3D MakerBot debido a que era una inversión relativamente baja, la máquina podía acomodarse en el escritorio de alguien y no se requería equipo auxiliar. Con el material plástico como único consumible, Hayes afirma que la MakerBot era una opción de bajo riesgo para aprendizaje práctico. Si una parte no resultaba según lo planeado, o si tenía que ser desechada, no tenía que preocuparse por tener que tirar un experimento de metal costoso.
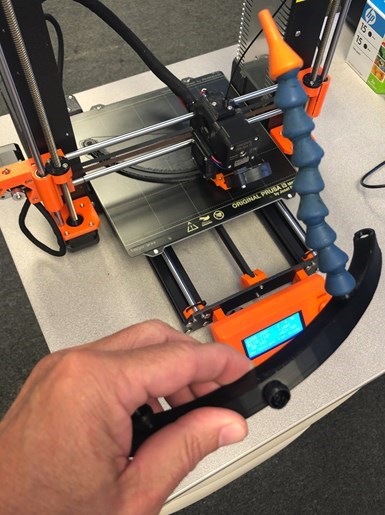
Esta fue la primera iteración de un anillo de refrigerante plástico impreso en 3D, de dos piezas, diseñado para distribuir mejor el refrigerante hacia la punta de la herramienta en la nueva mandrinadora de Able Tools. El problema es que el múltiple de refrigerante se asienta muy alejado del husillo, donde está la herramienta. Este dispositivo está diseñado para unirse a la manguera del husillo, permitiendo que el refrigerante fluya a través de su cámara interna y salga por los dos anillos en los cuales se unen mangueras flexibles Loc-Line. El refrigerante luego puede dirigirse de manera más eficiente a donde penetra la herramienta en el material.
Cuatro años después, Able invirtió en una impresora 3D Prusa para producir partes cercanas al uso final. Dos características principales llevaron a la compañía a adquirir la Prusa, dice el Gerente General, Mike Trovillo. Primero, puede imprimir más que una sola variedad de plástico. Segundo, su plataforma de construcción calentada mantiene el plástico tibio para evitar la deformación. La compañía ha usado esta máquina para hacer partes de uso final para sus clientes, como herramental del extremo de un brazo para robot y nidos de parte para una CMM.
Aunque en su mayoría, Hayes dice que él la usa como una opción de bajo costo para probar conceptos que le quitarían tiempo de otros trabajos en sus centros de mecanizado CNC o serían excesivamente costosos de hacer en metal. En algunos casos, la aplicación requiere solamente una solución plástica. Por ejemplo, durante mi visita, un practicante de verano estaba trabajando en la segunda iteración de un diseño para un múltiple de dos piezas que se uniría alrededor de la caja del husillo de una mandrinadora grande para ayudar a distribuir mejor el refrigerante al punto de corte, usando mangueras flexibles de refrigerante unidas a él.
Capacidad de imprimir metal
Después de adquirir experiencia con la impresión de plásticos y al ver la tecnología que estaba emergiendo, Hayes decidió que era el momento para dar el siguiente paso y comenzar a imprimir partes metálicas en 3D.
“Tuvimos que quitarnos el vendaje y por lo menos tratar de entender cómo podíamos usar la tecnología aditiva de metales y vendérsela a nuestros clientes”, dice él.
Aunque Able Tool se había estado preparando para este momento durante años, comprar realmente su impresora 3D Metal X de MarkForged fue un cambio súbito. Al final del año pasado, Hayes tomó la oportunidad de comprar la nueva máquina a Reynolds Machinery en Dayton, un nuevo distribuidor de MarkForged.
A pesar de la rápida sincronización, Hayes estaba confiado en que esta era la decisión correcta para su compañía. En lugar de escoger una máquina de sinterizado láser o de cama de polvo, la cual habría requerido un ambiente de laboratorio especial, la Metal X tiene una barrera de entrada más baja y puede hacer partes complejas en su volumen de construcción de 300- x 220- x 180 mm, dice él. Además de su experiencia imprimiendo plásticos, él sabía que quería la libertad de imprimir una amplia variedad de metales.
Actualmente, la Metal X puede imprimir acero inoxidable 17-4 PH, acero para herramientas H13 y A2, pero MarkForged planea añadir en el futuro cercano la capacidad para imprimir acero para herramientas D2, titanio, Inconel, cobre y acero inoxidable 316 (en el cual Able está particularmente interesado).
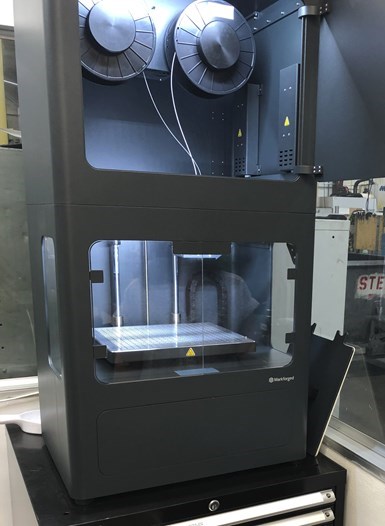
Metal X usa polvo metálico y cerámico para imprimir partes en 3D. El material viene en carretes de polvo contenido en plástico para facilitar su manejo y requerir un punto de fundición más bajo.
La Metal X es una impresora de fabricación de filamentos fundidos (FFF) que usa carretes de polvo de metal y un agente adhesivo contenido en una caja plástica. El segundo carrete es polvo cerámico contenido en una caja plástica. Trabaja alimentando esos carretes a través de un bloque calentador, donde se calientan hasta el punto de fusión de la caja y se alimentan a través de una boquilla de extrusión.
La boquilla primero deja capas de material mezcladas con cerámica donde sea necesario, lo cual actuará después como liberación de la parte (la cerámica también puede usarse para construir estructuras de soporte que, nuevamente, serán retiradas más adelante). La boquilla luego deposita el metal, construyendo la parte capa por capa.
La máquina usa láminas de impresión desechables que se mantienen abajo mediante una mesa al vacío para mejorar la adhesión de la cama y facilitar el manejo de la parte. Una vez se imprime la parte, el papel se retira fácilmente de la mesa de vacío. Los tamaños típicos de lote de Able Tool varían de una a cuatro partes. Sin embargo, Trovillo dice que si una parte es suficientemente pequeña, estima que podría acomodar hasta 30 partes en la placa de construcción. “Realmente depende del tamaño de la parte”, afirma. “Usted puede imprimir lo que sea que quepa en el volumen de construcción”. Las partes más pequeñas del taller se imprimen de dos a tres horas, mientras que las partes más grandes pueden tomar varios días, según la masa y complejidad de la parte.
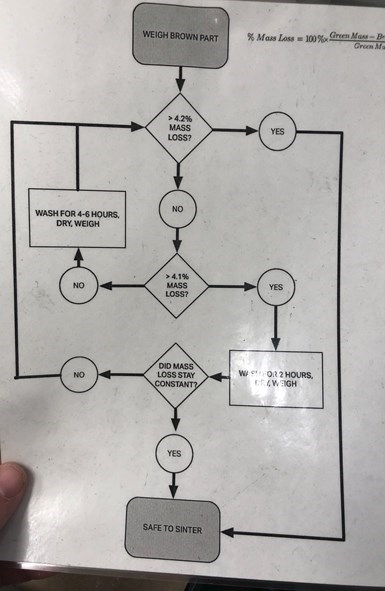
MarkForged ofrece este diagrama de flujo para guiar a los usuarios a través del proceso de lavado/sinterizado. Una parte impresa debe pesarse antes de pasar por el lavado, para comparar el porcentaje de masa perdida durante el proceso de lavado. Paul Hayes escribe el peso en la parte inferior de la parte para propósitos de trazabilidad. Si se pierde más del 4.2% de la masa, la parte puede sinterizarse. Si no, puede necesitar lavarse de nuevo.
Las partes impresas se pesan en una báscula digital antes de ser sumergidas en el sistema de lavado-calentado MarkForged Wash-1, donde el fluido de limpieza Opeteon SF-79 circula alrededor de las partes para romper la mayoría del plástico y el agente adhesivo de cera. Después del lavado, la parte secada por aire se pesa de nuevo para determinar si se ha retirado un porcentaje suficientemente alto del agente adhesivo. Si no, se devuelve al lavado para retirar más aglutinante. Si lo ha hecho, la parte se considera lista para ser sinterizada.
Las partes se ubican en una bandeja cerámica y se ponen en el MarkForged Sinter-1, el cual tiene un volumen de trabajo de 4,760 centímetros cúbicos. Aunque este es más pequeño que el volumen de construcción máximo de la Metal X, la compañía podría enviar partes a un proveedor externo para el sinterizado. El propósito del sinterizado, que toma alrededor de 25 horas, es fundir el metal en polvo para convertirlo en metal sólido. También hace cualquier cerámica impresa muy frágil. Una vez sinterizado, se puede romper la estructura cerámica de soporte de la parte y luego mecanizar para acabado si fuera necesario.
Para Hayes, una de las ventajas de usar la MetalX es que es básicamente un sistema preempaquetado: MarkForged suministró la impresora, el sistema de lavado y el horno de sinterizado, y dirige al taller en los detalles de cómo configurarlos, prestando atención especial a la ventilación, a la separación entre equipos y a los requerimientos de mezcla de gas para el sinterizado. MarkForged también ofrece su software de impresión 3D Eiger, que según Hayes es muy fácil de aprender.
Una vez una parte está diseñada en software CAD, su archivo STL puede cargarse al software Eiger, que usa algoritmos para compensar automáticamente la contracción que experimenta una parte durante el proceso de sinterizado. El software Eiger le permite manipular la parte y ver las dimensiones, tiempo de impresión, tiempo de lavado, tiempo de sinterizado, entre otros beneficios.
Un nuevo mundo de negocios con capacidades de manufactura aditiva
En una semana, tras la compra de la Metal X por parte de Able, la impresora comenzó a abrirles puertas a nuevos negocios. Un cliente del sector médico la vio durante un recorrido por el taller y comenzó a hacer preguntas sobre sus capacidades. Ese cliente no sólo le dio el trabajo de mecanizado que buscaba, sino que también le otorgó a Able un trabajo para imprimir un prototipo metálico para una parte, marcando la primera vez que la compañía hizo un trabajo para ese cliente.
Otros prototipos de clientes generalmente son el resultado de partes impresas por Hayes para sus clientes, como una sorpresa, para mostrarles lo que esta técnica de producción de partes alternativa es capaz de hacer. Pero, por ahora, Able utiliza la impresora Metal X para fijaciones personalizadas que se usan en el taller. Según Hayes, el uso intencional de la impresora 3D de metal ha sido un camino de crecimiento lento y orgánico. De hecho, el taller aún no promueve sus capacidades aditivas en su sitio web.
“Quiero ser capaz de ir a donde un cliente con certeza y decir que podemos producir la parte que quiera antes de promover oficialmente esa capacidad”, afirma.
Yendo más allá, Hayes espera usar las capacidades de impresión 3D, no para ir tras nuevos negocios per se, sino para solidificar la relación que tiene con sus clientes actuales ayudándoles a ver mejoras de diseño y formas de producir partes de manera más eficiente. Él cree que la refinación de la tecnología aditiva continuará hasta el punto en el que sea parte de la operación diaria de un taller.
Hayes predice que la mayoría de talleres metalmecánicos tendrán una impresora 3D en algún momento, así como tienen un VMC de tres ejes.
“Yo creo que la integración de tecnologías aditivas en el ambiente de un taller de subcontratación es cuestión de ‘cuándo’ y no de ‘si’”.
Necesitamos entender cómo usar estas herramientas para satisfacer las necesidades de nuestros clientes. Por eso es que compramos la máquina”.
Contenido relacionado
Manufactura aditiva: el papel de la tecnología de materiales
Descubra cómo la ciencia de los materiales potencia la manufactura aditiva, permitiendo la creación de estructuras complejas y personalizadas con precisión.
Leer MásEl futuro de la manufactura: aditiva vs. tradicional
Explore cómo la integración de la manufactura aditiva y sustractiva mejora la eficiencia y eleva la calidad en los procesos productivos, adoptando un enfoque híbrido innovador para la manufactura.
Leer MásSustentabilidad: clave para extender la utilidad de su máquina-herramienta
Las máquinas-herramienta ya adoptan algunos principios claves de la economía circular. La Asociación Europea de Fabricantes de Máquinas-Herramienta (CECIMO) analizó sus cualidades desde el diseño, el mantenimiento, el reequipamiento, el reacondicionamiento y el reciclaje de sus componentes que, además de extender la vida útil de estas máquinas, posicionan a sus fabricantes como pioneros en esta transición.
Leer Más6 elementos clave para que un taller metalmecánico se mantenga competitivo
Para optimizar la producción y seguir siendo competitivo en la industria, necesitará mucho más que una fresadora CNC de tres ejes, un torno CNC básico de dos ejes y algunas herramientas de medición. Conozca las herramientas esenciales que todo taller metalmecánico debe tener para mantenerse competitivo en el mercado actual.
Leer MásLea a continuación
Mesas magnéticas optimizan la electroerosión en producción de piezas complejas
Evolución en Moldes venía asumiendo varios retos para el mejoramiento de sus procesos de manufactura de componentes complejos para sus moldes. La aplicación de mesas magnéticas optimizó el mecanizado por electroerosión y mejoró sus tiempos de entrega.
Leer Más¿Por qué usar torno-fresado?
Los fabricantes de máquinas-herramienta se dieron cuenta de que las piezas torneadas a menudo requerían también, al menos, algún trabajo de fresado o taladrado. Por ello aumentaron las capacidades de los tornos mediante husillos adicionales para el trabajo con herramientas giratorias. De esa manera surgieron las máquinas de torno-fresado.
Leer MásPara qué sirve el fresado en duro
El fresado en duro se utiliza para mecanizar aceros endurecidos con filos cortantes definidos. El fresado de estos materiales requiere centros de mecanizado de alta velocidad configurados para el fresado en duro, junto con un CAD/CAM programado en concordancia.
Leer Más