Trends to Follow for The Manufacturing Industry in 2023
Managing uncertainty, addressing labor shortages, and boosting the supply chain resilience are some of the trends that the industry must follow in 2023, according to Deloitte.
According to the "2023 Manufacturing Industry Outlook" survey conducted by Deloitte, the manufacturing industry must consider five important trends in 2023, ranging from managing uncertainty, addressing labor shortages to boosting the supply chain resilience, among others.
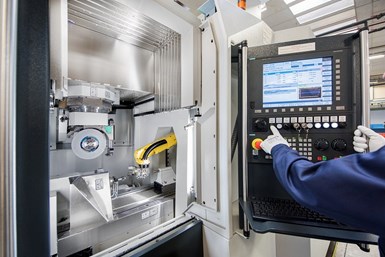
According to Deloitte, the manufacturing industry has increased its digital investment in recent years and accelerated the adoption of emerging technologies.
Investing in advanced technologies to mitigate risks
The document refers that the manufacturing industry has increased its digital investment in recent years and has accelerated the adoption of emerging technologies. It details that companies with greater digital maturity have demonstrated greater resilience, as have those that accelerated digitization during the pandemic.
"In the same way, companies with greater digital implementation tend to achieve greater supply chain visibility and are better able to adapt to supply chain challenges," the document reveals.
Furthermore, the report adds that the high level of uncertainty is expected to continue over the next 12 to 18 months, and manufacturers' digital strategies during this period are likely to be based on the following dynamics:
- Maintain the momentum: Investments in the right technologies can help manufacturers pivot quickly. For example, improved data and analytics capabilities can improve forecasting.
- Protect long-term profitability: Implement digital capabilities across the value chain can help ensure profitability, and manufacturers have multiple levers to engage when it comes to digital sophistication.
- Expand advanced manufacturing capabilities: Robotics and automation can improve efficiency, while Artificial Intelligence Artificial Intelligence (AI) and machine learning capabilities can provide the necessary edge.
Apply a wide range of talent management strategies
The research details that addressing labor shortages and turnover amid changing talent models will remain a priority for most manufacturers in 2023.
It adds that labor shortages, exacerbated by supply chain constraints, are reducing operational efficiency and margins, therefore, manufacturers are implementing several approaches to strengthen their talent retention strategy, which include:
- Wage increases: More manufacturers are forcing to consider raising wages because of the talent shortage.
- Upskilling: As the use of digital technologies proliferates in the manufacturing sector, the workforce needs more advanced technical and digital skills. However, skilled workers are in short supply in the manufacturing industry. Manufacturers are likely to emphasize strategies such as continuous training to upskill the workforce, as well as investing in startups to access new technologies and talent, among others.
- DEI strategy: The industry is focusing on diversity, equity and inclusion (DEI) to attract more women, racially and ethnically diverse groups into the workforce.
- Flexible work arrangements: Manufacturers are actively seeking ways to redesign work, the workplace, and the workforce to adapt to broader changes in the overall work culture. As the hybrid work culture begins to spread to parts of the manufacturing sector, companies are exploring ways to add flexibility to their entire operations.
Supply chain
A recent Deloitte supply chain survey highlights that 80 % of manufacturing executives surveyed have experienced a "strong" to "very strong" impact on their supply chains in the last 12 to 18 months.
According to this, 72 % of executives surveyed believe that persistent shortages of critical materials and ongoing supply chain disruptions represent the greatest uncertainty for the industry in the coming year.
Manufacturers are mitigating these risks not only with increased use of digital technology, but also with time-tested approaches:
- Relationship and supply chain management: Many manufacturers are working closely with suppliers as partners to navigate through the current disruption. These relationships can help them effectively pivot to alternative transportation routes or component sources.
- Create redundancy in the supply chain: Manufacturers are expected to continue to diversify their supplier base and add redundancy in the coming year. Supply chain executives should carefully evaluate the cost of multiple suppliers versus the benefits of increased agility and risk mitigation.
- Increasing local capacity: Many manufacturers have boosted local capacity by integrating their businesses across the whole value chain to reduce exposure to logistical issues and transportation bottlenecks.
- Implementing digital technologies: As manufacturers actively recalibrate their supply chain exposure, many are turning to digital capabilities that can increase visibility into their supply network and improve control and coordination.
Taking a holistic approach to smart factory initiatives
The survey details that manufacturers are likely to continue to move towards smart factory transformation as these initiatives drive future competitiveness.
"Many manufacturers are making investments to lay the technology foundation for their smart factories. Early adopters are improving connectivity through the cloud, Edge Computing and 5G. With the adoption of these foundational technologies, leading manufacturing companies are also likely to partner across their value chain," the survey indicated.
The survey details that once the Digital Core is established, manufacturers are investing in disruptive technologies such as Augmented Reality, Artificial Intelligence, Internet of Things, additive manufacturing, Blockchain and advanced analytics.
Focusing on corporate social responsibility
Finally, the survey refers that another trend is the rapidly evolving environmental, social and governance landscape that may require manufacturers to be closely monitored in 2023.
"Many organizations voluntarily comply with a complex grid of reporting regulations, ratings and disclosure frameworks; but regulators around the world are also moving toward requiring greater disclosure of non-financial metrics," the survey indicated.
It adds that manufacturers are moving toward these commitments by introducing operational changes throughout their value chain.
Contenido relacionado
Mata Automotive inaugura planta en Aguascalientes
Mata fabricará alrededor de dos millones de piezas al año para vehículos eléctricos de marcas como Tesla, Audi, Dodge, GM, entre otras.
Leer MásMéxico: perspectivas de crecimiento para la industria de autopartes
En 2023, la industria de autopartes en México prevé un crecimiento del 10.45 %, con un valor de producción de USD 115,802 millones, esto pese a desafíos como la huelga de UAW en EE. UU. El nearshoring ha jugado un papel clave.
Leer MásParamount New Materials invierte 200 millones de dólares en Coahuila
La planta iniciará operaciones en diciembre de 2024 y procesará piezas de aluminio como chasises, parachoques y otros componentes para la industria automotriz.
Leer MásIndustria automotriz en México: balance 2022 y proyecciones 2023
Conozca las estadísticas en producción, exportación y ventas de vehículos en México en 2022. Explore el impacto del nearshoring y la producción de vehículos eléctricos en la industria de autopartes.
Leer MásLea a continuación
Por qué los talleres en México usan tornos tipo suizo
En México, el uso de tornos tipo suizo ha venido en crecimiento. Si bien empezó con aplicaciones dedicadas a la industria de la joyería y médica, ahora se utilizan para diversas aplicaciones en las industrias automotriz, electrónica, aeroespacial y de petróleo y gas.
Leer MásMesas magnéticas optimizan la electroerosión en producción de piezas complejas
Evolución en Moldes venía asumiendo varios retos para el mejoramiento de sus procesos de manufactura de componentes complejos para sus moldes. La aplicación de mesas magnéticas optimizó el mecanizado por electroerosión y mejoró sus tiempos de entrega.
Leer Más10 tendencias que se están tomando los talleres metalmecánicos mexicanos
Modern Machine Shop México resume las tendencias y tecnologías a observar por parte de los talleres de mecanizados en México.
Leer Más