A medida que la pandemia de COVID-19 se extiende por todo el mundo, las fábricas de manufactura enfrentan desafíos operativos significativos. Algunas compañías han cerrado temporalmente en respuesta a las restricciones gubernamentales o la caída de la demanda, pero otras enfrentan aumentos significativos en la demanda de suministros esenciales.
El personal de fabricación de primera línea no puede llevar su trabajo a la seguridad relativa de sus hogares. Por lo tanto, los líderes de las plantas están buscando formas de operar durante la crisis inmediata, todo mientras se preparan para un período mucho más prolongado de mayor incertidumbre sobre la demanda y la oferta, y una necesidad duradera de mantener una mayor higiene y distanciamiento físico.
Según la consultora McKinsey & Company, hay tres áreas de enfoque que pueden ayudar a los líderes de planta a navegar hacia la transición:
- Proteja a la fuerza laboral: formalice y estandarice los procedimientos operativos, procesos y herramientas que ayudan a mantener seguro al personal. Genere confianza en la fuerza laboral a través de una comunicación efectiva y bidireccional que responda a las preocupaciones de los empleados a través de una adaptación flexible
- Gestione los riesgos para garantizar la continuidad del negocio: anticipe los posibles cambios y modele la forma en que la planta debe reaccionar mucho antes de las fluctuaciones para permitir acciones rápidas y basadas en hechos.
- Impulse la productividad a distancia: continúe gestionando eficazmente el rendimiento en la planta mientras se mantienen las políticas de distanciamiento físico y trabajo remoto.
Proteger a la fuerza laboral
El enfoque más crítico para cada organización es mantener a los empleados seguros en un entorno donde los brotes repetidos son una amenaza persistente. Para lograr esto, las empresas pueden implementar un conjunto integral de políticas y pautas, que incluyen medidas de higiene mejoradas, provisión de equipos de protección personal (PPE) adicionales cuando sea necesario, distanciamiento físico y modificaciones a la gobernanza y los comportamientos existentes.
La protección de la salud mental de los empleados también ha surgido como una alta prioridad, con compañías en China (y en otros lugares) que brindan servicios de asesoramiento a los empleados que regresan después de cuarentenas prolongadas. Estas medidas, desarrolladas en la respuesta inicial a la crisis, se pueden integrar en los procedimientos estándar de una organización a medida que se realiza la transición a las operaciones normales.
La intensificación de las comunicaciones internas es de vital importancia, incluido el intercambio regular de información sobre la evolución de la empresa y cómo está utilizando ese conocimiento para proteger a los empleados y la organización. La frecuencia también cuenta, ya que el público necesita escuchar un mensaje repetidamente antes de absorberlo por completo. Y eso implica contenido consistente.
Finalmente, la mejor comunicación es bidireccional, con los gerentes respondiendo preguntas y entablando un diálogo abierto con los empleados en todos los niveles. Un fabricante de equipos, por ejemplo, pide a los supervisores que recopilen consultas y preocupaciones de los miembros del equipo de primera línea todas las mañanas. El departamento de recursos humanos de la compañía luego publica una lista actualizada diaria de preguntas y respuestas, que se muestran en los monitores de la fábrica. Después de la introducción de la nueva política, el absentismo entre el personal del taller cayó significativamente y la productividad volvió a los niveles anteriores a la crisis. Como un beneficio adicional no deseado, el enfoque descubrió una serie de preocupaciones de primera línea no relacionadas con la pandemia, permitiendo a los gerentes tomar medidas adicionales para aumentar la productividad y mejorar la satisfacción de la fuerza laboral.
Permitir el distanciamiento físico en el lugar de trabajo
Para mantener al personal seguro a largo plazo, las compañías pueden retener y formalizar las partes apropiadas de sus pautas de respuesta a emergencias, para que se conviertan en parte de los procedimientos operativos estándar de las plantas. Dichas pautas pueden incluir una mejor vigilancia de la salud, restricciones en el uso de herramientas y áreas comunales, desinfección regular de equipos junto con limpiezas periódicas profundas de lugares de trabajo completos y políticas de recursos humanos que aseguren que los trabajadores puedan quedarse en casa si no se sienten bien. Los cambios regulatorios también merecen atención adicional, ya que los gobiernos introducen nuevas reglas sobre el pago obligatorio por enfermedad, o requisitos para que los empleados limiten el contacto con los productos o entre ellos.
Al inicio de la crisis, algunas compañías comenzaron a pedirles a los empleados que realizaran una encuesta digital antes de comenzar a trabajar en el sitio, confirmando que no tienen ningún síntoma COVID-19, compartiendo su historial de viajes desde su último turno y verificando que entienden las nuevas pautas de salud y seguridad. Este enfoque proporcionó datos valiosos que podrían ayudar al rastreo de contactos (cuando sea coherente con las prácticas locales) en el caso de una prueba positiva en la planta. También ayuda a reforzar la importancia de seguir las políticas de salud y recuerda a los empleados que eviten el riesgo de enfermar a otros.
Reducir al mínimo el posible impacto futuro de las infecciones requerirá que las empresas modifiquen las estructuras del equipo y los métodos de trabajo para limitar el contacto en toda la fuerza laboral. Una forma de hacerlo es estableciendo “grupos o cápsulas” para todo el personal en el sitio, organizados por equipos independientes con tareas y espacios de trabajo claramente definidos que pueden separarse física y socialmente tanto como sea posible.
Los cambios organizativos para apoyar la introducción de las cápsulas incluyen la dedicación de los trabajadores a una sola línea de producción y la eliminación de los trabajadores “flotantes”, por ejemplo, al hacer que los miembros de las cápsulas sean responsables de recolectar materiales y realizar sus propios controles de calidad y mantenimiento.
Las reuniones de transferencia de turno se pueden llevar a cabo de forma remota, utilizando la tecnología de videoconferencia, mientras que los tiempos de inicio, parada y descanso de las diferentes unidades se pueden escalonar para minimizar el contacto en las áreas comunales de la planta. Las plantas incluso pueden optar por modificar los patrones de cambio, por lo que las líneas muy cercanas entre sí cuentan con personal y se ejecutan en diferentes momentos.
El Anexo 1 muestra cómo el enfoque de pod podría funcionar en una línea de empaque. Antes de los cambios, los operadores que trabajaban en la línea eran responsables de varias máquinas, respaldadas por personal de logística, calidad y servicios que trabajaban en varias líneas. Bajo el sistema de pod, los operadores están asignados a menos máquinas, pero son responsables de más tareas dentro de su área de trabajo, minimizando así el contacto con el personal y el equipo fuera del pod.
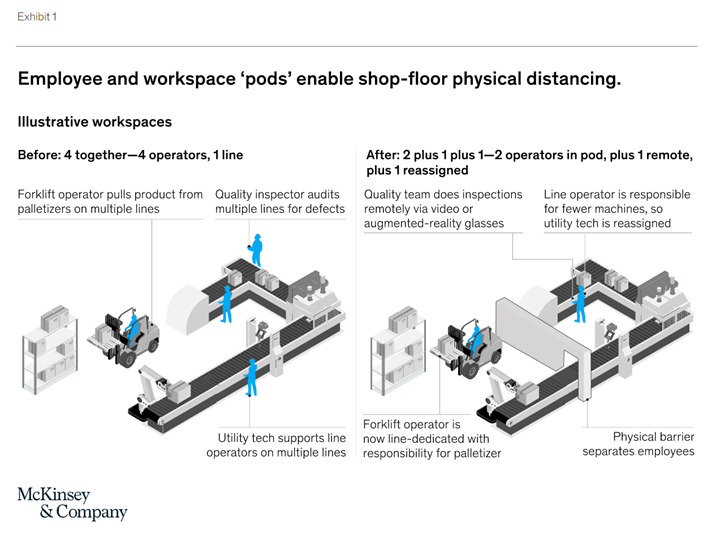
En lugar de que varios empleados manejen cada pallet, por ejemplo, un solo miembro del equipo es responsable de todo su viaje. Algunas tareas, como el control de calidad, ahora son realizadas por especialistas remotos, con la ayuda de cámaras y herramientas digitales. Las nuevas barreras físicas protegen contra el contacto accidental entre los trabajadores, al tiempo que permiten el movimiento sin trabas del producto.
Gestionar riesgos para garantizar la continuidad del negocio
La crisis del coronavirus ha aumentado drásticamente el riesgo para todas las empresas, y muchas experimentan choques tanto en la oferta como en la demanda. Las plantas de fabricación están en el centro de esa incertidumbre, y su operación continua durante la crisis y más allá dependerá en gran medida de la capacidad de la organización para sortear estos riesgos más amplios.
Los líderes de la planta pueden planificar su propia respuesta a los riesgos que podrían afectar directamente las operaciones en sus instalaciones, comenzando con qué hacer si un empleado en cualquier lugar de la planta da positivo por una infección por COVID-19. Las respuestas pueden incluir, entre otras, consultar con las autoridades sanitarias, poner en cuarentena a la persona afectada (junto con cualquier otro personal que trabajara en las proximidades) y aislar y desinfectar productos, herramientas y espacios de trabajo expuestos.
Enfrentando niveles más altos de incertidumbre a mediano plazo, las plantas probablemente encontrarán útil aumentar su planificación de escenarios, con una mayor cadencia de planificación y una gama más amplia de escenarios potenciales incluidos en su análisis. Cuando está estrechamente vinculada a la estrategia de respuesta y recuperación más amplia de la organización, esta planificación acelerada ayuda a la planta a desarrollar estrategias para acomodar materiales sustitutos o producir piezas internas difíciles de obtener.
Algunas compañías están utilizando gemelos digitales de sus instalaciones para simular la operación con diferentes niveles de personal y escenarios de producción. Este enfoque puede soportar muchos aspectos de la planificación operativa, desde evaluar el impacto de los cambios en el diseño de la planta hasta determinar la combinación de habilidades que requerirán los equipos en el sitio.
La transición a la próxima normalidad en las plantas de fabricación requerirá que tanto los líderes como los equipos de primera línea desarrollen nuevas capacidades. La introducción de las cápsulas en la línea de producción, por ejemplo, puede requerir operadores con una gama más amplia de habilidades, para que puedan completar todas las tareas requeridas en su cápsula o cubrir a los colegas ausentes.
Los nuevos enfoques digitales pueden acelerar el proceso de creación de capacidades y permitir a los empleados desarrollar nuevas habilidades de forma remota. Dichas técnicas incluyen la entrega remota de capacitación utilizando sistemas de aprendizaje electrónico o el uso de tecnologías de realidad virtual para familiarizar a los operadores con nuevas tareas o diseños de planta. Los sistemas de realidad aumentada ayudan al personal del taller a recibir capacitación, asesoramiento y apoyo de colegas remotos. Los contratistas especializados pueden usar dichos sistemas para guiar al personal de planta a través del mantenimiento de la máquina o la resolución de problemas.
Conduzca la productividad a distancia
Mientras la transmisión de virus entre los empleados siga siendo un riesgo, las empresas naturalmente querrán minimizar el contacto innecesario entre el personal. Cualquier persona que no sea absolutamente necesaria en el sitio, incluidos los gerentes y muchas funciones de soporte, puede ser alentada a trabajar lo más remotamente posible para proteger la salud de sus colegas en el taller. Para minimizar el riesgo de que toda una parte de equipo de liderazgo necesite entrar en cuarentena al mismo tiempo, el personal de liderazgo que necesita permanecer en el sitio puede separarse en al menos dos equipos, sin contacto físico entre ellos.
A medida que reconfiguran sus operaciones para mantener a los empleados seguros y responder a los cambios en la cadena de valor más amplia, las empresas necesitan mantener el rendimiento de fabricación. En muchas plantas, los líderes han manejado el desempeño cara a cara durante mucho tiempo, utilizando sesiones informativas diarias de turnos, gestión visual y "caminatas gemba" regulares, recorridos de observación en el taller y en cualquier otro lugar donde se esté haciendo el “trabajo real”. Las políticas de distanciamiento físico y trabajo remoto harán que estos enfoques establecidos sean más difíciles, obligando a las empresas a encontrar nuevas formas de gestionar el rendimiento en el taller.
La tecnología necesaria para respaldar estos cambios no necesita ser costosa. El personal que trabaja fuera del sitio puede usar programas seguros de acceso remoto desde sus dispositivos personales para manejar reuniones de transferencia de turnos y actividades similares. Algunas plantas han equipado a los operadores con radios bidireccionales, asignando canales a equipos específicos o grupos funcionales. Este enfoque en realidad puede aumentar la velocidad a la que se comunican y resuelven los problemas.
Ahora es un buen momento para que las empresas vuelvan a visitar los conjuntos de métricas que utilizan para realizar un seguimiento del rendimiento de fabricación. Para compensar el acceso reducido en persona al taller, algunos equipos de administración de fábrica ya están comenzando a identificar y rastrear los principales indicadores clave de rendimiento (KPI) además de los KPI estándar de primer y segundo nivel en los que generalmente confían.
El Anexo 2 ilustra este enfoque con una cascada simplificada de KPI de una línea de producción de alta velocidad. Cada uno de los KPI de rendimiento de nivel superior a la izquierda del gráfico se encuentra en una serie de KPI de segundo nivel que describen las principales fuentes de pérdidas experimentadas en la línea. Los principales KPI en la tercera columna siguen acciones acordadas previamente diseñadas para minimizar esas pérdidas.
El monitoreo de la frecuencia con la que los equipos de primera línea limpian, verifican y ajustan las partes críticas del equipo, tal vez utilizando sensores, si están disponibles, puede brindar a los líderes de equipo y gerentes de planta una advertencia temprana útil de posibles problemas antes de que debiliten el rendimiento operativo.
Históricamente, los gerentes dependerían de los líderes de línea para revisar estas actividades en persona, pero con solo un monitoreo remoto posible, estos puntos de datos pueden llenar los vacíos críticos de información para los gerentes. Por ejemplo, si la cantidad de veces que se limpian los rieles de alimentación comienza a caer en una línea de llenado, los gerentes pueden hacer un seguimiento con los operadores en lugar de esperar a que se produzcan atascos para reducir la efectividad general del equipo de la línea, el KPI estándar que los equipos de liderazgo suelen seguir.
A largo plazo, la respuesta de la organización a COVID-19 debería acelerar la transformación digital que ya está en marcha en muchos entornos de fabricación. Para los equipos que trabajan de forma remota o bajo pautas de distanciamiento físico, la recopilación de datos en tiempo real y las tecnologías de análisis avanzado pueden proporcionar una imagen más detallada, precisa y actualizada de las operaciones de la planta.
Las cámaras de mano y los anteojos inteligentes pueden brindar al personal remoto una presencia virtual en el taller, lo que les permite ayudar a los equipos de primera línea con tareas de solución de problemas o incluso participar en caminatas gemba para apoyar a los supervisores y operadores de línea. Los procedimientos operativos estándar digitales (SOP) y las guías de resolución de problemas pueden ayudar a los equipos de primera línea cuando los gerentes o colegas más experimentados no están disponibles. Las tecnologías de aprendizaje en línea pueden ayudar al personal a desarrollar nuevas habilidades rápidamente, creando una fuerza laboral más flexible y más conocedora de la tecnología en todos los niveles de la organización (Anexo 4).
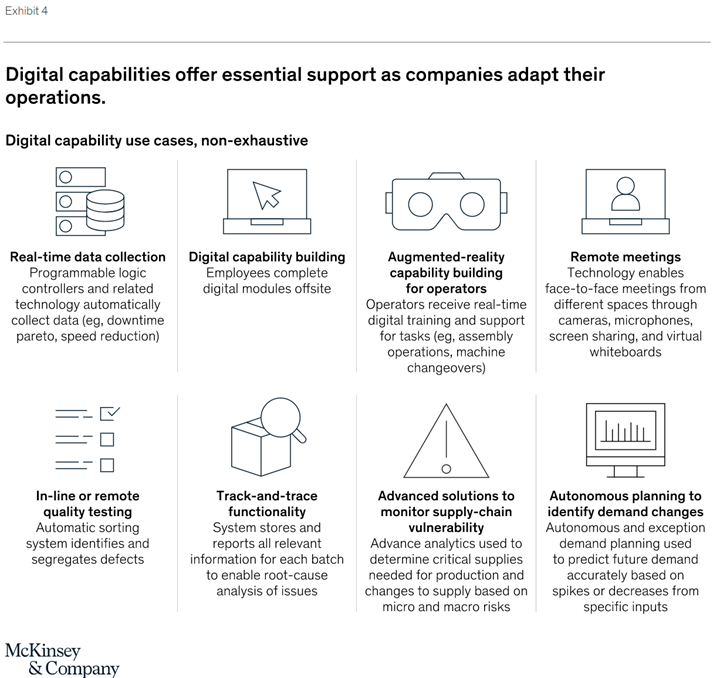
Es probable que la próxima normalidad genere un cambio en las métricas y los objetivos que las empresas utilizan para optimizar el rendimiento de fabricación. Los sistemas de gestión que generalmente enfatizan la productividad y la calidad se expandirán para incluir un mayor enfoque en la flexibilidad (por ejemplo, la cantidad de personal capacitado para realizar múltiples tareas en la línea) y la resiliencia (la cantidad de escasez de componentes debido a la cadena de suministro o problemas de calidad o las habilidades que escasean porque solo un pequeño número de empleados tiene la capacitación o experiencia necesaria). Las empresas pueden reforzar esos cambios ajustando objetivos e incentivos para empleados individuales, como enfatizando el cumplimiento de las pauts de salud y seguridad. El personal podría ser recompensado por desarrollar conjuntos de habilidades más amplios, reducir la dependencia de contratistas externos y aumentar la capacidad de recuperación general de la fuerza laboral.
El coronavirus tendrá efectos duraderos, quizás permanentes, en las organizaciones manufactureras, lo que obligará a las empresas a reestructurar sus operaciones para mantener la producción y proteger a sus trabajadores. Las próximas semanas y meses seguirán siendo extremadamente difíciles para los líderes de las plantas, pero la crisis también crea una oportunidad para reimaginar la forma en que se realiza el trabajo.
Al acelerar la adopción de nuevas tecnologías digitales y al aprovechar la flexibilidad y la creatividad de su personal de primera línea, las empresas tienen la oportunidad de salir de la crisis con operaciones de fabricación que son más seguras, más productivas y más resistentes.
Contenido relacionado
BorgWarner anuncia inversión en San Luis Potosí
La inversión de BorgWarner permite la creación de una nueva planta de fabricación de componentes electrónicos de potencia y motores eléctricos.
Leer MásIndustria automotriz en México: balance 2022 y proyecciones 2023
Conozca las estadísticas en producción, exportación y ventas de vehículos en México en 2022. Explore el impacto del nearshoring y la producción de vehículos eléctricos en la industria de autopartes.
Leer MásMéxico: perspectivas de crecimiento para la industria de autopartes
En 2023, la industria de autopartes en México prevé un crecimiento del 10.45 %, con un valor de producción de USD 115,802 millones, esto pese a desafíos como la huelga de UAW en EE. UU. El nearshoring ha jugado un papel clave.
Leer MásAcabado automatizado en CNC: barriles de alta energía
Mass Finishing Inc. ha desarrollado máquinas de acabado con barril de alta energía que automatizan el proceso de desbarbado de partes complejas, lo que ahorra tiempo y elimina la necesidad de desbarbar las partes a mano.
Leer MásLea a continuación
En Nuevo León crean ventilador para atender a pacientes con COVID-19
Investigadores de la Universidad Autónoma de Nuevo León (UANL) y la empresa Kronos Dta crearon un ventilador mecánico para tratar a pacientes con COVID-19.
Leer MásEl reto del coronavirus en la manufactura mexicana
Hay que considerar que, fuera de lo trascendentales de las actividades del sector metalmecánico, está de por medio la sostenibilidad de las industrias aeroespacial y automotriz, sustento de miles de familias mexicanas.
Leer MásAnte COVID-19 surgen iniciativas de manufactura aditiva en México
Stratasys México, Tridi MX, Prothesia y la Asociación Mexicana de Manufactura Aditiva y 3D trabajan en diversos proyectos de manufactura aditiva.
Leer Más