Compartir
Lea a continuación
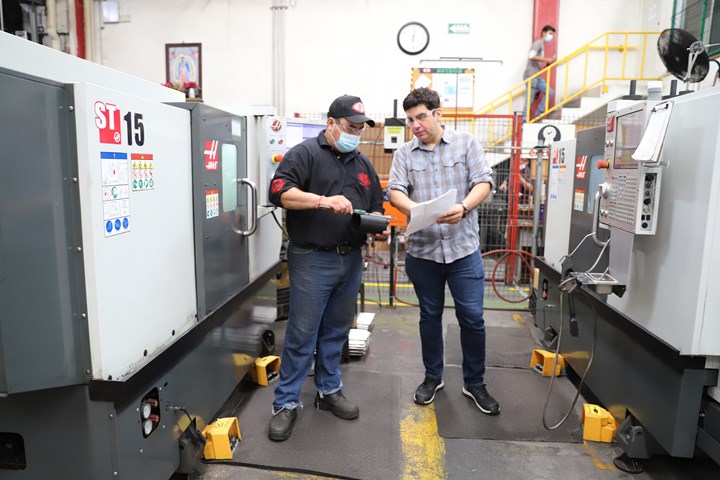
El ingeniero Gilberto Tamez, director de MITSA, cree que la clave del éxito de un taller es la capacitación. “Los mejores operadores son hechos aquí. Si traes un operador de otra parte, es difícil que comparta nuestro ritmo de trabajo porque viene con otro tipo de mentalidad. Es preferible que entren jóvenes al taller, porque aquí aprenden y les enseñamos la cultura de trabajo de la empresa. Con el paso del tiempo es la gente más valiosa que tienes”.
Maquinados Industriales Tamez (MITSA) es una empresa familiar, fundada por Isaúl Tamez Alanis en 1980. “Yo nací en ese año. En ese entonces, mi papá trabajaba en una empresa en Monterrey llamada Fábricas Monterrey, del grupo Femsa, donde fabrican latas y envases para bebidas. Él trabajaba allí en el área de moldes, como operador. Mi abuelo le prestó un dinero y pudo comprar su primera máquina para iniciar Talleres Unidos, que es nuestra empresa hermana. Talleres Unidos se dedica a la fabricación de cuchillas para el corte de papel y al mantenimiento industrial. Toda la vida crecimos viendo a mi papá trabajar en esto. Me parecía fabuloso que un pedazo de metal se transformara en diferentes piezas. Crecí y empecé a estudiar ingeniería. Con el tiempo, los clientes nos pedían piezas más complejas, pero no era fácil hacerlas con las máquinas convencionales que teníamos en el taller”, cuenta el ingeniero Gilberto Tamez, director de MITSA.
MITSA originalmente tenía otro dueño, era un taller pequeño que tenía dos máquinas CNC pequeñas. “Uno de los socios conoció a mi papá y le propuso venderle el negocio. Mi papá aceptó y le dijo que iba a poner al frente a su hijo, que tenía conocimiento. Pero la realidad era que yo tenía 21 años. El taller tenía máquinas convencionales y máquinas CNC, pero muy obsoletas. Por fortuna, aprendí de contratación con un señor que tenía mucha experiencia en CNC y me ayudó a entrar en este mundo”, dice Gilberto Tamez.
Al comienzo de sus actividades MITSA empezó a comprar máquinas CNC nuevas y usadas de diferentes marcas y distintas formas de programación.
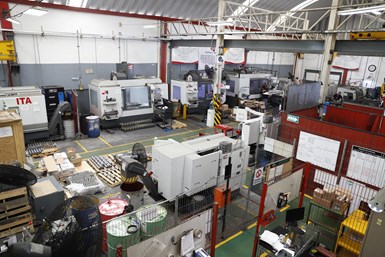
Al comienzo de sus actividades MITSA compraba máquinas CNC nuevas y usadas, de diferentes marcas y distintas formas de programación. Estandarizar las máquinas y los tipos de controles ayudó muchísimo con las refacciones, los mantenimientos y la operación de los equipos, además de que ayudó a reducir los tiempos de mantenimiento, programación y paros.
“Aquí me metí en el primer lío, pues empezamos a crecer con diferentes tipos de maquinaria y de controles. Y el problema era que no podía estandarizar. Era un dolor de cabeza: los mantenimientos, las refacciones y la programación de tantas máquinas distintas. De manera que replanteamos: si queríamos crecer no podíamos seguir ese esquema, que no estaba funcionando. Justo entonces conocimos a Hi-Tec. Platicamos con ellos y compramos la primera máquina Haas. La gente que llevaba tiempo trabajando aquí me decía que no comprara esa máquina, que comprara otra marca. Crecí con esa mentalidad, pero una vez que conoces la marca te das cuenta de que son mitos. Adquirimos la primera máquina y fue tan rentable que ese mismo año compramos tres más. Eso nos cambió la visión del negocio y empezamos a estandarizar. Me pareció fabuloso poder cambiar refacciones de una máquina a otra. Si por casualidad estoy trabajando y tengo un proyecto en una VF7, que no puedo parar, y por alguna razón algo falló, puedo quitarle a mi VF5 esa refacción para ponerla en la otra y la máquina sigue funcionando. También puedo poner distintos operadores a trabajar las máquinas, porque el control es el mismo para todas. Ese cambio nos ayudó muchísimo en cuanto a las refacciones, los mantenimientos y la operación. Y a partir de allí decidimos continuar con la marca, porque esas máquinas trabajan muy bien el tipo de piezas que hacemos. De esa manera, no tuvimos que seguir cambiando de marca, lo que ayudó a reducir los tiempos de mantenimiento, programación y paros”, explica el ingeniero Tamez.
Máquinas-herramienta nuevas
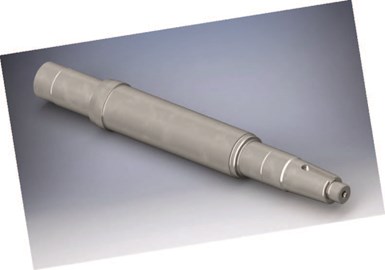
El proceso de producción de las flechas de Alstom se realiza con una barra de acero 4140 tratado, con un diámetro exterior de 4 pulgadas y longitud de 29⅜, donde se realizan operaciones en un torno Haas ST40 y un centro de mecanizado Haas VM6.
En el año 2012 MITSA adquirió la primera máquina nueva de Hi-Tec y, a partir de ahí, el taller empezó a renovar los equipos, a razón de dos o tres máquinas por año.
Una de las adquisiciones que más ha marcado la diferencia en la producción del taller es un torno Haas ST40 de grandes capacidades. El torno más grande del taller era un ST15, que usaban para producción de piezas pequeñas y medianas. Si bien MITSA tiene clientes de todo tipo, con el ST40 se han enfocado en la fabricación de flechas motrices para trenes, producidas para Alstom en Nueva York.
“Gracias a esa máquina logramos el contrato y las piezas están saliendo con la calidad requerida; trabajamos muy bien con ellos. Sin esa máquina no habríamos podido conseguir el trabajo, uno de esos contratos que llegan de pronto. Además de la máquina teníamos la experiencia y las certificaciones. Fue sorprendente, porque inmediatamente después de comprarla, abrimos una puerta a un mercado que no teníamos”, afirma Gilberto Tamez.
MITSA trabaja de dos maneras. Si un cliente necesita una maquinaria simple, ellos desarrollan la ingeniería y la fabrican. En la otra modalidad el cliente les envía los dibujos y ellos mecanizan la pieza de acuerdo con el prototipo enviado por el cliente, como en el caso de las flechas de Alstom.
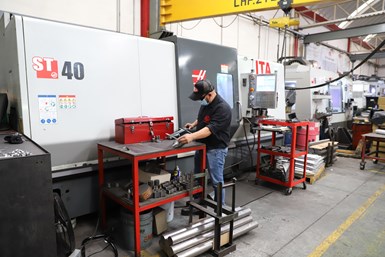
La primera operación de las flechas motrices para trenes se realiza en un torno Haas ST40, en el que se hace el torneado de la cara y el centro. Posteriormente, la flecha se coloca en el contrapunto para realizar el desbaste y acabado de los diámetros exteriores (cono y rosca). El ciclo para esta operación es de 35 minutos.
Antes, el máximo que podían trabajar eran piezas de 8 pulgadas de diámetro por 16 pulgadas de largo. Actualmente, con el torno Haas ST40 pueden trabajar piezas con dimensiones de 16 a 17 pulgadas hasta un metro de largo. La flecha de Alstom, por ejemplo, es una pieza de 8 pulgadas por un metro de largo, de las cuales este año van a producir 400, pero en 2022 tienen programado producir 3,500.
En esa misma máquina también hacen piezas para la empresa Dematic. La mayoría de los clientes que atienden requieren producción de piezas de bajo volumen y alta mezcla. Precisamente, la estandarización de los controles le permitió a MITSA brindar el servicio a los clientes que necesitan muchos tipos de piezas, en un rango amplio y diferente, pero en volúmenes bajos.
“Necesitamos hacer cada vez más rápido los setups, las programaciones, contar con que la misma persona pueda manejar varias máquinas y que tenga el conocimiento para poder jugar con el rol de los turnos. Esto nos ha ayudado bastante porque los clientes no son de alta producción y de millares de piezas. A veces nos llegan órdenes de piezas diferentes en volúmenes de veinte, treinta o quinientas partes. Y tienes que responder en tiempos muy cortos para hacer las entregas. Prácticamente, ese fue el diferenciador: estandarizar las máquinas y los controles para atacar ese mercado, el que actualmente atendemos”, explica el ingeniero Tamez.
Producción de flechas motrices
El proceso de producción de las flechas motrices que MITSA fabrica para Alstom se inicia con una barra de acero 4140 tratado, que tiene un diámetro exterior de 4 pulgadas y una longitud de 29 ⅜ pulgadas, en el que se realizan dos operaciones donde intervienen dos máquinas: un torno Haas ST40 y un centro de mecanizado Haas VM6.
En la primera operación se realiza el torneado de la cara y el centro, para después colocar la flecha en el contrapunto y así poder realizar el desbaste y acabado de los diámetros exteriores (cono, rosca). Las herramientas utilizadas para esta operación son insertos para torneado CNMG, DMNG y VNMG con diferentes radios. Posteriormente, la pieza se gira para realizar el mecanizado de los diámetros restantes (el ciclo para esta operación es de 35 minutos).
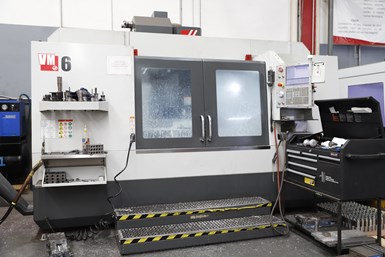
En la segunda operación de la producción de las flechas motrices para trenes utilizan un centro de mecanizado Haas VM6.
En la segunda operación utilizan un centro de mecanizado VM6 para realizar el cuñero localizado en el cono de la flecha y para el que usan un fixture con el ángulo requerido, donde colocan la flecha para poder efectuar la operación (este ciclo es de 12 minutos).
“Fabricamos las flechas en dos partes. Se hace la primera operación, que es el mecanizado de todos los diámetros con ajustes y se libera la pieza al área de calidad para verificar que todos los diámetros estén en dimensiones. Se hace todo un lote en la primera operación y luego volteamos las flechas para ejecutar la misma operación, pero del lado izquierdo. Es una operación espejo. La máquina ST40 trae una bomba de presión de soluble que sale a una presión de 1,000 psi, que pulveriza la rebaba y permite que la herramienta dure más. Así podemos trabajar a más altas velocidades para reducir los tiempos de ciclo de la pieza. Ese fue un plus que le pusimos a la máquina para poder bajar tiempos de ciclo. Originalmente lo compramos para la industria petrolera, con el fin de hacer taladros, refrigerarlos y lograr taladros muy amplios”, dice el ingeniero Tamez.
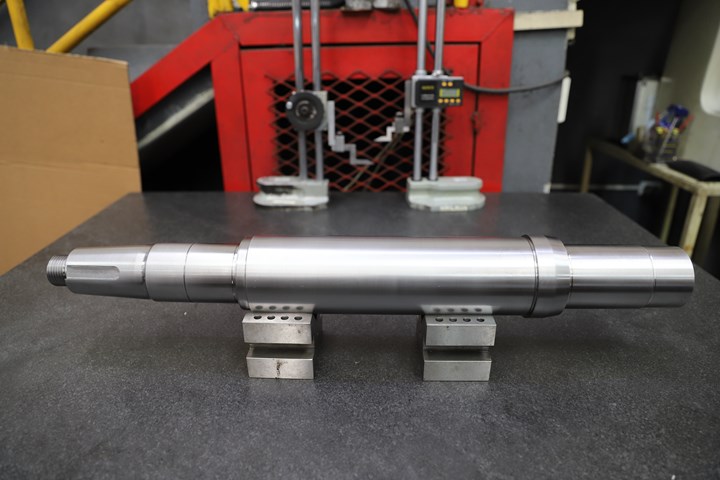
La flecha de Alstom se fabrica en dos operaciones. En la primera máquina ST40 se hace el mecanizado de todos los diámetros con ajustes y se libera la pieza al área de calidad para verificar que todos los diámetros estén en dimensiones. Luego de producir todo un lote, pasa al segundo torno ST40, donde se le hace la misma operación, pero del lado contrario. Es una operación tipo espejo.
“Cuando vas a hacer un proyecto invitas a varios proveedores, que traen las herramientas y hacen pruebas. Escogemos la que mejor funciona por costo-calidad. Hace poco, Hi-Tec nos ofreció el servicio de herramentar las máquinas, ya que ellos saben qué ciclo y a qué velocidades trabajamos. Traemos un proyecto que vamos a empezar con ellos para trabajar todas las piezas que fabricamos y nos van a ayudar a herramentar las máquinas para conseguir ciclos más exactos. En el caso de la producción de las flechas, usamos herramientas para tronzado de diámetro y roscado con diferentes ciclos, de Sandvik Coromant.
Equipos que facilitan la producción de otros componentes
El taller también cuenta con una máquina Haas ST15, que utilizaban para producir componentes de los equipos, robots y conveyors de la empresa Dematic. Ellos necesitan muchas flechas de inoxidable o de otro tipo de materiales.
“Sin embargo, muchas de las piezas de ellos llevaban una segunda operación y tardábamos mucho en la producción de lotes de quinientas flechas. Teníamos que esperar a que la máquina terminara la primera operación para voltear la pieza y seguir trabajando”, afirma Gilberto Tamez.
Eso ocasionaba que las piezas que estaban en fila se retrasaran. Entonces, identificaron todas las piezas que estaban haciendo que requerían operaciones iguales. “Vimos que todas esas piezas llevaban a una segunda operación espejo o una segunda operación más simple y decidimos comprar una máquina igual. Esa ST15 la pusimos en una pequeña celda y con un mismo operador. De esa manera redujimos los tiempos de ciclo a la mitad, porque cuando haces la primera operación ya estás trabajando al tiempo con la segunda operación y el mismo operador. Eso nos permitió incrementar muchísimo la producción, pero más que nada nuestro porcentaje de entregas al cliente. Antes manejábamos entregas del 84 %. Sin embargo, el último mes terminamos con una entrega del 93 %, por encima del 91 % que nos exige el cliente. Detectamos que era un área de oportunidad de mejora y lo pudimos conseguir. Uno quisiera que fuera al 100 %, pero a veces son materiales exóticos, como en el caso de los aceros, donde hay un poco de escasez y no los consigues tan rápido como antes; sin embargo, estamos dentro de los parámetros”, dice el ingeniero Tamez.
Otra situación que les ha ayudado a mejorar los tiempos de producción es el seguimiento de los procesos. Allí cuentan con un drive en el que entran todas las órdenes y se registra todo el proceso, desde que se recibe la orden de compra y se manda a ingeniería para que se desarrolle el plan de trabajo con los materiales requeridos. Para ello hay una persona dedicada exclusivamente a ese trabajo, que debe estar revisando, de una celda a otra, con los diferentes operadores para determinar si alguna de las series tiene algún inconveniente.
“Esta máquina ST15 se adquirió en diciembre de 2020 y con la pandemia algunos de nuestros clientes bajaron los pedidos, pero a otros se les incrementó muchísimo el trabajo. Entonces, de la noche a la mañana aumentaron los pedidos y tuvimos que responder rápido. Contacté a Hi-Tec para pedirles la máquina y como la tenían disponible en Tijuana, en dos semanas ya teníamos la máquina aquí. La experiencia con otras máquinas nos indicaba que debíamos esperar que el técnico nos instruyera para ponerla a funcionar. Pero como ya conocíamos la máquina a la perfección, llegó un jueves y el viernes ya estábamos trabajando con la celda”, cuenta Gilberto Tamez.
“Esto fue algo fabuloso, que me emociona mucho porque inmediatamente vimos cómo aumentó nuestro porcentaje de entregas y nuestra facturación se fue para arriba. Además, como el cliente ve que cumples, te mandan más trabajo y se te abre el panorama por completo”.
Esta nueva máquina les permitió hacer la operación uno y en la otra hicieron la operación dos para completar el ciclo de las series de piezas. Eso les ayudó a bajar los tiempos prácticamente a la mitad. “Había mucha fila de partes por procesar ahí y el cliente estaba muy contento porque le entregábamos en tiempo y forma. Y empezamos a producir más cantidad de piezas. Es una familia de muchísimos tipos de partes con diferentes volúmenes. La programación es muy sencilla, los setups son muy rápidos y podemos hacer cambios de parte en cuestión de una hora”, dice el ingeniero Tamez.
Antes hacían los ciclos de las piezas en 10 minutos en una sola máquina. Cuando llegó la otra máquina, distribuyeron los trabajos en los dos equipos y redujeron el tiempo de ciclo a 5 minutos. Eso les permitió producir de manera más eficiente todos esos lotes de diferentes números de parte.
En este caso, el proceso inicia con un material en bruto de acero inoxidable 420 con un diámetro de 15 mm x 970 mm en el que utilizan una celda de dos tornos Haas ST15 colocados uno frente a otro y manejados por la misma persona. En la primera operación mecanizan cara, diámetros y ranuras con los ajustes y acabados superficiales indicados. En esta operación utilizan insertos CNMG y DNMG para acero inoxidable, para desbaste y acabado. En la segunda máquina dan la longitud total de la flecha y terminan los diámetros y ranuras con ajustes y acabado superficial indicados en el otro extremo de la flecha. Esto les ayudó a tener más piezas terminadas en menos tiempo y así cumplir con los requerimientos del cliente.
“El trabajo para este tipo de piezas es muy dinámico. Por ejemplo, hoy podemos recibir un dibujo, que se analiza, es autorizado y, enseguida, recibimos una orden de compra para entregar dentro de los próximos 20 días. Por eso, para el taller es importante bajar los tiempos de los procesos”.
Las piezas fabricadas en estas máquinas son para conveyors robotizados. Las flechas donde van los rodamientos en los que se desliza la banda y para algunos robots que se deslizan por las plantas entregando cosas. Son flechas de transmisión que llevan ajuste para los baleros de diferentes diámetros y largos, además de bujes de todo tipo.
La capacitación es la clave
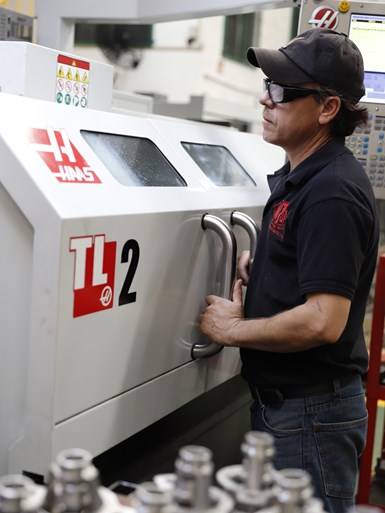
Varios de los operadores de MITSA han sido capacitados en Hi-Tec
Gilberto Tamez conoció a la gente de Hi-Tec en una exposición. “Para nosotros, ir a una feria es como ir a una juguetería. La relación que tengo con ellos en los últimos años es muy estrecha. Por ejemplo, con Alicia Espejel, gerente de ventas de esta área, tengo toda la confianza. Es como hablar con una amiga. Si tengo una necesidad o algo inesperado, enseguida le hablo a Alicia. Siento que más que proveedores somos amigos”, afirma Gilberto Tamez.
Varios de los operadores de MITSA han sido capacitados en Hi-Tec. “Los mejores operadores son hechos aquí. Si te traes un operador de otra parte, es difícil que comparta nuestro ritmo de trabajo porque viene con otro tipo de mentalidad. Es preferible que entren jóvenes al taller, porque aquí aprenden y les enseñamos la cultura de trabajo de la empresa. Con el paso del tiempo es la gente más valiosa que tienes”, explica el ingeniero Tamez.
Actualmente, MITSA tiene el proyecto de hacer una miniescuela, con la ayuda de Hi-Tec, para dar cursos con los controles de Hi-Tec. “Quiero comprar algunos de esos controles, hacer un salón pequeño y empezar a capacitar a jóvenes para que sean nuestros empleados y de alguna forma ayudarnos mutuamente”, dice Gilberto Tamez.
Actualmente están en un plan de expansión con las dos empresas, Talleres Unidos y MITSA. En febrero de 2020 adquirieron un terreno muy cerca de las actuales instalaciones de MITSA, donde planean construir una nave cuatro veces más grande.
“En ese terreno vamos a crear una nueva empresa, que inicialmente va a dar servicio tanto a MITSA como a Talleres Unidos, mientras desarrolla sus propios clientes. La mitad del terreno lo queremos usar para ensambles y proyectos, porque ahora nos hace falta espacio. Crecimos de una manera que nos quedamos sin espacios y, de repente, hay clientes que piden todo tipo de estructuras pequeñas o carritos móviles para mover en una planta. También como el caso de Whirlpool. Ellos tienen máquinas para moldes y de pronto necesitan que las modifiquemos, pero hay que traernos los equipos. Entonces, no tenemos espacio suficiente para hacerlo”.
La mitad de esa nueva nave va a estar disponible para ese tipo de proyectos, y en la otra parte van a instalar unas máquinas de gran capacidad de Hi-Tec. “Veo un área de gran oportunidad para México. Talento en el país hay mucho. También muchos herramentales que se pueden hacer aquí en el país, pero como las empresas vienen de corporativos extranjeros, deciden comprarlos en Italia o Estados Unidos. Hablando de oportunidades, siento que hay muchas para empresas como la nuestra, especialmente en herramentales. Si hubiera un desarrollo en las plantas y vieran el talento que hay en los talleres de México en general, la situación cambiaría. El área de herramentales es un nicho que nos va a beneficiar a todos: a nosotros como fabricantes y a las empresas que van a tener un proveedor local y más barato. Yo le vendo moldes Whirlpool, pero a veces siento que pudiera haber muchísimo más trabajo si hubiera un poco más de apertura”, concluye Gilberto Tamez.
Contenido relacionado
Máquinas-herramienta en IMTS 2024: impulsando la innovación en la manufactura
El sector de las máquinas-herramienta en IMTS 2024 presentó innovaciones de vanguardia diseñadas para mejorar la productividad, la precisión y la flexibilidad en los procesos de manufactura.
Leer MásPresentan cifras de importación de máquinas-herramienta de enero 2023
En enero de 2023, el valor de las importaciones de centros de mecanizado y tornos tuvo incrementos con relación a enero de 2022, de acuerdo con el Banco de México.
Leer MásAvances tecnológicos de Mazak resaltan en FITMA
En FITMA, Mazak presenta su centro de torneado Ez con asistencia robótica y el centro de mecanizado horizontal HCN-5000 que destacan por su productividad y tecnología avanzada.
Leer MásPrincipios del mecanizado asistido por vibración
VibroCut, un método desarrollado por el Instituto Fraunhofer de Máquinas-Herramienta y Tecnología de Conformado (IWU), consiste en superponer vibraciones de baja frecuencia o ultrasonido en el proceso de maquinado convencional.
Leer MásLea a continuación
"La pandemia también nos abrió los ojos": Luciano Diorio, director Grupo Hi-Tec
En entrevista con Modern Machine Shop México, Luciano Diorio, director del Grupo Hi-Tec, habla sobre su trayectoria en la industria y el lanzamiento de la Comunidad CNC.
Leer MásHi-Tec lanza la “Comunidad CNC” en México
Luego de varios meses desarrollando el proyecto, Grupo Hi-Tec lanza la “Comunidad CNC”, un grupo virtual conformado por operadores, técnicos CNC, dueños de talleres e ingenieros de empresas que tienen la necesidad de resolver problemas cotidianos en sus talleres.
Leer MásSistemas innovadores de sujeción para electroerosión y mecanizado de tres ejes
Con el propósito de aumentar el índice de ocupación de máquinas en el taller, este fabricante de moldes adaptó un dispositivo de sujeción en sus máquinas de tres ejes y su electroerosionadora de penetración para aumentar la flexibilidad de sus equipos y ser más competitivo.
Leer Más