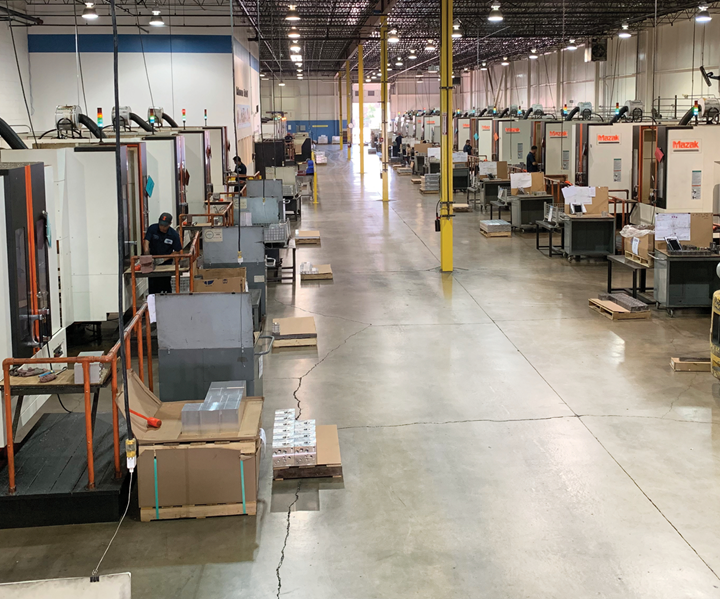
Este no es un truco de copiar y pegar de Adobe Photoshop. Esta es la “Fábrica de Rendimiento” de Tomenson Machine Works, donde la mayoría de los trabajos de perforación se realizan para sus colectores. Lo que hace que esta área sea tan única es la gran cantidad de centros de mecanizado horizontal Mazak alineados a ambos lados del corredor. Pero, más que eso, el taller ha estado comprando el mismo modelo (en la medida de lo posible) desde principios de los años 80.
Todo en Tomenson Machine Works es intencional. Cada elección, desde el trabajo que acepta, el flujo desde la materia prima hasta el producto terminado alrededor de su instalación en forma de U de 100,000 pies cuadrados, hasta las marcas y modelos específicos de sus centros de mecanizado, está dirigida a la estandarización. Al estandarizar todo su proceso de producción, Tomenson ha encontrado una manera no solo de funcionar de manera eficiente y predecible, sino también de capacitar a los nuevos empleados con facilidad.

De izquierda a derecha: Zach, Scott y Alex Roake se paran frente a dos de las 40 máquinas Mazak del taller.
El camino hacia la simplicidad ha sido largo y ha requerido dedicación. Llegar a este grado de estandarización tomó tiempo y esfuerzo por parte de tres generaciones de miembros de la familia, comenzando con Thomas Roake, quien fundó el taller en 1977. Thomas dirigió el taller hasta 1993 con su hijo Scott Roake (de ahí el riff sobre “Tom e hijo” para el nombre de la compañía Tomenson).
En 1997, la compañía se mudó a su ubicación actual en West Chicago, Illinois. Scott es ahora el presidente de la compañía, y la tercera generación ha asumido roles de liderazgo, con los hermanos Alex Roake de 24 años como gerente de operaciones, y Zach Roake, como gerente de posproducción/calidad. A través de los años, los miembros de la familia se han concentrado en un proceso que le permite a la compañía enviar más de medio millón de colectores hidráulicos de precisión por año, junto con al menos otras 20,000 piezas por año, utilizando apenas 70 personas, quienes en su mayoría llegaron al taller sin experiencia en mecanizado.
Dado el gran volumen para el nivel de personal, es de esperar que la historia de Tomenson sea sobre automatización. Pero se trata de algo más. Este taller se ha preparado para la eficiencia y la mejora continua mediante la estandarización de tres formas principales: 1) especializada en colectores hidráulicos de precisión, 2) comprando nada más que modelos similares de centros de mecanizado horizontal de Mazak y, 3) desarrollando e integrando software personalizado que se usa en iPads para unir el trabajo de cada empleado y departamento en el negocio.
Máquinas Mazak en todo el taller
Vamos a caminar. Al ingresar a Tomenson Machine Works, se encontrará en un patio interior recientemente renovado. El resto de la instalación se envuelve alrededor de este lugar común centralizado en una U invertida gigante, dividida en ocho unidades. Todas las unidades tienen ventanas de vidrio y fácil acceso al área del patio. Cuando Tomenson se mudó allí por primera vez, estas unidades albergaban otros negocios, pero con el tiempo Tomenson ha adquirido cada unidad, una por una, por lo que ahora es dueño de todo el inmueble, una instalación prácticamente perfecta para el flujo de trabajo estandarizado. Ahora, recorrer las 8 unidades en la “U” es recorrer el proceso de Tomenson. La primera puerta desde la derecha del patio es la Unidad 1: materia prima entrante. Todo el trabajo finalmente fluye hacia arriba, hacia la izquierda y hacia atrás por la U hasta que llega a la Unidad 8: envío.
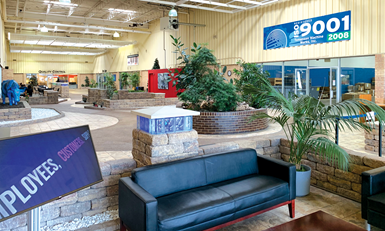
Un recorrido por Tomenson siempre comienza en el patio. La instalación se envuelve alrededor de esta área centralizada en forma de U invertida. Ingresando a las puertas bajo el letrero ISO 9001 se encontrará en la Unidad 1: materias primas entrantes. Caminando hacia arriba y alrededor de las instalaciones, y se sale por las puertas a la izquierda.
Los esfuerzos de estandarización de Tomenson son evidentes a partir de la Unidad 1. La compañía utiliza solo un proveedor para los bloques entrantes de aluminio, acero y hierro. En el pasado, el taller cortaba los bloques, un aparente ahorro de costos que de hecho agregaba complejidad al proceso. Ahora, la compañía ordena sus materiales en tamaños estándar precortados que están listos para el mecanizado.
En la parte superior de la U están las Unidades 4 y 5, denominada la “Fábrica de rendimiento”. Aquí es donde tiene lugar el mecanizado del colector principal. Ambos lados de la pasarela central están flanqueados por nada más que centros de mecanizado horizontal Mazak. Y cualquier recorrido por el proceso del taller simplemente tiene que detenerse aquí para considerar (quizás incluso maravillarse) la impresionante similitud y la gran cantidad de máquinas en esta sección del edificio: 40 en total, funcionando 24/7.
En la medida de lo posible, Tomenson ha estado comprando la misma marca y modelo de centros de mecanizado horizontal Mazak desde principios de la década de 1980, cuando el taller adquirió su primer centro de mecanizado CNC. Mazak ha avanzado y mejorado sus máquinas desde entonces, pero esta es la única razón de las diferencias entre las máquinas en esta bahía. Durante décadas, Alex dice que la compañía ha adoptado el “enfoque de Southwest Airlines”, refiriéndose a la aerolínea que compra un famoso modelo de avión. Algunos talleres siguen siendo fieles al fabricante de una máquina-herramienta, pero Tomenson también se ha mantenido fiel a un modelo de centro de mecanizado horizontal.
Mejora continua a través de la estandarización
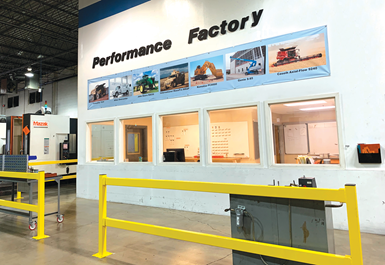
A diferencia de algunos talleres metalmecánicos, Tomenson se esfuerza por comunicarles claramente a sus empleados y visitantes exactamente quiénes son sus diferentes clientes, como se ve en el letrero que se encuentra sobre la sala de control en la Fábrica de Rendimiento.
Fue hace décadas, durante la transición del taller de máquinas manuales a CNC, que Tomenson decidió estandarizar sus ofertas de productos, centrándose casi exclusivamente en el mecanizado de colectores hidráulicos. Los pedidos de estas piezas, una mezcla de volúmenes altos y bajos, cambiaron la trayectoria de la empresa debido a la forma en que muchos de estos trabajos se ejecutan durante meses, sino años.
Debido al enfoque en colectores, casi todo el mecanizado realizado en Tomenson es para hacer agujeros, y casi todos estos agujeros están orientados en direcciones de ángulo recto, lo cual es un trabajo perfecto para los centros de mecanizado horizontal con ejes X, Y y Z, solamente, y un eje B pivotante. Cuando un colector requiere que se mecanice un agujero en un ángulo compuesto, ese trabajo se realiza en una operación secundaria en una máquina de cinco ejes. Los ciclos de mecanizado para colectores pueden funcionar durante dos horas o más, ya que el taller ejecuta las piezas en lotes. Debido a esto, el setup en cualquier máquina no tiene que suceder con mucha frecuencia, pero cada máquina puede requerir de 5 a 10 setups por semana.
En el pasado, el setup solía ser un proceso en el que los operadores sacaban sus propias herramientas y construían sus propios accesorios. Sin embargo, la estandarización en colectores ha permitido que Tomenson desarrolle un proceso altamente eficiente en el que los empleados se coordinan para proceder rápidamente a través de cuatro pasos bien definidos: 1) fijación, 2) herramientas, 3) presetup (eliminación de fijación y herramientas de trabajos anteriores) y 4) ejecutar la primera pieza. Además, el trabajo de colectores le ha permitido a Tomenson desarrollar herramientas y accesorios personalizados que la empresa puede estandarizar en gran medida. El sistema de setup de cuatro pasos se ha vuelto tan eficiente que Alex cuestiona ciertos tipos de automatización. “Agregar más complejidad a un proceso no siempre lo hace más eficiente”, dice. “A veces, en realidad lo hace menos eficiente”.
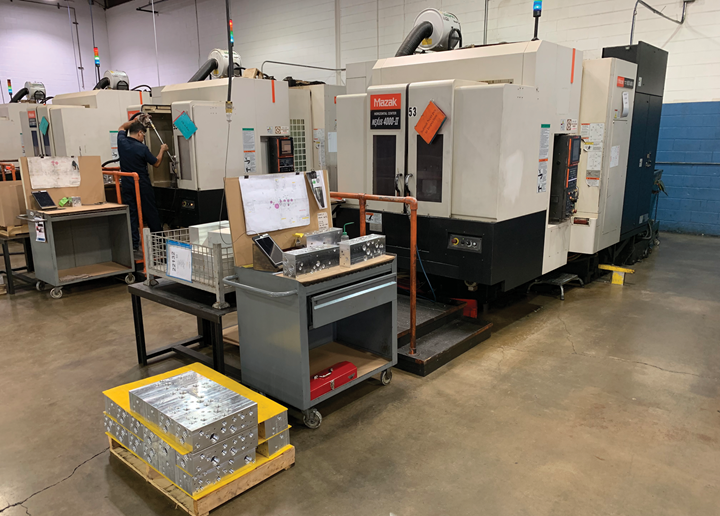
Señales visuales simples, como el color del pliego en los palets (el amarillo va al mecanizado secundario), la señalización de color en la parte delantera de las máquinas (el azul significa que está bien para operar y el naranja significa enviar las siguientes piezas a inspección), entre otras, ayudan a los empleados a saber de un vistazo qué debe hacerse con el trabajo.
El taller ha implementado una variedad de señales visuales para asegurarse de que el trabajo termine en el lugar correcto. Por ejemplo, al mirar alrededor del taller, cualquier cosa apilada en un patín con cartón amarillo tendrá un agujero en ángulo en el mecanizado secundario, todo lo apilado en un patín con cartón marrón se desbarbará y cada máquina que muestre un cartel verde indica que el trabajo ha recibido la inspección de primera parte.
Una solución para la brecha de habilidades
La estandarización en un modelo de centro de mecanizado horizontal también es valiosa por la forma en que optimiza el sistema de capacitación de Tomenson. A menudo, dice Alex, la compañía tiene que contratar empleados sin experiencia en el manejo de máquinas CNC. Siendo ese el caso, todos los empleados en esta sección del taller son contratados como operadores. Después de adquirir experiencia, pueden avanzar en su capacitación y trabajar para llegar a un puesto de configuración, lo cual es una posición deseable en la empresa porque requiere resolución de problemas y proporciona una variedad de trabajos. Tener solo una máquina para aprender prepara a los nuevos empleados para el éxito, y hace que sea más fácil para los operadores (y programas) ser intercambiables. “Nuestros operadores conocen todas las máquinas, y de esta manera, conocen todas las soluciones simples”, dice Alex. Esto también le ha dado al taller la capacidad de tener solo una persona de mantenimiento dedicada al equipo.
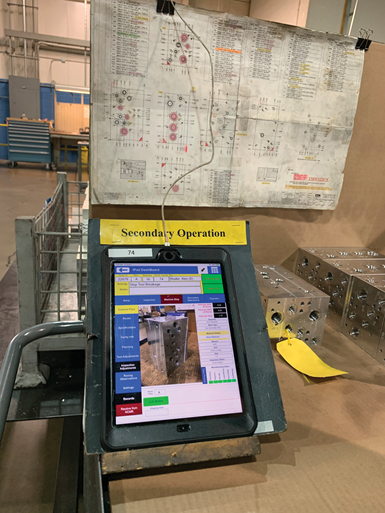
Cada máquina Mazak tiene su propio iPad con acceso al sistema de gestión de talleres propio, FilePro. El sistema comunica toda la información necesaria sobre el trabajo que fluye a través del taller, haciendo de la capacitación algo que casi puede ser autodidacta. Dicho esto, todavía se pueden encontrar planos originales después de los trabajos en el taller, aunque los empleados que confían en ellos aún son responsables de ingresar la información actualizada en FilePro.
Eficiencias como esta han permitido que la compañía ahora sea más ágil que antes de la Gran Recesión. Cada operador es responsable de varias máquinas, y la función principal del operador es mantener las máquinas en funcionamiento. Con el tiempo, el taller ha podido ampliar la cantidad de máquinas que cada persona puede supervisar de manera efectiva. Según Alex, Tomenson empleó a más de 200 personas en 2012. Hoy, gracias a mejoras como esta, dice que la compañía emplea a unos 70, pero son dos veces más eficientes que en el pasado.
El pegamento que lo mantiene todo junto
El nivel final de la sofisticada estandarización de la compañía depende de su software personalizado, “FilePro”, que Scott desarrolló durante un período de 10 años. Durante este tiempo, vio cuán necesario era tener un núcleo central que pudiera comunicar efectivamente la información requerida en todo el negocio. Los empleados de setup, operación, inspección, desbarbado y envío tienen acceso al software utilizando sus propios portales, a los que se puede acceder en cualquiera de los 60 iPads de Apple ubicados en el taller. Los empleados simplemente inician sesión con su número de empleado y registran su información de producción.
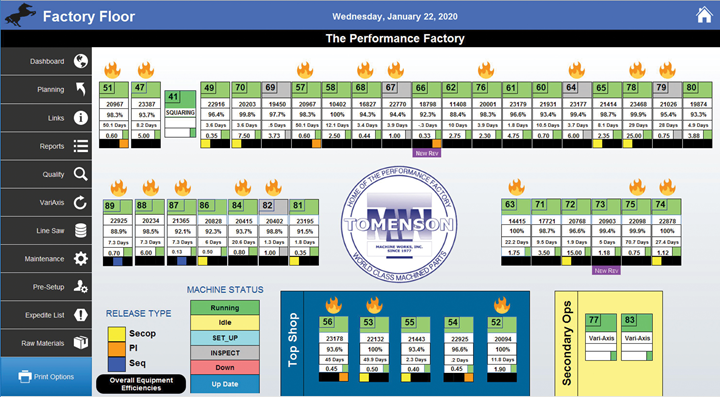
El software FilePro tiene paneles centrales con información específica para ciertos empleados y departamentos. Esta es una vista digital de Performance Factory, que se puede ver desde la sala de control en el medio de esa área. El software ofrece una representación visual de las máquinas, tal como se presentan en las Unidades 4 y 5, y qué trabajos se ejecutan en cada máquina.
Según Alex, Tomenson usa FilePro para cada entrada de información de taller que la compañía ha podido reconocer. “El sistema iPad es verdaderamente único”, dice, refiriéndose al inusual proceso que tomó el taller para desarrollar un sistema de administración propio en la plataforma de Apple.
“Incluso el reloj se maneja a través del sistema. Rastreamos muchos datos. Podemos decir cuándo las piezas se deteriorarán antes de que suceda. Lo ponemos en un gráfico y podemos ver si las tolerancias están fuera de rango”.
Si una máquina se cae, el operador puede tomar una fotografía y escribir una descripción del problema. Esto alerta a los empleados de configuración por correo electrónico para que se apresuren a la máquina y la pongan en funcionamiento lo antes posible, dice Alex. FilePro también se utiliza para almacenar información para las herramientas estandarizadas y personalizadas de la empresa. El personal de presetup puede acceder a los datos de la herramienta, a las listas de herramientas, a las instrucciones de fijación y a la información de programación, y luego se puede enviar por correo electrónico al personal de configuración cuando la máquina está lista. Este centro de información central también garantiza que las máquinas siempre estén ejecutando el programa CNC más reciente.
Otro beneficio del sistema iPad es que es parte de la estrategia de capacitación de la compañía. “Dado que les hemos brindado a los nuevos empleados toda la información, casi se han capacitado en la inspección. Además, si están registrando una inspección que está fuera de tolerancia, no necesitan saber qué hacer para abordarla: se emitirá un ticket que explica automáticamente la situación”, dice Alex.
Y esta es solo la información que se usa en torno a la Fábrica de Rendimiento. FilePro también se usa en otros lugares. Sigamos, aún no hemos terminado con nuestro recorrido.
Posproducción
Detrás del cuarto de configuración se encuentra la sala de inspección. Debido al papel fundamental que desempeñan los colectores en la maquinaria de un millón de dólares, Tomenson siempre ha mecanizado sus colectores con altos estándares. Pero hace dos años, uno de sus clientes comenzó a exigir tolerancias de 400 micras en las partículas que quedaban en la pieza. Para cumplir con este requisito, la compañía ha diseñado una estación de lavado agresiva, por la que ahora pasan todos los colectores varias veces.
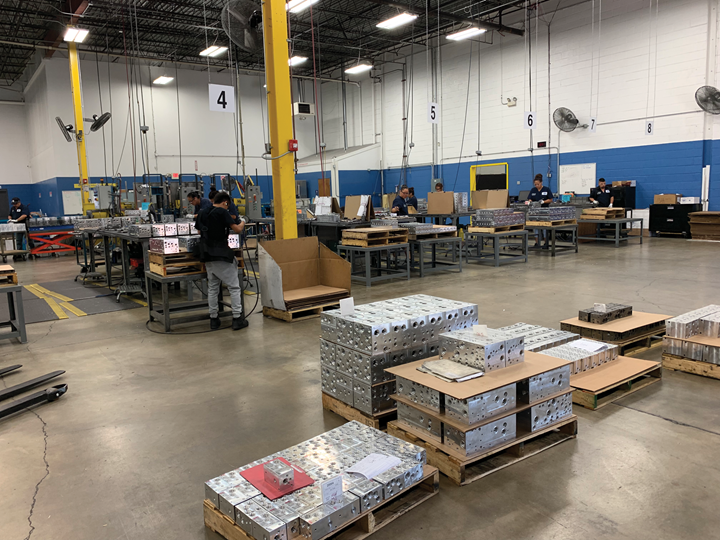
Esta es el área de desbarbado - Unidad 6. Una vez que los colectores se desbarban manualmente, pasan por una estación de lavado y luego al desbarbado térmico. Mediante el desbarbado de la línea de montaje, esto ahorra tiempo en más de 60 piezas de trabajo. Especialmente ahorra mano de obra si se detecta un problema en este proceso.
La unidad 6 está desbarbando. Así mismo, en respuesta a los estrictos requisitos de partículas, Tomenson decidió comenzar a utilizar un proceso de desbarbado térmico para complementar parte del desbarbado manual de sus colectores, un cambio que redujo la dotación de personal en 20-30 personas. Recientemente, Tomenson recibió un sistema Extrude Hone para el desbarbado térmico, que viene inmediatamente después del paso de lavado.
Desde el desbarbado, los colectores se trasladan a la Unidad 7 para el embalaje y a la Unidad 8 para el envío. En el empaque, el software FilePro juega otro papel crucial. Les da a los empleados señales visuales al mostrar fotos de cómo exactamente se deben empacar las piezas para su envío. “Es una parte importante del proceso que sería fácil pasar por alto”, dice Alex. Por ejemplo, si alguien accidentalmente etiquetó erróneamente un paquete o colocó el artículo incorrecto en un paquete enviado, es lo mismo que enviar una parte no conforme en términos de partes defectuosas por millón (dppm), dice. “Podría hacer todo bien durante todo el proceso de mecanizado y postproducción, pero si se envía el artículo incorrecto a los clientes, sería una falla enorme y costosa para nuestra empresa”. El escaneo de código de barras está integrado en el software FilePro para que se puedan rastrear las partes, y esta ID ahora ayuda a garantizar que cada parte se empaque como debe ser. El software tiene información sobre cuánto tiempo debe tomar empacar la pieza y fotos de cómo hacerlo, dice Alex.
Esta fina estandarización de Tomenson no sucedió de la noche a la mañana. Los miembros de la familia y los empleados han avanzado gradualmente para que el proceso de mecanizado de los colectores sea lo más fácil y eficiente posible. Y este proceso no se ha detenido. Según Alex, los empleados escriben constantemente sugerencias en el sistema iPad: la mejora continua está integrada en la cultura de la empresa. “Tomamos todas las sugerencias en serio y mejoramos las cosas a medida que se ejecuta el trabajo”, dice Alex. “Algunos trabajos los hemos estado ejecutando desde los años 90 y todavía estamos mejorando sus procesos”.
Contenido relacionado
Innovación y calidad en la manufactura de dispositivos médicos
Traufix, empresa mexicana con sede en San Miguel de Allende, Guanajuato, es reconocido como un líder en la manufactura de dispositivos médicos innovadores. El uso de centros de mecanizado de última generación le ayudó al taller a mejorar el proceso de fabricación de las placas para implantes óseos.
Leer MásSoluciones avanzadas de manufactura para componentes de precisión
Con cuatro nuevos centros de mecanizado de 5 ejes y dos células PH Cell Twin de DMG MORI, esta compañía refuerza su compromiso con la excelencia en la manufactura para sectores exigentes como el automotriz, médico y aeroespacial.
Leer MásMecanizado de precisión para componentes del sector energético
GMG Machining nace por la necesidad de fabricar piezas de precisión para la industria de generación de energía. La experiencia y el conocimiento del sector llevó a este proveedor de herramientas mexicano a convertirse en cliente de sus clientes. El uso eficiente de centros de mecanizado vertical y tornos de última generación le han permitido alcanzar las tolerancias exigidas por la industria.
Leer MásMecanizado de engranajes: materiales, herramientas y procesos
A medida que los vehículos eléctricos e híbridos ganan terreno, las estrictas exigencias de operación silenciosa y eficiencia energética impulsan innovaciones en el mecanizado de engranajes para maximizar la precisión, reducir el ruido y prolongar la vida útil de las transmisiones.
Leer MásLea a continuación
Por qué usar torneado tipo suizo
¿Para qué clase de producción se usan los tornos tipo suizo? ¿En qué se diferencian de los centros de torneado convencionales? Expertos y usuarios cuentan sus experiencias.
Leer Más¿Por qué usar torno-fresado?
Los fabricantes de máquinas-herramienta se dieron cuenta de que las piezas torneadas a menudo requerían también, al menos, algún trabajo de fresado o taladrado. Por ello aumentaron las capacidades de los tornos mediante husillos adicionales para el trabajo con herramientas giratorias. De esa manera surgieron las máquinas de torno-fresado.
Leer MásSistemas innovadores de sujeción para electroerosión y mecanizado de tres ejes
Con el propósito de aumentar el índice de ocupación de máquinas en el taller, este fabricante de moldes adaptó un dispositivo de sujeción en sus máquinas de tres ejes y su electroerosionadora de penetración para aumentar la flexibilidad de sus equipos y ser más competitivo.
Leer Más