La Industria 4.0 es una tendencia que ha permeado a lo largo y ancho del sector metalmecánico. Es el tema central de la mayoría de las ferias especializadas en el mundo, el lugar recurrente de conversación entre expertos y futurólogos, y el terreno hacia el que la mayoría de los proveedores de la industria están volcando sus innovaciones; sin embargo, aterrizado al día a día de quienes le dan vida a este sector —los talleres y quienes los conforman—parece ser todavía una realidad lejana, costosa, y destinada a seguir siendo un tema de moda, pero de poca puesta en acción.
Un informe sobre Transformación Digital del Foro Económico Mundial (WEF) indica que la mayoría de pequeñas y medianas empresas están preocupadas de adoptar prácticas o tecnologías de la Industria 4.0 por el temor de tener que invertir grandes cantidades de dinero, por la falta de conocimiento en el tipo de tecnologías que involucra, y ausencia de habilidades internas para sacar un proyecto de estos adelante.
Lo que a menudo se pasa por alto —y que recordó recientemente Bernd Rohde, Director General Hannover Fairs México, durante la presentación a medios del evento Industrial Transformation México, que tendrá lugar en León, Guanajuato, del 9 al 11 de octubre— es que más allá de las tecnologías abrumadoras que se asocian con este concepto, el núcleo de la Industria 4.0 son los datos, la conectividad entre los distintos sistemas y recursos de la planta, y el análisis de la información interconectada.
El llamado, entonces, es a repensar los negocios desde lo digital y desde los datos. Esto puede lograrse priorizando las áreas en las que la digitalización puede ofrecer los mayores beneficios, actualizando lo que tiene en funcionamiento, construyendo nuevos modelos operativos, comprando nuevas tecnologías, asociando las máquinas que ya están operando, y capacitando a su personal. Internamente, sus máquinas heredadas (legacy machines) deben transformarse o conectarse para permitir interacciones a lo largo del ciclo operativo y, más importante aún, esas máquinas deben empezar a hablarle con datos y usted debe desarrollar las habilidades necesarias para saberlas escuchar y analizar.
Digitalización de máquinas-herramienta: posible para todos
Con la misma idea que fundamenta este artículo, investigadores del Centro de Investigación de Manufactura Avanzada (AMRC) de la Universidad de Sheffield, en Reino Unido, quisieron demostrar que la digitalización de máquinas antiguas, pero todavía operativas, es posible y asequible para pequeños y medianos talleres a través de tecnologías económicas de sensórica y de comunicación en la nube.
Inicialmente, y por solo unos pocos cientos de libras esterlinas, fue posible habilitar para la Industria 4.0 un torno Colchester Bantam de 1956 y una fresadora Bridgeport de 1980. El objetivo fue comenzar a capturar métricas básicas de producción de estos equipos como Overall Equipment Effectiveness (OEE), costos operativos, condiciones de máquina y control de procesos, entre otros.
La máquina Colchester Bantam fue reacondicionada con un acelerómetro en cada uno de los motores (Adafruit MMA8451), caja de cambios y carro (Adafruit ADXL335) para medir las vibraciones a través de la máquina. Los datos de vibración se utilizaron para indicar una serie de parámetros, incluido el desequilibrio y la configuración deficiente de la pieza o la herramienta. Se instaló un sensor de temperatura digital (Maxim DS18S20) en la unidad de accionamiento del motor. La temperatura del cabezal también se consideró como un componente importante dentro de la máquina para controlar la temperatura; sin embargo, sin desmantelar la máquina por completo, se pensó que era demasiado invasivo y no una simple modificación para este proyecto.
También se instaló un sensor simple de transformador de corriente de núcleo dividido (LEMATO-10-B333-D10; 1: 1000, 10A) dentro del gabinete eléctrico de la máquina. La posición del carro se midió utilizando un sensor de distancia de tiempo de vuelo (TOF) (Adafruit VL53L0X) montado en el cuerpo de la máquina y un pequeño dispositivo reflector fijado al carro móvil. La velocidad del husillo se determinó utilizando un sensor de posición digital de efecto hall (Honeywell SR3 Series) y un imán de neodimio fijado al husillo de rotación.
Las mediciones de los sensores instalados en el torno Colchester Bantam se obtuvieron utilizando un microcontrolador Arduino (Mega 2560, £ 35) con capacidades de reloj en tiempo real (RTC). Los datos se adquirieron con preprocesamiento antes de enviarse a través del puerto serie Arduino a una Raspberry Pi (modelo 3B, £ 34). La función del Raspberry Pi era actuar como puerta de enlace de red, punto de acceso inalámbrico, procesador de datos y servidor web.
A medida que los datos del Arduino llegaron al puerto serie de la Raspberry Pi, NodeRED se utilizó para manipular esos datos, analizarlos en varias estructuras diferentes para que estuvieran disponibles en varios servicios. Estos servicios incluyen una base de datos SQL interna, una base de datos SQL basada en la nube y un sitio web HTML5 que utiliza sockets web simples.
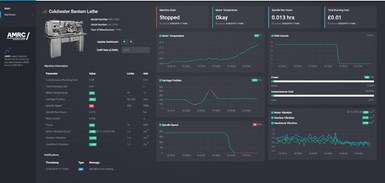
Panel de visualización de los parámetros de registro definidos para el torno Colchester Bantam de 1956. Foto: AMRC.
También se configuraron alertas simples dentro de la interfaz web para demostrar métodos básicos de notificación de problemas. Se definieron los límites de temperatura, vibración y posición del carro. Si la máquina se desvía fuera de estos límites, se genera una notificación. Esto se demostró a través de indicadores en el sitio web, pero también podría tener la capacidad de alertar problemas por correo electrónico o mensaje de texto si es necesario. Además, los gráficos se codificaron por colores según el estado actual del parámetro para una identificación más intuitiva.
La misma actualización, pero con un presupuesto más elevado, se desarrolló en la fresadora Bridgeport. Más allá de demostrar que es posible darles una nueva vida y oportunidad a estas máquinas, el AMRC concluyó que el costo inicial asociado con este tipo de reacondicionamientos es significativamente menor si se tienen en cuenta los beneficios en monitoreo basado en condición y en el mantenimiento predictivo.
“Existe la necesidad de que los proveedores de hardware industrial ofrezcan opciones de instrumentación más económicas pero robustas, adecuadas para un negocio pequeño donde el presupuesto para la modernización de los equipos no sobrepasa los 20,000 dólares”, señala el estudio de caso publicado por el AMRC.
De igual manera, Matei Moldovean, ingeniero de software del AMRC, sostuvo durante la presentación de este proyecto en el evento MACH 2018, que el interés que ha despertado esta demostración “muestra qué determinación tienen las empresas para preservar y actualizar los procesos de manufactura heredados que aún proporcionan valor, aprovechando los beneficios potenciales de las tecnologías de la Industria 4.0 a través de inversiones de bajo costo”.
Desde la óptica del proveedor
En México son cada vez más los talleres y plantas que se suben al tren de la digitalización. Al menos así lo ve Jorge Santana, ingeniero técnico de marketing en Balluff, quien afirma que, con herramientas más fáciles e intuitivas de usar, y varias marcas que ofrecen servicios de actualización en los que se agregan complementos como controladores, tarjetas, sensores y programación, se puede llegar a visualizar el estado de una máquina sin tener que cambiar todo el inventario de la planta.
Así también lo resaltó Bosch Rexroth a través del white paper “A practical roadmap for the implementation of Industry 4.0”, en el que enfatiza que bien sea que las empresas quieran hacer un acercamiento escalado a la Industria 4.0 o consideren moverse al escenario digital por completo, siempre existe la preocupación sobre la viabilidad de escalar tecnologías digitales para que engranen con sus operaciones actuales y, peor aún, muchos fabricantes desconocen que existe un rango de tecnologías que permiten soportar la digitalización de sus infraestructuras sin la necesidad de reemplazar el equipo existente.
Santana, por su parte, enfatiza que toda máquina, material o producto tiene un tiempo de vida; sin embargo, la idea es prolongarla.
“Más allá de pensar en costos, lo que se debe tener claro es el panorama de lo que se quiere visualizar. Ya teniendo eso claro se puede determinar qué se necesita, quién lo va a ejecutar, y qué proveedores los pueden apoyar o asesorar en qué tecnologías usar. Obviamente debe haber una inversión inicial pero lo que hay que tener en cuenta es el costo beneficio. Puede ser una inversión alta al principio, pero siempre debe tenerse en cuenta que se recuperará”.
Las inversiones para capturar datos de una máquina convencional pueden incluir un controlador (un PLC, un CNC o una CPU). Luego viene el módulo de comunicación en el que se introducen todas las señales, ya sea entrada/salida, entradas analógicas, los sensores y actuadores y, por último, una interfaz para la obtención y visualización de los datos que se recogen.
“Digamos que un gerente decide que lo que quiere ver es dónde está determinada pieza o material dentro del taller. Lo ideal sería contar con marcas que ofrezcan productos de digitalización y que a su vez ofrezcan asesoría gratuita para la implementación de sus productos, o que cuenten con un servicio de llave en mano en donde se realice, desde la selección de las tecnologías, hasta la integración y puesta en marcha. Los clientes valoran más estas cualidades en los proveedores, lo que los hace socios de valor dentro de la cadena de suministro”, sostiene Santana.
Además, recuerda que con interfaces de comunicación como IO-Link (una subred compatible con todos los protocolos de bus de campo convencionales: Profibus, Profinet, Ethernet-IP, Devicenet, CC-Link y EtherCat), se pueden obtener más ventajas de los dispositivos del taller como expansión de las señales y de los módulos, para la detección de los sensores, y el análisis en tiempo real.
Por el lado de Bosch Rexroth, su tecnología IoT Gateway —que combina hardware (sensores instalados en una celda, máquina o herramienta) y software (que se basa en sistemas operativos Linux, así como varias aplicaciones Java y otras interfaces abiertas)— les permite a las empresas digitalizar su maquinaria de producción, sin la necesidad de un amplio cableado, reequipamiento o reemplazo de los activos existentes, como lo destaca en su white paper.
Para demostrarlo, la empresa realizó su propio reacondicionamiento. Se trata
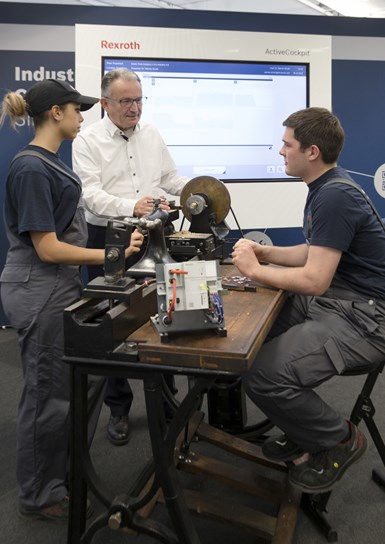
Con su tecnología IoT Gateway, Bosch Rexroth adaptó para la Industria 4.0 un torno de hierro fundido de 300 kg, de Robert Bosch, fabricado en 1887. Foto: Bosch Rexroth.
de un torno de hierro fundido de 300 kg, de Robert Bosch, fabricado en 1887. Comenzaron montando sensores en la máquina que, cuando se vinculaban con IoT Gateway, recopilaban datos sobre parámetros de rendimiento como: temperatura, presión, vibración, consumo de energía, inclinación del ángulo y velocidad de rotación. El IoT Gateway transmitía estos datos a un monitor que mostraba los resultados a los operadores del torno de una manera que fuera comprensible y accionable.
“Se lograron dos resultados significativos. Primero, el acabado superficial de una pieza torneada se rige por una combinación de velocidad de rotación y velocidad transversal de la herramienta de corte. El monitor se programó para mostrar las ventanas de velocidad mínima y máxima. Luego, el operador puede ajustar su velocidad del pedal para mantenerse dentro del margen, garantizando así un acabado superficial de calidad. También protege la herramienta de torno contra daños o desgaste”, indica el documento.
Además, con esta actualización los operadores pueden identificar cambios en la transmisión por correa que anteriormente podrían haberse perdido. Los sensores reconocen las desviaciones y notifican a un trabajador de mantenimiento una vez que se haya alcanzado el umbral predefinido.
“El torno de pedal es un buen ejemplo de cómo la maquinaria heredada, incluso la que se remonta a la primera Revolución Industrial, puede convertirse en parte de una infraestructura conectada y digitalizada. Además, demuestra cómo la capacidad de la Industria 4.0 puede continuar logrando un retorno de la inversión de maquinaria que tiene más de un siglo de antigüedad”, puntualiza el texto.
Transición de la mano de la academia
Cuando se dio la primera Revolución Industrial, impulsada por el desarrollo del agua y el vapor, el porcentaje de base instalada de equipos que debió ser reemplazada en la industria alcanzó el 100%. En la Cuarta Revolución Industrial este porcentaje solo alcanza el 40 o 50% ya que o bien las máquinas existentes ya están conectadas con los sistemas ciberfísicos, o se puede dar un reacondicionamiento de estas.
Con la premisa de que la Industria 4.0 más que una transformación, es una adaptación, en Monterrey surgió la iniciativa Lab Industria 4.0, que funciona como un esquema de triple hélice entre la Universidad Regiomontana (U-RRE), el Monterrey Interactive Media & Entertainment Cluster (MIMEC) y la Cámara Nacional de la Industria Electrónica de Telecomunicaciones y Tecnologías de la Información (CANIETI) como socios estratégicos. Su objetivo es ser el primer Centro de Innovación Industrial 4.0 a través del desarrollo y certificación del talento, la integración tecnológica de soluciones inteligentes, la investigación aplicada, y la promoción de emprendimientos basados en machine to machine (M2M), Internet of Things (IoT) y Big Data Analytics (BDA).
Para su director, Salvador Barrera, un primer paso para una empresa que quiera comenzar con el proceso de digitalización de sus operaciones es acercarse a una cámara sectorial o clúster y con ello a los laboratorios que cada una de estas tiene dependiendo el giro del taller.
“Como laboratorio nosotros tenemos la lista de las empresas que habilitan este tipo de tecnologías o de procesos. Si tenemos la necesidad de dar una solución a una empresa en materia de 4.0, nosotros hacemos el barrido de la información de lo que requieren, y avalamos el desarrollo del proyecto junto con las empresas que nosotros consideramos que son las que pueden responder al requerimiento”, comentó.
Asimismo, avanzan en la consolidación de un paquete de diplomados centrados en los procesos que son necesarios para la industria a corto plazo como, por ejemplo, protocolos de comunicación IIoT para Industria 4.0, simulaciones, manufactura aditiva, realidad virtual y aumentada, materiales avanzados, robótica colaborativa, entre otros.
A la fecha, ya van 20 clases impartidas en el Lab y 107 personas capacitadas en protocolos de comunicación y en arquitectura de Big Data, OPC/UA, TCP/IP, Profinet/bus, y Big Data Architecture. Entre otros, cuentan para ello con una estación de ensamble y procesamiento de piezas con robot (Mitsubishi), dos robots colaborativos autónomos, estación AS/RS de almacenamiento de producto en proceso y terminado con protocolo RFID, estación de maquinados CNC, inspección dimensional con cámara de visión, estación de medición de variables y sensores para automatización, entre otros equipos y software.
Contenido relacionado
Optimizando la manufactura con el Internet de las Cosas (IoT)
El Internet de las Cosas simplifica la automatización con sensores de bajo costo, conectividad rápida y almacenamiento en la nube. Descubra a través de un caso práctico en Georgia Tech cómo los fabricantes pueden aprovechar esta tecnología para optimizar procesos.
Leer MásMecanizado de precisión: herramientas y simulación
El software de simulación y una cuidadosa atención a los parámetros de las herramientas le han permitido a Major Tool acometer ambiciosos proyectos con su compleja maquinaria.
Leer MásInspección por rayos X: la nueva era de la metrología dimensional
La manufactura basada en datos recibe un impulso con una nueva línea de equipos de inspección por rayos X que genera un gemelo digital de la pieza mecanizada, incluidas representaciones 3D completas de las dimensiones internas y externas.
Leer MásLa inteligencia artificial en la manufactura: cómo llevarla a su taller
Conozca los factores críticos para implementar con éxito la inteligencia artificial en procesos de manufactura y su impacto en la calidad y productividad.
Leer MásLea a continuación
Comunicación 5G: datos que viajan a toda velocidad
Las redes móviles de quinta generación (5G) ofrecen beneficios inmejorables para los usuarios industriales, facilitándoles planificar su camino en el viaje hacia la Industria 4.0. La llegada de la red 5G a México es un evento esperado con anticipación.
Leer MásSiete claves sobre el Internet de las Cosas y la Industria 4.0
Cuando todas las máquinas y herramientas estén conectadas con todo lo demás en el taller, la manufactura tendrá un aspecto muy diferente.
Leer MásCNC o control numérico por computadora: qué es y cómo funciona
El Control Numérico Computarizado (CNC) revoluciona la manufactura moderna a través de la automatización precisa de máquinas-herramienta. Este artículo examina los fundamentos técnicos del CNC, desde sus sistemas de coordenadas y programación de movimientos hasta las funciones avanzadas que maximizan su eficiencia en el mecanizado industrial.
Leer Más