Compartir
Cuando Ed Beaumont se planteó experimentar con la perforación robótica mediante electroerosión rápida, no existían SpaceX y mucho menos la industria espacial comercial. Ahora, dice, no podría haber imaginado un mejor caso de estudio para un proceso de perforación y conformación de agujeros de alta producción, que parece hecho a la medida para una era de talento escaso y enredos en la cadena de suministro.
Beaumont Machine, el especialista en equipos de electroerosión rápida para orificios que Beaumont fundó hace casi treinta años, ya había suministrado robots con sus máquinas de electroerosión. Sin embargo, no hay una máquina de electroerosión en SpaceX, al menos no en el sentido tradicional. Más bien, la manipulación del electrodo se le deja completamente al robot: un enorme brazo de ABB Robotics que maniobra un taladro de electroerosión de 609 mm de largo, similar a una jeringa, alrededor de la parte cónica aún más masiva, que gira sobre una mesa giratoria de 2.44 metros de diámetro.
Demasiado grande, incluso para la carcasa de la máquina más grande, esta pieza de trabajo requería un medio alternativo para perforar los numerosos orificios alrededor de su diámetro, que están colocados y formados con precisión para moldear el flujo de aire de enfriamiento que mantendrá el material intacto en los tramos superiores de la atmósfera de la Tierra.
“Los robots nunca se habían utilizado para la electroerosión de esta manera”, dice Beaumont, aunque esto no se debe a que la tarea haya sido imposible. Más bien, había sido poco práctico, al menos hasta hace poco. Ahora espera ver a otros replicar el éxito de SpaceX, y no solo para grandes partes.
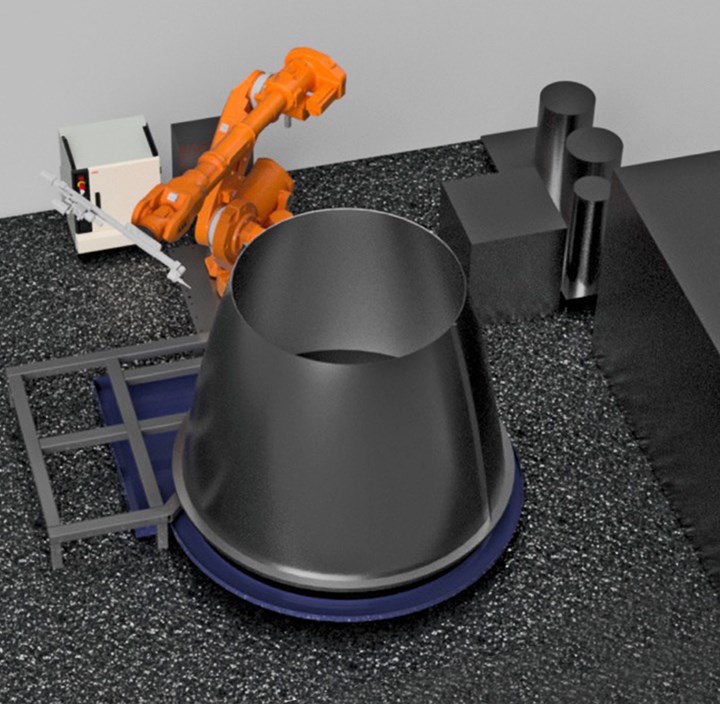
Aunque el sistema de perforación por electroerosión en SpaceX cambia una carcasa de máquina-herramienta por un robot de seis ejes, el sistema general todavía está cerrado por razones de seguridad. Fotos cortesía Beaumont Machine.
De hecho, imagina filas de brazos más pequeños, de seis ejes, que durante todo el día inyectan electrodos cilíndricos, cargados y delgados como un alambre, en aleaciones a base de níquel y otros materiales de grado aeroespacial, y con una pausa entre ciclos para intercambiar herramientas.
Cualquiera que sea el tamaño de la pieza, los brazos robóticos pueden ocupar menos espacio que las máquinas-herramienta cerradas, son más fáciles de reemplazar o reorganizar y tienen una tasa entre fallas más larga.
Sin embargo, la electroerosión rápida de orificios articulada por robot es posible por razones que van más allá del continuo avance y adopción de la automatización de robots. Superar el obstáculo más importante, la precisión del posicionamiento del robot, fue un gran reto para el equipo de Beaumont Machine.
El principal reto consistió en integrar el brazo en el sistema de control de Siemens con la misma precisión que cualquier conjunto de ejes de máquina accionados por tornillos de bolas.
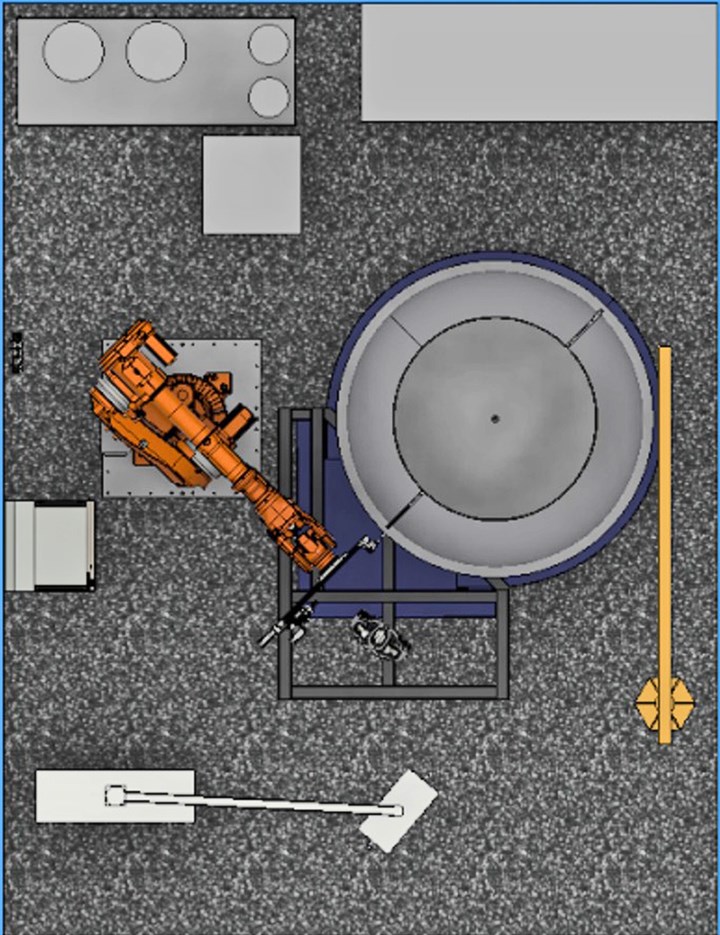
Como se ve en los modelos 3D, el sistema se basa en algo más que un robot. Los elementos también incluyen una mesa giratoria; una grúa grande (visible en amarillo); una estación de almacenamiento para electrodos y guías intercambiadas por el robot; por supuesto, la fuente de alimentación de la electroerosionadora. Otras consideraciones comunes a cualquier sistema de orificio rápido incluyen la gestión del agua y el aislamiento eléctrico para todo el sistema.
En el mundo de la electroerosión, el bucle de retroalimentación del control CNC no deja espacio para los tipos de transferencia de datos entre la máquina-herramienta y el robot que caracterizan el manejo de piezas, el cambio de herramientas y otras aplicaciones tradicionales, en las que el brazo automatizado es esencialmente un complemento.
“Poner el robot en el asiento del conductor”, como él dice, requiere un control directo, y para eso, “podemos hacer mucho mediante una verdadera interfaz con el CNC”.
La historia se repite
Beaumont Machine no es ajena a los trabajos profundos de CNC. De hecho, escuchar a Ed Beaumont explicar lo que está dispuesto a revelar aclara hasta qué punto la aplicación de SpaceX es un eco del pasado. Un ejemplo es el trabajo de calibración y compensación de errores. “Si entiendes cómo funciona el CNC, esencialmente puedes programar en torno a cualquier problema que puedas tener”, dice.
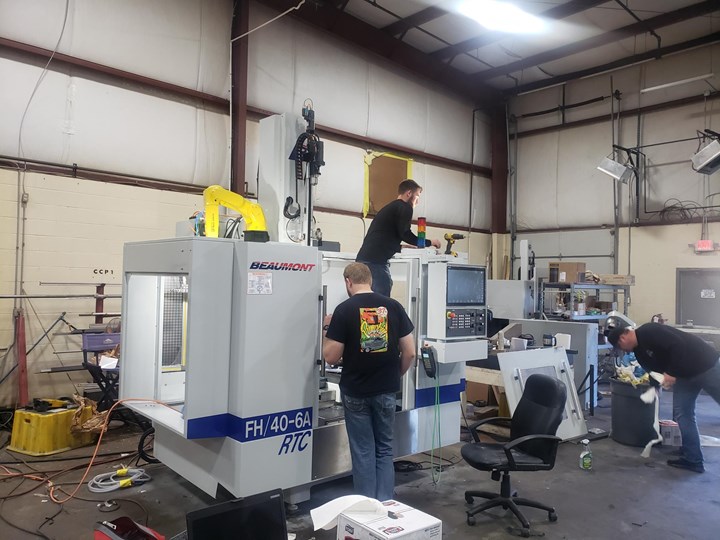
El equipo de Beaumont proporciona equipos de electroerosión, consumibles y soporte de ingeniería de aplicaciones a clientes de todo el mundo desde las instalaciones de la compañía en el suroeste de Ohio.
La compensación y calibración CNC es esencial, sin importar cómo se manipule el aparato de perforación. Llenar las superficies de las piezas con orificios diminutos y de precisión requiere coordinar una compleja dinámica entre la pieza de trabajo y la unidad de perforación, explica Beaumont.
Las máquinas-herramienta de la empresa ofrecen diversos medios para ello, como cabezales angulares, múltiples ejes lineales y mesas giratorias basculantes. Algunas máquinas tienen, incluso, un eje independiente para manipular el propio electrodo con el fin de que se mueva a lo largo de X o Y, una capacidad que suele emplearse para dar forma a los conos y contornos acampanados de los orificios en los difusores de las turbinas.
El bucle de control de la electroerosionadora nunca se puede cerrar realmente.
En aplicaciones articuladas por robot, la realización de orificios depende de la coordinación del brazo con otro medio de movimiento, como la mesa giratoria de alta precisión construida a la medida en SpaceX. Sin embargo, se aplican los mismos conceptos.
Dada la complejidad del equipo llave en mano de la compañía, trabajar con un robot que puede “torcer de cualquier manera su propio brazo y también hacer un giro de 360° al final” requirió flexionar esencialmente los mismos elementos competitivos que diferenciaron a Beaumont Machine en primer lugar, dice. “La forma como hemos manejado estos desafíos nos ha llevado a donde estamos”.
De hecho, Beaumont dice que había considerado flexionar esos elementos competitivos en la perforación robótica por electroerosión ya a mediados de la década de 2000. En aquel entonces, sin embargo, el desafío habría sido mucho mayor. Con las herramientas de software modernas, “realmente puedes resolver los movimientos —explica—. Se convierte más en una cosa X-Y-Z en lugar de ‘articulación 1 y articulación 2’”.
Sin embargo, tener la capacidad de mover la unidad de perforación a su posición no es la única razón para el control directo del robot CNC. En la electroerosión, dice Beaumont, mover la unidad de perforación a su posición no es suficiente por sí sola. El control preciso de la eliminación de materiales, particularmente en las tolerancias que los clientes esperan (que van a +/- 0.0003 pulgadas para algunas aplicaciones aeroespaciales), requiere un bucle de retroalimentación de datos lo suficientemente rápido como para proporcionar control a nivel de la chispa de remoción de material.
El bucle de retroalimentación del control de electroerosión
Los esfuerzos para desarrollar la interfaz entre el CNC y el robot reflejan el trabajo realizado por la empresa para conectar el otro extremo del bucle de retroalimentación de control: el proveedor de energía de la electroerosión que da forma a la chispa.
Tres años de colaboración con Siemens, que suministró el CNC 840di que ejecuta el sistema SpaceX, han sido fundamentales para garantizar las formas adecuadas de los orificios y las tasas de avance, así como la calidad general del proceso, dice Beaumont.
La conexión con la fuente de alimentación es importante para el posicionamiento del robot porque en un sistema Beaumont, el electrodo se sumerge en la pieza de trabajo a lo largo de su propio eje (W).
“El eje W es un verdadero eje CNC”, dice. Esto significa que se puede programar con precisión para extenderse a una cierta profundidad, lo que permite usar la punta del electrodo esencialmente como una sonda para ayudar en el posicionamiento. “Cada vez que el electrodo baja, se restablece a cero —explica Beaumont—. Investigamos varios puntos y hacemos que el controlador haga los cálculos para recentrar la pieza”.
La aplicación SpaceX es otra indicación de que las posibilidades de automatización se están expandiendo, y que el pensamiento de los fabricantes debe expandirse para coincidir.
Tanto para los robots como para los ejes de la máquina-herramienta, la retroalimentación de estos ciclos repetidos de “sondeo” es fundamental en el posicionamiento, porque el bucle de control de la electroerosionadora nunca se puede cerrar realmente, dice Beaumont.
Considere los medios de eliminación de material: un tubo largo y hueco que se enrosca a través de una guía cilíndrica, gira a miles de rpm y proporciona un conducto para una corriente de agua desionizada de 2000 psi, que descarga el material a través del espacio entre el trabajo y la punta del electrodo. El control esencialmente intenta mantener una brecha especificada, pero mantener la brecha es una ciencia inexacta, porque la cantidad de material erosionado a medida que el arco se dispara desde la punta del electrodo hasta la pieza de trabajo es alta e inherentemente variable.
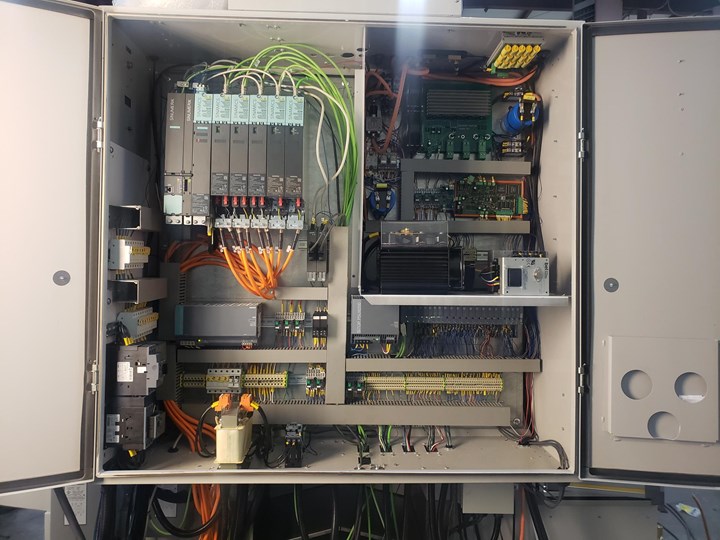
El panel eléctrico de una de las máquinas-herramienta de la línea FH, de Beaumont, es como el resto de la máquina, ya que cuenta con la menor cantidad de componentes posible, todos los cuales son fáciles de obtener y reemplazar.
Todo esto se suma a la necesidad de tener flujos de datos casi en tiempo real desde la fuente de alimentación hasta el CNC y el sistema de movimiento, cualquiera que sea la naturaleza de ese sistema de movimiento.
“El proceso cambia todo el tiempo”, dice Beaumont, citando fuentes de variabilidad, que van desde la calidad del agua y los electrodos hasta las inconsistencias de los materiales que pueden jugar impredeciblemente con las complejas fuerzas detrás de la erosión del material eléctrico. “La información tiene que volver al controlador en corriente y voltios, y velocidad y distancia, y todo esto debe calcularse en microsegundos para bombear esa información de nuevo”.
Incentivo para innovar
En cuanto a la posibilidad de que los brazos robóticos desempeñen funciones similares en otras aplicaciones, debe tenerse en cuenta que la electroerosión se presta particularmente bien al proceso. Por ejemplo, la precisión no requiere el mismo nivel de rigidez que las operaciones de mecanizado por contacto, que a menudo dependen de la masa de la máquina. Sin embargo, la aplicación SpaceX es otra indicación de que las posibilidades de automatización se están expandiendo, y que el pensamiento de los fabricantes debe expandirse para coincidir.
En este caso, solo hizo falta un incentivo. Para Beaumont, ese incentivo incluía tanto las dificultades de la cadena de proveedores, como la oportunidad de dar los siguientes pasos hacia el mismo objetivo que siempre ha perseguido la empresa: proporcionar plataformas de electroerosión estándar y modulares, que puedan ser atendidas con facilidad desde cualquier parte del mundo, pero que también sean “verdaderamente fabricadas en Estados Unidos”, dice.
Cuando la aplicación es adecuada, la articulación del robot podría ser la clave para limitar los componentes importados y construir un “producto verdaderamente grande” que siga mereciendo esa etiqueta.
Contenido relacionado
EMO: insertos de roscado de doble cara para la industria petrolera
Vargus presentó la nueva línea de herramientas MACH 25 enfocada en el mecanizado de componentes para la industria petrolera.
Leer MásValero invertirá 120 millones de dólares en Tamaulipas
Valero ampliará su presencia en Tamaulipas con una nueva terminal marítima en el Puerto Industrial de Altamira.
Leer MásCrece el Indicador de Pedidos Manufactureros en noviembre de 2024
El Indicador de Pedidos Manufactureros creció 1.5 puntos en su comparación anual, mientras que el rubro de productos metálicos, maquinaria, equipo y muebles aumentó 1.9 puntos.
Leer MásIndustria petrolera en México: urgen inversiones en exploración y producción
El sector petrolero mexicano experimentó un descenso en 2023, principalmente por la disminución en la exploración y extracción en aguas someras.
Leer MásLea a continuación
Por qué los talleres en México usan tornos tipo suizo
En México, el uso de tornos tipo suizo ha venido en crecimiento. Si bien empezó con aplicaciones dedicadas a la industria de la joyería y médica, ahora se utilizan para diversas aplicaciones en las industrias automotriz, electrónica, aeroespacial y de petróleo y gas.
Leer Más10 tendencias que se están tomando los talleres metalmecánicos mexicanos
Modern Machine Shop México resume las tendencias y tecnologías a observar por parte de los talleres de mecanizados en México.
Leer MásMesas magnéticas optimizan la electroerosión en producción de piezas complejas
Evolución en Moldes venía asumiendo varios retos para el mejoramiento de sus procesos de manufactura de componentes complejos para sus moldes. La aplicación de mesas magnéticas optimizó el mecanizado por electroerosión y mejoró sus tiempos de entrega.
Leer Más