Compartir
Lea a continuación
Agregar más turnos de trabajo para responder a un nuevo pedido que requiere una operación 24/7, limitar las tareas repetitivas de su personal para aprovechar sus habilidades en otras áreas y evitar las deserciones e, inclusive, aumentar el distanciamiento social entre sus colaboradores para cumplir con las medidas sanitarias que rigen por estos días, son requerimientos que pueden resultar familiares para usted y su taller de mecanizado.
La solución a los anteriores desafíos está hoy más que nunca en la automatización, y en la posibilidad que su adecuada implementación le brinda para reenfocar los recursos humanos y técnicos de su taller. En este largo camino de modernización tecnológica que ha recorrido el sector metalmecánico, la imagen de los robots industriales ha estado rondando la mente de fabricantes visionarios desde hace más de medio siglo y, por varios años, su idea estuvo asociada con complejas celdas de producción en las que, encerrados en intrincados resguardos de seguridad, desarrollaban tareas de carga y descarga de piezas que requerían de un gran espacio de operación, de una programación compleja y de un despliegue similar al que se muestra en las películas futuristas.
El arribo de los robots colaborativos al escenario industrial abrió una nueva puerta para que estos nuevos compañeros de trabajo salieran del confinamiento al que estaban asociados sus familiares y empezaran a trabajar mano a mano con los operarios del taller, extendiendo su aplicación del cargue y descargue de piezas a tareas mucho más complejas y costosas en cuanto a mano de obra —como inspección y marcación—, y haciendo que sus beneficios sobrepasen los obstáculos que hasta el momento se habían asociado para su implementación.
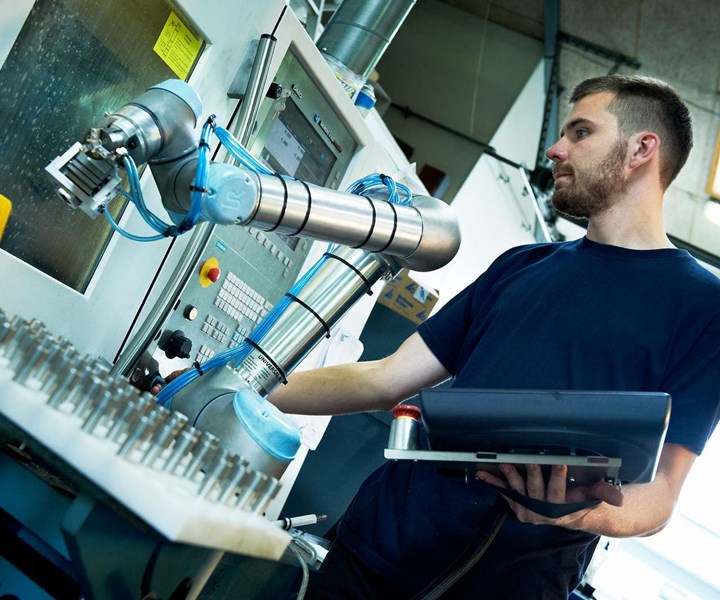
Implementación de cobots en la empresa Nymann Teknik, Dinamarca.
Además de su rápido despliegue, programación intuitiva y optimización comprobada de las tareas rutinarias de un taller de mecanizado, estos robots colaborativos le permiten ofrecer espacios seguros de trabajo para sus colaboradores en los que, al tiempo de liberarlos de las tareas sucias, peligrosas y aburridas y reducir las lesiones por esfuerzo repetitivo y accidentes, puede garantizar el sano distanciamiento y operar en varios turnos a lo largo del día.
Uriel Fraire, Channel Development Manager de Universal Robots, lo sintetiza en esta frase:
“La única forma de hace frente a las situaciones que enfrentamos hoy en día, es siendo mucho más productivos, competitivos e inteligentes y para lograrlo debemos movernos al futuro con robótica colaborativa”.
Esta compañía de origen danés logró romper con el paradigma de que los robots son poco confiables para trabajar junto con los humanos al garantizar todas las condiciones para que estos operen mano a mano con los operarios gracias a una característica de seguridad incorporada que les hace detenerse automáticamente cuando encuentran obstáculos en su ruta. Este fue un cambio radical ya que uno de los principales impedimentos para usar robots era la seguridad necesaria alrededor de la máquina.
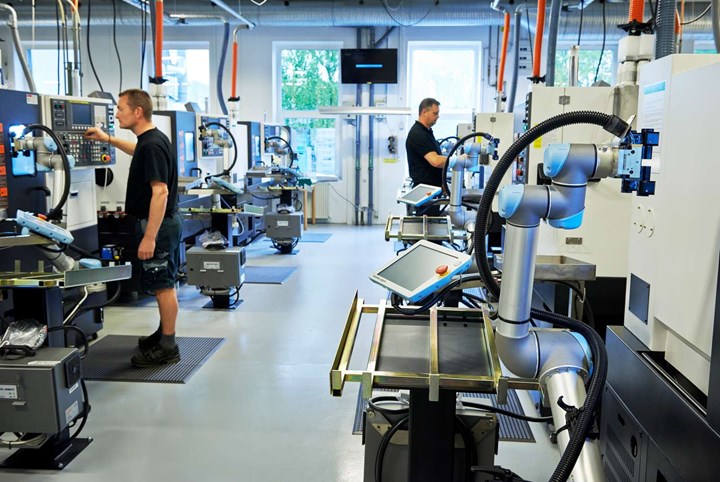
Taller Trelleborg Sealing Solutions, Dinamarca.
En el caso de las máquinas CNC, la liberación del personal que tradicionalmente las operaban también ha desempeñado un papel importante en el aumento de la calidad de las piezas fabricadas. Diversos talleres alrededor del mundo que han desplegado cobots de Universal Robots en sus operaciones han comprobado que cuando los empleados no están preocupados por mantener una máquina en funcionamiento, tienen más tiempo para inspeccionar visualmente los productos mecanizados, aportar nuevas ideas y analizar nuevas formas para mejorar la producción.
Fraire sostiene que, si bien hay tareas, como el control de la vida útil de las herramientas, que siguen siendo responsabilidad del operario, en este nuevo ambiente de producción automatizado surgen nuevas necesidades como el aprender a programar el robot y analizar en qué otras áreas del taller puede ser desplegado y, en ellas, se puede reorientar el tiempo del trabajador e incrementar sus habilidades de cara a futuras responsabilidades.
Lo que un robot colaborativo puede hacer por la eficiencia de su taller
Aunque en México se conozca poco sobre la implementación y alcances de los robots colaborativos en las máquinas CNC, hay casos documentados de talleres de todos los tamaños y giros alrededor del mundo que, con KPIs en mano, han dado cuenta de los numerosos aportes que estos cobots han hecho tanto en operaciones presenciales como en turnos desatendidos, y desde aplicaciones rutinarias de carga y descarga, hasta las más complejas asignaciones de calidad e inspección.
La clave para que la implementación de este tipo de robots sea exitosa está en la propia visión del taller, pues entre más flexible sea su operación y más alta la capacidad de reacción del equipo directivo frente a posibles cambios o nuevas oportunidades de mejora, mayor será el nivel de aprovechamiento de los cobots y, por consiguiente, el retorno de la inversión para el negocio.
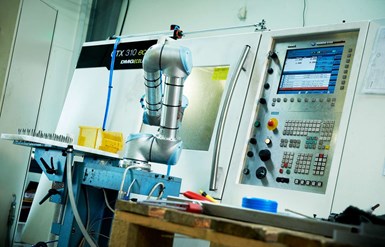
Taller Nymann Teknik, Dinamarca.
Fraire explica que, en el caso de los robots colaborativos de Universal Robots, sus funcionalidades y su facilidad de acoplamiento con los controles numéricos de las máquinas más utilizadas en el mercado, permiten una programación exacta de variables como la velocidad o fuerza de acción, haciendo que estas se puedan modificar automática y rápidamente ante la presencia de un trabajador o ante cambios en el flujo de producción.
“Las diversas posibilidades de agarre, bien sea en una mesa, pared o piso, hacen que su implementación sea posible en cualquier tipo de máquina. Lo importante es determinar el espacio disponible y, si el espacio del taller es pequeño o limitado, buscar cobots pequeños y flexibles”, agrega.
Por ejemplo, la empresa alemana Thiele implementó un brazo robótico ligero de Universal Robots para las tareas de fresado que le permitió implementar turnos desatendidos. Este nuevo colaborador nocturno abre las puertas de la máquina CNC, suministra la materia prima, ajusta la sujeción, y descarta la viruta de la fase de fresado.
Por su parte, la compañía Endutec eligió utilizar su recién adquirido robot colaborativo UR10e para automatizar el cambio de herramientas de la máquina CNC. Para lograrlo, la empresa desarrolló una estación personalizada en la que el cobot toma las herramientas de trabajo de un estante y las regresa después del mecanizado.
En el caso del fabricante de partes en aluminio, metal y plástico Jenny | Waltle, los cobots fueron la solución ideal ante la escasez de mano de obra calificada. La empresa cuenta con dos robots UR5 que atienden una fresadora utilizando un recipiente de recolección y manejan hasta 2,400 partes de aluminio al día en dos turnos. En este caso, adicional a sus tareas de descarga, uno de los cobots está conectado a un sistema de cámaras 3D para visualizar las estructuras superficiales y la colocación exacta de las piezas de trabajo.
Según Universal Robots, al utilizar los brazos robóticos, el proveedor incrementó su producción en un 11% en doce meses dentro de esta área de aplicación.
Además de los beneficios mencionados, estos son otros frentes en los que el uso de robots colaborativos ha reportado beneficios en términos de eficiencia:
1) No implican costos adicionales: Fraire sostiene que mientras que los robots industriales tradicionales demandan la inversión en el robot más diversos elementos adicionales de programación, instalación y resguardos de seguridad, en el caso de los robots colaborativos, estos solo requieren del cobot en sí más el elemento de sujeción o fin de brazo. El software está cubierto por Universal Robots que ofrece diversas opciones gratuitas y en línea para acompañar todo el proceso, desde la toma de decisión, hasta la implementación y el mantenimiento preventivo.
“El periodo medio de amortización de los robots de UR, de tan solo 195 días, es el más corto de la industria robótica”, explica Fraire.
Así mismo, su programación intuitiva, a través de una pantalla táctil, elimina la necesidad y el costo de contratar un integrador externo. Por el lado del consumo energético y de materias primas en su taller, diversos usuarios alrededor del mundo
2) Instalación y operación sencilla: los robots colaborativos son una solución fácil de manejar y portátil. Su diseño compacto ahorra espacio y pueden ser rápidamente reprogramados para ser utilizados con diferentes máquinas. Fraire explica que los robots pueden personalizarse conforme a los requisitos de fabricación (con cambio de grippers, de soporte del robot e, inclusive, con la posibilidad de transportarlos en plataformas móviles) y demandan cambios mínimos en el área de trabajo.
“Cuando una tecnología es fácil de instalar y de programar, se vuelve flexible”, sostiene.
En cuanto a su instalación, su operación simple e intuitiva hace que en promedio tome medio día el instalar y configurar un brazo robótico para una nueva tarea. “El cobot se asegura a la superficie de trabajo, luego se conecta el plug del robot al controlador, se ajusta el gripper a la mano del robot, se conecta el gripper al controlador del robot, se programan los puntos o trayectoria, y el robot está listo para trabajar”.
3) Optimización en la producción: un cobot le permite aumentar la calidad, uniformidad y velocidad. Para lograrlo, lo primero es identificar qué proceso es ideal para automatizar y, en estos casos, según Universal Robots, lo ideal es comenzar por la tarea manual que genere mayores costos en su taller, y que usted crea que no requiere de constante intervención humana. Así mismo, es clave escoger aplicaciones seguras y flexibles, en las que preferiblemente el cobot pueda ser redesplegado para optimizar más de un proceso y que a futuro permitan la escalabilidad a nuevas aplicaciones en la medida en la que aumenta su experiencia y confianza con el desempeño de este nuevo aliado.
“Si el tiempo de ciclo da, el cobot puede abrir y cerrar la puerta de la máquina, entregar piezas paletizadas y, con la disposición adecuada, atender varios CNCs al mismo tiempo”, añade Fraire.
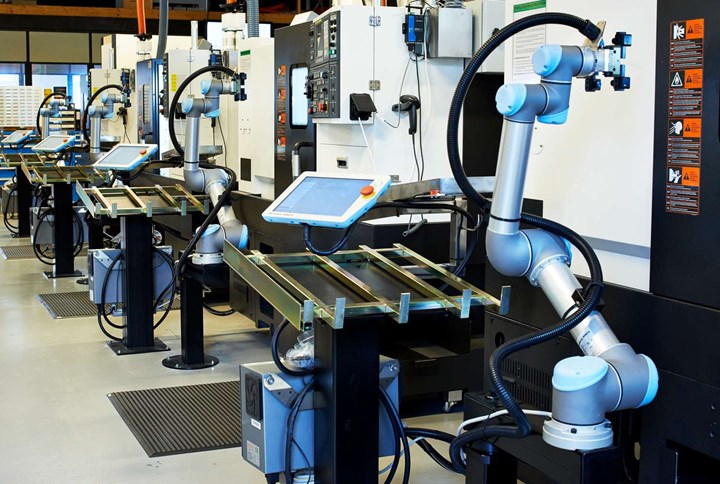
Taller Trelleborg Sealing Solutions, en Dinamarca.
Cabe señalar que los cobots tienen altos niveles de repetibilidad, con una precisión de hasta ±0.03 mm, incluso en una operación 24/7. Esto asegura tiempos de ciclo menores y reduce el desperdicio de materia prima. Además de las tareas de producción, los brazos robóticos están equipados con un sistema de cámaras pueden realizar tareas de control de calidad tales como medición 3D y pruebas.