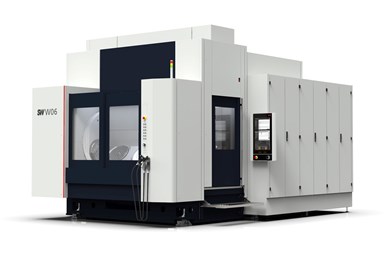
BA W06 es un centro de mecanizado horizontal de cuatro a cinco ejes especializado en el mecanizado de grandes componentes no ferrosos.
Schwäbische Werkzeugmaschinen GmbH (SW) ha lanzado su BA space3 y BA W06 para dar apoyo a los desafíos únicos de la manufactura de vehículos eléctricos.
SW afirma que el mecanizado de grandes componentes estructurales, como las carcasas de las baterías, a partir de metales ligeros es uno de los mayores retos de la manufactura de vehículos eléctricos, pero también afirma que la BA space3 está optimizada para esta tarea.
La máquina cuenta con un rango de trabajo de 3,000 x 1,800 x 875 mm en los ejes X, Y y Z, respectivamente. En cada uno de estos ejes, el husillo HSK 63 puede alcanzar un avance rápido de 120 m/min, con un tiempo de viruta a viruta de 4 a 4.25 segundos.
La BA space3 también se destaca por la flexibilidad de su versión de cinco ejes y el dinamismo de la versión de tres ejes con husillo rígido. La distancia a la mesa giratoria es de 165 – 1,040 mm para la versión de cinco ejes, y de 425 – 1,300 mm para la variante de tres ejes.
El BA W06 es un centro de mecanizado horizontal de cuatro a cinco ejes especializado en el mecanizado de grandes componentes no ferrosos, como carcasas de cajas de cambios de aluminio y torres de amortiguación. Su avance rápido alcanza hasta 120 m/min en los ejes X, Y y Z, y la última versión redujo el tiempo de viruta a viruta en un 10 %.
La BA W06 utiliza la construcción monobloque característica de SW, lo que significa que la máquina está construida como un cubo para aumentar la rigidez y la estabilidad.
La última BA W06 cuenta con una distancia de husillo variable de 590.00 mm a 651.00 mm, con un recorrido de los ejes Y y Z de 630 y 510 mm, respectivamente. El “tirón”, tanto en G1 como en G0 (los drives de avance del eje Y) se asigna a un valor máximo de sobreimpulso de 0.004 mm.
Los clientes pueden equipar la BA W06 con grandes husillos HSK 100 que admiten herramientas más grandes. SW afirma que la capacidad del husillo de motor síncrono se adapta bien a estas herramientas de mayor tamaño y resulta útil para el mecanizado de los orificios de la carcasa del estátor en las unidades de transmisión de los vehículos eléctricos.
Contenido relacionado
-
Cómo pasivar las partes de acero inoxidable
Descubra cómo la pasivación maximiza la resistencia a la corrosión en aceros inoxidables y evita la falla prematura de piezas y componentes mecanizados.
-
10 consejos para el fresado de titanio
Unas consideraciones simples de proceso pueden incrementar su productividad en el fresado de aleaciones de titanio.
-
5 errores críticos en el uso de máquinas CNC que debe evitar
Descubra los cinco errores más comunes en la operación de máquinas CNC, desde la elección de herramientas incorrectas hasta la manipulación inadecuada de funciones críticas.