Con mecanizado horizontal y de 5 ejes, MAPSA toma vuelo
MAPSA, de Monterrey, le ha sacado provecho al mecanizado horizontal y de 5 ejes para la producción de componentes petroleros. Es tanto lo que han aprendido de estos dos procesos, que ya tienen en la mira la producción de partes para la industria aeroespacial y automotriz.
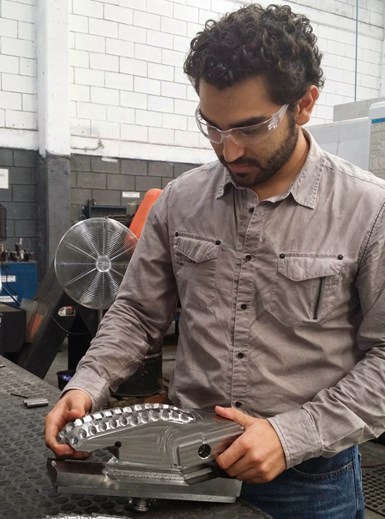
Según Rubén Garza, Gerente General de Maquilas de Alta Precisión, su taller no tenía ninguna experiencia con máquinas horizontales, “pero el equipo técnico de Mazak vino a nuestras instalaciones a capacitarnos para aprender cómo se programa y a utilizar las adecuaciones de la máquina horizontal HCN 6800, que no vienen estándar de fábrica”.
MAPSA inició operaciones en el año 2005 como Maquilas de Alta Precisión en Monterrey, Nuevo León. Hacía algunos años ya existían como una empresa que se llamaba Maquinados Gamar.
Pero fue a partir de 2005 que todo cambió para ellos cuando adquirieron la primera máquina de control numérico. Este taller inició sus trabajos haciendo componentes para bombas hidráulicas.
De hecho, las dos máquinas CNC que compraron fueron para producir componentes que exportaban a Estados Unidos.
“Con este cliente fuimos creciendo hasta cierto punto, pero llegó un momento en que decaímos. Seguíamos buscando más trabajo y fue cuando encontramos a Nidec Motors, a quienes les fabricamos componentes para motores eléctricos”, comenta Rubén Garza, Gerente General de Maquilas de Alta Precisión.
Con ellos trabajaron cerca de 5 años y continuaron comprando máquinas, aumentando así su capacidad. “
Fue cuando empezamos a ver áreas de oportunidad. Había piezas que no teníamos la capacidad de hacer, en dimensiones más que nada. Llego un punto en que encontramos más clientes y no dábamos abasto. Fue así que decidimos adquirir más máquinas, con mayor capacidad, para entrar a otro nicho de mercado”.
Hace dos años empezaron a trabajar con la industria petrolera. Contaban con una maquina Mazak de 5 ejes (un centro de mecanizado vertical VCN 510-II), que adquirieron en el año 2010. Esta es una máquina que por sus características de columna fija extendida y autosoportada en la base ampliada de la máquina a la carrera longitudinal de 1050 mm (41.3") le confieren versatilidad para tamaños y pesos de piezas variados, aunado a su husillo de 12,00 rpm y 25 HP, que le dan versatilidad para ejecutar cortes en piezas de forma compleja y materiales difíciles de mecanizar.
Precisamente, esa tecnología fue la que les permitió ingresar al sector petrolero y, con los clientes de la industria petrolera, nuevamente empezó el crecimiento de la producción en el taller.
Sin embargo, en la actualidad han tenido limitaciones de capacidad porque han llegado muchos clientes que les piden el mecanizado de piezas grandes. Por ello, decidieron adquirir una nueva máquina Mazak de mecanizado horizontal (un centro de mecanizado horizontal 6800 HM) de características diferentes a las demás que tenían, con ciertos aditamentos y extras. En estos momentos llevan 4 meses trabajando con la máquina.
“Anteriormente, trabajamos diferentes materiales, productos y diferente complejidad. En octubre de 2014 recibimos nuevas órdenes de la industria petrolera y ahí empezamos con las pruebas. En realidad esas piezas las habríamos podido hacer en otra máquina pero no con la misma rapidez y productividad que con esta nueva máquina. Actualmente, hemos podido mecanizar piezas que no podíamos mecanizar antes”, refiere Rubén Garza.
En el caso de los componentes hidráulicos que MAPSA produce para diferentes clientes, el centro de mecanizado horizontal también les ha servido. Antes hacían una pieza en 4 o 5 operaciones, y tardaban hasta 3 horas en producirla. Ahora la hacen en 29 minutos.
“Se trata de bombas hidráulicas para impulsar el agua en plantas y edificios. Antes las hacíamos con tres máquinas: dos tornos y un centro de mecanizado, con dos operaciones en los tornos y tres en los centros de mecanizado. Ahora realizamos el trabajo con un solo setup en la maquina horizontal. Con el doble pallet tenemos la habilidad de estar produciendo sin tener tiempos muertos y se hace en dos operaciones, sin tener que estar montando y desmontando durante el tiempo que la maquina esté parada y eso representa bastante productividad en comparación a como lo hacíamos antes”, comenta el ingeniero Garza.
El montaje de las piezas en el centro de maquinado
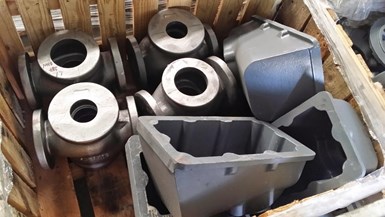
Este taller inició sus trabajos haciendo componentes para bombas hidráulicas, como los que se aprecian en la foto. Las dos primeras máquinas CNC que compraron fueron dedicadas a producir componentes que exportaban a Estados Unidos.
Por el doble husillo de la maquina horizontal y la dimensión de la pieza requerían una sujeción especial. “Al mismo tiempo que nos llegó la maquina llegó un proveedor de herramientas de sujeción. Nos hizo demostraciones y pruebas, pero en ese momento todavía dudábamos. Luego decidimos hacer una inversión de dos módulos de sujeción que lleva dos pernos o pines. Entonces, eso nos dio la habilidad de bajar un aditamento de sujeción y subir otro en cuestión de 5 minutos. El modulo es neumático y se conecta por aire, sujetando o soltando (VERO-S de SCHUNK). Antes, usábamos los típicos 6 tornillos y teníamos que apretar, alinear, sacar centros y empezar a correr el trabajo”, comenta Garza.
Ese trabajo les implicaba 3 horas de setup. Con estos nuevos dispositivos pudieron bajar el tiempo del alistamiento entre media hora y 40 minutos (entre poner herramental, y quitar y subir dispositivos (antes tardaban medio turno en completar un solo setup). Esto les ayudó bastante porque tienen mucha carga en esa máquina.
Para generar los programas de mecanizado utilizan Mastercam y, para ello, contrataron una persona que conoce SolidWorks, donde se hace el diseño del aditamento. El aditamento consta de una placa y su configuración para poder subir la pieza a la máquina.
“Trabajamos con hierro vaciado y todas las piezas varían y tienen diferentes complexiones, es decir, cada número de parte tiene su propio dispositivo de sujeción. Por eso, tenemos que hacer esos dispositivos antes de empezar a trabajar la pieza”, explica el ingeniero Garza.
Para el caso de las bombas hidráulicas, el cliente les lleva el diseño, el dibujo y hasta el material. Por su parte, ellos tienen que diseñar el dispositivo para poder sostener la pieza, escoger las herramientas y desarrollar el programa.
“Todo lo que es el diseño de la pieza en sí es propiedad del cliente. Lo que son dispositivos de sujeción, herramientas y programas es propiedad de MAPSA”, anota Garza. En el herramental los ha apoyado Tecnitools, el distribuidor de Kennametal, quien les provee las herramientas y les da algunas asesorías en ciertas aplicaciones donde necesitan saber qué tipo de herramienta usar, con qué avances, y a qué velocidades.
El proceso de producción en MAPSA
Tenemos un programa de producción donde sabemos qué va a hacer la máquina y el número de partes que producirá. Toda máquina tiene una hoja de ruta que viaja con las piezas y contiene lo que se le va a hacer a la pieza, el dibujo, la liberación de la primera pieza, y la inspección del proceso.
Hay una persona encargada del setup, que sabe cuándo va entrar una pieza a una máquina, de manera que va preparando las herramientas y todo lo necesario para el trabajo de la pieza. Así, cuando la máquina termina el trabajo ya todo está preparado para empezar la segunda corrida. En el caso del centro de mecanizado horizontal nuevo, quita el aditamento y sube el siguiente.
“Es la ventaja de la máquina porque solo es cambiarlo y poner la herramienta que haga falta, sacar las longitudes de las herramientas y empezar con la operación”, dice Garza. Normalmente, las máquinas ya tienen cargado el programa, si es una pieza que han corrido anteriormente. Es solo cuestión de realizar un chequeo del programa para hacer que coincidan las herramientas y empezar a correr las piezas.
Para los componentes petroleros que produce MAPSA, hacen un premecanizado o desbaste en el centro de mecanizado horizontal y luego el componente pasa a la máquina de 5 ejes, para hacer mecanizados, taladros, pernos y rimados. Se hace prácticamente toda la figura de la parte y ahí mismo se corta la pieza.
Mecanizado horizontal
El componente para el sector petrolero que actualmente producen para Weatherford es un Under Reamer, herramienta necesaria para la perforación de pozos petroleros. En el centro de mecanizado Mazak HCN 6800 se hace el desbaste de la pieza por las cuatro caras, además de unas referencias, donde se montan los pines de sujeción.
“A diferencia de la otra máquina teníamos que hacer los desbastes por partes, es decir, primero un lado y teníamos que voltear la pieza. Hacer el otro lado y voltearla otra vez. En cambio, en esta máquina, como tenemos la ventaja que la mesa puede girar, hacemos en una sola montada todo el mecanizado”, explica Garza. Eso significa que antes hacían cuatro operaciones y ahora solo deben hacer una.
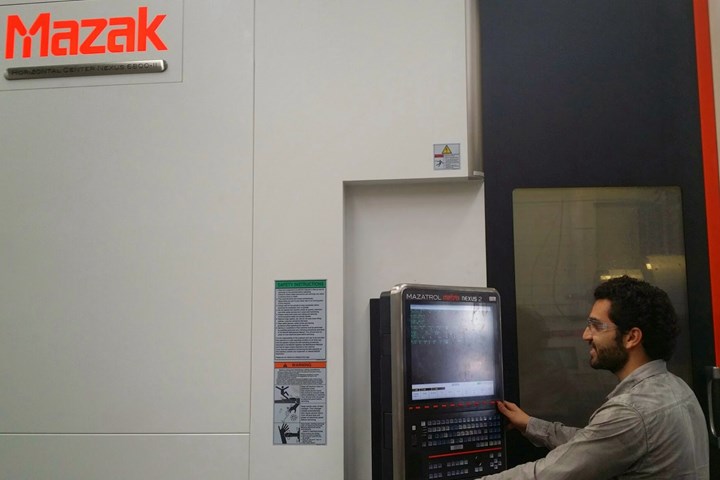
MAPSA decidió adquirir una nueva máquina Mazak de mecanizado horizontal (un centro de mecanizado horizontal 6800 HM) de características diferentes a las demás que tenían, con ciertos aditamentos y extras.
Luego de que se ha hecho el mecanizado de las cuatro caras en el centro de mecanizado horizontal, como se siguen conservando los pernos de sujeción, los mismos pernos los utilizan para la máquina de 5 ejes, donde realizan los procesos de acabado, el terminado de la figura, los taladros que van en diferentes posiciones, y todos los trabajos necesarios de la máquina de 5 ejes, donde tienen la posibilidad de poner la posición en que quieran mecanizar. Allí termina prácticamente todo el proceso, excepto un proceso sencillo, que es un acabado en la parte inferior de la pieza, y que la realizan en un centro de mecanizado vertical 510C Mazak de 3 ejes.
Todo el proceso de este componente para la industria petrolera parte de un sólido redondo que se trabaja en la máquina horizontal HCN 6800 de Mazak, donde se hace el desbaste para que la pieza tome la forma. Luego de que la pieza queda mecanizada por los 4 lados pasa al centro de 5 ejes. Utilizan los mismos módulos de sujeción, pero la ventaja en la máquina de 5 ejes es que la mesa gira y se hace la figura completa y se realizan los agujeros, taladros y la forma finalizada (ver fotos).
Estas piezas son usadas para el rimado de los pozos petroleros para abrir pozos de 12 pulgadas de diámetro, aunque también han hecho herramentales para abrir pozos de 38 pulgadas de diámetro. “La pieza más grande que hemos hecho es de un sólido de 450 kilos y al final, cuando se ha terminado el proceso pesa 93 kilos, lo que muestra la cantidad de material que se remueve en la elaboración de dichas piezas”, cuenta Garza.
Cuando llega el requerimiento del cliente, les entrega el sólido en 3D. Los ingenieros del taller lo ponen en el software Mastercam y allí determinan que tipo de sólido es y qué dimensiones van a ocupar. Un sólido puede requerir unas dimensiones de 8 pulgadas de diámetro por 12.5 pulgadas de largo. Con base en eso, el Departamento de Compras se encarga de hacer el pedido del material, que se trae de Estados Unidos por ser un material especial (acero 4145 modificado).
“En México hemos batallado mucho para conseguir aceros. La mayoría del material se trae de Houston, que normalmente tiene un tiempo de entrega de dos semanas. Cuando se requiere muy urgente se hace el pedido con costo extra que debemos pagar por el flete”.
Cuando el material llega a Monterrey, lo primero que hacen es empezar a diseñar los programas en el Mastercam para la primera, segunda, tercera y cuarta operación.
El dispositivo de sujeción que se utiliza en el taller para la primera operación, por lo general, se ocupa para las demás operaciones.
“Siempre los productos que hacemos son nuevos y nunca hemos repetido un número de parte. Eso se debe a las complexiones y la ingeniería de los mismos pozos petroleros, que siempre son diferentes”, explica Garza.
Por eso, siempre deben desarrollar la pieza y el programa, además del setup de las máquinas. De esa manera, decidieron estandarizar y hacer un solo aditamento para todas las piezas.
La pieza la sujetan de manera que el redondo quede sobre la mesa ya grapado. Se hace la primera operación, que es una cara, y los primeros registros para poner los chupones de sujeción, que son los pines para los módulos de SCHUNK, que adquirieron especialmente para ese proceso (VERO-S).
“Estos módulos nos han ayudado mucho y pueden sujetar hasta 8 toneladas. Adquirimos los módulos para hacer las primeras piezas en la máquina nueva. Empezamos a hacer las pruebas y se hizo la primera operación donde se colocan los pines o pernos. Luego, sobre esos pernos entran al módulo, se quita la L, se sujeta, y ya está lista la pieza para mecanizarla. La segunda operación es el desbaste de todas las caras, por todos lados, y se hace la preforma, que tiene las medidas más amplias de la forma que debe tener la pieza. Posteriormente, la pieza es enviada a la máquina de 5 ejes, donde la pieza es sujetada con los mismos módulos y se realizan los acabados y el tipo de forma de la pieza, los taladros, y el rimado”, explica Garza.
Para la preforma, utilizan las piñas y herramientas de desbaste como face mills, end mills, y brocas de inserto de Kennametal. También usan otras herramientas de Tungaloy para conseguir acabados más finos (end mill de insertos). La ventaja con estas herramientas es que para los radios de 15 milésimas pueden conseguir los radios o las esquinas marcados tal como los pide el cliente, ya que es exigente en que lleven esos radios.
MAPSA también hace fundición de hierro gris en otra planta que les pertenece, llamada Fundición Qualy. Todo lo que funden en esa planta lo mecanizan en el taller.
Industrias automotriz y aeroespacial en la mira
“Estamos haciendo planes con un consultor para certificarnos en TS y AS para poder trabajar con las empresas automotrices y aeroespaciales. Ya estamos con las ISO, pero nos faltan las demás. Hemos visto que hay mucho nicho de mercado que no hemos podido abarcar por no estar certificados”. Y en el rostro de Rubén Garza se refleja el deseo de ser un proveedor importante de la industria automotriz y aeroespacial. De hecho, ya están en contacto con una empresa automotriz y pronto esperan trabajar con ellos.
“Una de las ventajas competitivas que hemos tenido en MAPSA han sido las máquinas Mazak y los productos que hacemos con ellas, porque la verdad no cualquier máquina da la precisión que ofrecen estas máquinas. Cuando llega un cliente nuevo que viene de Estados Unidos, le impacta ver que somos una empresa pequeña; pero al ver que tenemos máquinas de este tipo les da confianza, pues ven que estamos comprometidos a mejorar y que queremos crecer. La confianza no es solo porque tengamos ese tipo de máquinas, sino porque también ven que las sabemos utilizar para obtener buenas piezas terminadas”, explica con orgullo el ingeniero Garza.
En la actualidad el taller cuenta con 10 máquinas CNC, de las cuales ocho son Mazak: cinco tornos (un QTM 200, dos QTM 250, un QTM 300 y un QTM 350) que van desde mandriles de 8 pulgadas, el más pequeño, hasta 15 pulgadas, el más grande. Además de un centro de mecanizado vertical 510 C Mazak de 3 ejes, el centro de mecanizado VCN 510-II de 5 ejes y la máquina horizontal 6800 HM, su última adquisición.
“Ahora que empezamos a trabajar con la industria automotriz estamos pensando hacer una celda de trabajo con los tornos para sacar lotes de producción con un solo operador, pues ahora estamos utilizando varios operadores. La pieza que vamos a producir es un engrane para las retroexcavadoras de oruga”.
Esas máquinas oruga para los que MAPSA producirá los engranes cuentan de 70 a 80 piezas por cada unidad, lo que significa que van a tener mucho trabajo por hacer. “Se trata de piezas de acero forjado. La empresa nos trae el material y nosotros mecanizamos la pieza. En este momento estamos haciendo las piezas de manera separada, pero la idea es poner dos máquinas juntas para hacer una celda de trabajo. Si se hace la celda de trabajo vamos a ahorrar 25% en tiempo y nos evitaremos el desplazamiento de las piezas de un lugar a otro dentro de la planta”, afirma Garza.
“Para nosotros el apoyo de los proveedores ha sido bueno. Lo único es que no ofrecen crédito. Sin embargo, a nosotros sí nos toca darles crédito a los clientes. La gente de Kennametal nos ha apoyado bastante”.
En un inicio la parte más complicada fue la inversión y con este proveedor de herramientas han hecho una especie de joint venture. “Ya son parte de nosotros y ellos saben que les somos leales. Nos han apoyado sobre todo en tiempos de entrega, ya que a veces necesitamos una herramienta de un día para otro. En cuanto a procesos, Kennametal cuenta con técnicos en aplicaciones y cuando tenemos una duda o no obtenemos el rendimiento que queremos con una herramienta, ellos vienen, nos hacen el estudio y nos dicen que debemos implementar para mejorar el rendimiento, o nos ofrecen otra alternativa de herramienta, la cual probamos antes de adquirirla”, cuenta Garza.
Con Mazak también han tenido un buen soporte. “No teníamos ninguna experiencia con la máquina horizontal, pero el equipo técnico de Mazak vino a nuestras instalaciones a capacitarnos para aprender cómo se programa y a utilizar las adecuaciones de la máquina que no vienen estándar de fábrica”.
Entre las adecuaciones con las que cuenta la máquina horizontal está un palpador que ayuda a sacar centros en automático con la misma máquina. Normalmente, se hace con un reloj y se tiene que estar revisando manualmente el centro de la pieza. En este caso no. La máquina palpa sola en automático y sola sabe dónde quedó la pieza. Otro aditamento es el Super Flow, un sistema de soluble interno a alta presión que ayuda cuando se realizan perforaciones muy profundas en la pieza de trabajo, evitando el atasco de rebaba, permitiendo su evacuación y manteniendo la temperatura adecuada de los insertos, de manera que no se queme la broca cuando está perforando.
También está el eje indexable, que normalmente tiene cuatro posiciones. “En este caso cuenta con 360.000 posiciones, se puede voltear a .01 grados por giro. Es decir, que tiene la posibilidad de hacer taladros a 45 grados, cuando normalmente no tiene esa opción porque gira a 90 grados. La ventaja con esta máquina es que se le pueden poner varios aditamentos, de ahí su precio, y cada cual puede ponerle los extras dependiendo de sus necesidades de producción. Nosotros por manejar hierro vaciado, un material que viene muy desproporcionado, adquirimos el palpador automático. Para las aplicaciones de taladrado profundo, adquirimos el módulo de sujeción. Y como muchos de nuestros clientes son de la industria petrolera, producimos piezas muy complejas. Si esta máquina la hubiéramos comprado estándar, como viene normalmente, no hubiéramos podido hacer los taladros en las posiciones que nos lo permite hacer la máquina. Por eso, Mazak ha venido con los técnicos y nos ha ayudado bastante enseñándonos y capacitando nuestra gente para que sepan operar y aprovechar la máquina”, concluye Garza.
Contenido relacionado
Industria 4.0 en el mecanizado de implantes médicos
Conozca cómo LINK, fabricante de implantes médicos, utiliza soluciones de mecanizado y automatización de DMG MORI para una producción desatendida, eficiente y de calidad.
Leer MásTransformando desafíos del mecanizado aeroespacial en oportunidades
Este fabricante aeroespacial duplicó un subconjunto de trabajo y su habilidad para convertir la resolución de problemas en el taller en nuevos productos comercializables.
Leer MásInversión en maquinaria y equipo en México: análisis 2023
Encuentre aquí un análisis detallado sobre las expectativas y tendencias de inversión en activos fijos y maquinaria en México durante 2023.
Leer Más10 consejos para el fresado de titanio
Unas consideraciones simples de proceso pueden incrementar su productividad en el fresado de aleaciones de titanio.
Leer MásLea a continuación
Nuevas tendencias en instrumentos de medición e inspección
La precisión en la manufactura no es opcional, es una necesidad. Desde la integración de sistemas de medición en tiempo real hasta innovaciones en tecnologías sin contacto, la medición precisa resulta esencial para cumplir con las exigencias de tolerancias estrictas y optimizar los procesos de control de calidad. Exploramos los recientes avances en metrología y su impacto en industrias como la automotriz y la aeroespacial, donde la precisión es clave.
Leer Más¿Por qué usar torno-fresado?
Los fabricantes de máquinas-herramienta se dieron cuenta de que las piezas torneadas a menudo requerían también, al menos, algún trabajo de fresado o taladrado. Por ello aumentaron las capacidades de los tornos mediante husillos adicionales para el trabajo con herramientas giratorias. De esa manera surgieron las máquinas de torno-fresado.
Leer MásPor qué los talleres en México usan tornos tipo suizo
En México, el uso de tornos tipo suizo ha venido en crecimiento. Si bien empezó con aplicaciones dedicadas a la industria de la joyería y médica, ahora se utilizan para diversas aplicaciones en las industrias automotriz, electrónica, aeroespacial y de petróleo y gas.
Leer Más