Maquinsa inicio hace 25 años con el nombre de Maquinados y Utensilios de Madera para el Hogar en la Ciudad de México, en el patio de la casa de los padres del ingeniero Eduardo Retana. Allí se empezaron a producir los rebana papas, uno utensilios de madera que sirven para cortar la papa en hojuelas y quitarles la cascarilla a la papa y las verduras.
“Siempre la ilusión de mi hermano fue que ese utensilio se fabricara en plástico, por eso surgió la idea de adquirir equipo para fabricar los moldes”, explica el ingeniero Retana.
Con el tiempo, Maquinsa (Maquinados, Ingeniería y Construcción S.A. de C.V.) empezó a adquirir tornos y fresadoras para incursionar en la manufactura de moldes de inyección en zamak.
“Empezamos a hacer los moldes y nos dimos cuenta de que no se necesitaba tanta tecnología como ahora y que podíamos hacer esos moldes de inyección sin problema en una buena fresadora. Estamos hablando de 1990”, cuenta Retana.
Posteriormente, un ingeniero del Politécnico les ofreció hacer mecanizados con General Electric. Él les ofreció que hicieran la maquila de las mordazas donde llegan las líneas de alta tensión, que son unos conectores, hembra y macho, donde llega el cable y se aprieta como una especie de perno. Esos fueron sus primeros inicios en el sector del mecanizado.
Posteriormente, empezaron a tener más clientes para hacer roscas para válvulas de seguridad para la industria petrolera y algunos componentes para la industria agrícola. Una de esas empresas era Tractores Agrícolas, que actualmente es CNH y tiene sede en Querétaro. En 1999 se trasladan de Ciudad de México a la ciudad de San Juan del Río, donde vieron que había un área de gran oportunidad por el crecimiento que traía la ciudad de Querétaro.
“Teníamos dos tornos convencionales de la Segunda Guerra Mundial y dos fresadoras viejas y con eso empezamos. Los taladros de mano ya los teníamos, que es donde generábamos las roscas. Así empezamos haciendo trabajos de mantenimiento y, posteriormente, hubo el ahorro para comprar la primera máquina de control numérico en el año 2005. En ese año también compramos el centro de mecanizado”, explica el ingeniero Retana.
“Y en Querétaro también empezaba ese boom de la de la industria metalmecánica, entonces había poca gente que tenían máquinas de control, y fue como nosotros incursionamos en el mercado, empezando a hacer dispositivos para empresas como Mondragón, que son empresas que se dedican a integrar líneas de ensamble para el sector automotriz y para la industria en general”, relata Retana.
“Una vez que fuimos agarrando fortalezas en este sector, nos acercamos a empresas automotrices como Tremec, en el año 2005, igual que a Siemens. A Tremec les hacíamos mecanizados de componentes para la transmisión de transporte pesado y a Thyssenkrupp les realizábamos monturas para las líneas de ensamble para un robot. Posteriormente, no quisimos tener dependencia de la industria automotriz y vimos una oportunidad en el sector eléctrico. Empezamos a trabajar con Siemens en pequeñas líneas de producción y desde ahí empezamos a tener mayor crecimiento”, explica Retana.
Aprovechando todos los ejes en el mecanizado
Desde el año 2005 Maquinsa se ha venido desarrollando en la manufactura de piezas eléctricas. Actualmente, a Siemens le fabrican componentes para las cabinas de media y alta tensión. Se trata de muchos componentes, con muchos números de parte, hechas de aleaciones de acero al carbono, componentes de aluminio, componentes de acero inoxidable, latones y aleaciones especiales.
Sin embargo, para hacer piezas de mejor calidad y con mayor volumen de producción han necesitado hacer muchos cambios. “Lo que primero hicimos fue ordenar e iniciar un sistema de calidad para, de alguna manera, ser una empresa certificada y trabajar con procedimientos y controles con el fin de satisfacer los requerimientos de nuestros clientes. Una vez que logramos esto, el siguiente paso fue el lograr hacer pequeños dispositivos en nuestras máquinas, y tratar de ocupar la capacidad total de los ejes en los centros de mecanizado”.
Normalmente, en Maquinsa utilizan los centros de mecanizado para hacer piezas únicas y un paso importante para mejorar la productividad fue aprovechar todos los ejes del centro de mecanizado. Para ello, tuvieron la visión de crear dispositivos y monturas para poder meter en una sola operación desde 10 hasta 20 piezas en un palet y mecanizar de manera más eficiente.
Posteriormente, crearon otros palets de intercambio rápido en lugar de tener centros de mecanizado con doble mesa –que hoy en día están muy de moda—. “Se puede ser tan eficiente con estos sistemas, así como las nuevas tecnologías de hoy en día”, refiere Retana. “Adquirimos un sistema neumático y nosotros hacemos los dispositivos de sujeción. Este sistema nos empezó a dar este orden y así fue como hace 10 años nos certificamos en la norma ISO 9001 2015”.
“También tenemos mucha herramienta de alto rendimiento, uno de los puntos fundamentales que nos permitió el crecimiento, ya que las máquinas requieren de esa calidad de herramientas para poder alcanzar los tiempos de mecanizado. De otra manera, si no se hace uso de buenas herramientas y de buenos sistemas de sujeción, pues no aprovechas la capacidad que tienen este tipo de máquinas”, explica el ingeniero Retana.
Anteriormente, realizaban los trabajos en tornos convencionales y fresadoras, haciendo la sujeción en prensas convencionales. Empezaron con pocas piezas y fueron avanzando con las máquinas de control numérico. Actualmente, tienen tres Chevalier de 3 ejes, donde hacen operaciones todo tipo: contornos, ranuras, barrenado, roscado y ángulos, además de otras geometrías complejas.
Estos centros de mecanizado los adquirieron hace 12 años. Desde que tiene estos centros, empezaron con el sistema de montaje rápido para varias piezas, pudiendo poner piezas diferentes en un solo montaje para hacer varias operaciones sin necesidad de quitar y poner diferentes trabajos.
Sin embargo, para llegar a eso fue todo un proceso de aprendizaje: usaron los sistemas de clampeo a través de prensas mecánicas, y a través de clamps sobre la misma mesa, para ir alineando pieza por pieza.
“A medida que fuimos agarrando experiencia, empezamos a crear esas molduras y fijar nuestros setups y piezas de trabajo en los códigos de la máquina para evitarnos estar alineando una por una. Una vez que hicimos esos dispositivos, nos evitó el estar alienando y ahora en lo único que tardamos es en ajustar las herramientas y poner la máquina a punto, que yo creo que no nos lleva alrededor de 15 minutos entre cambio y cambio de pieza”, dice Retana.
Anteriormente, con las prensas tardaban un turno de 8 horas para hacer una sola pieza.
“Actualmente, dependiendo de la geometría de la pieza, hay operaciones donde hacemos una placa de acero inoxidable, con 3 barrenos y 3 machueleados, y estamos produciendo alrededor de 100 piezas en un turno de 8 horas, desde que se monta el palet hasta que se ajusta la herramienta y se produce la pieza. Hacemos bujes, soportes para las bases de las cabinas, husillos, roscados, pernos y algunos componentes de aluminio de diferentes geometrías: cuadrados, redondos y hexagonales”, cuenta el ingeniero Retana.
Un paso más allá con el torneado tipo suizo
Como Maquinsa está inmerso en un mercado donde se trabajan bajos volúmenes y muchos números de parte, han tenido que invertir muchos recursos para herramentar una máquina. Y, en muchos casos, para hacer una sola pieza tienen que herramentar una máquina determinada.
Por esa razón, el ingeniero Eduardo Retana tomó la decisión de adquirir un torno tipo suizo. “Lo que pretendí al adquirir esta máquina es que podamos traer una línea de producción más grande, y que tengamos el mínimo de cambio de herramienta o adquisiciones de herramientas, aunado a que estas producciones que hagamos poderlas pasar o complementarlas con el proceso de galvanizado y entregar el producto terminado”, dice Retana.
La máquina que adquirieron es un torno tipo suizo de Tsugami (modelo B0265-II con alimentador de barra). Comparando un trabajo típico realizado en Maquinsa, usando varias máquinas, es evidente la diferencia comparado con el torno tipo suizo.
“La diferencia va a depender del número de operaciones. Para una pieza sencilla en un torno de control numérico puedes hacer una operación de cilindrado o torneado longitudinal, un chaflán y una operación de tronzado o roscado, que llevará un posicionamiento de barrenos en diferentes grados; como no tiene herramientas vivas, tendríamos que bajar esa parte y pasarla a una segunda máquina, que sería el centro de mecanizado, y tendríamos que hacer una montura especial y complementarla con esas operaciones de barrenado y roscado. Entonces, a lo mejor en una pieza sencilla estaríamos ocupando entre unas 6 y 8 herramientas”, explica el ingeniero Retana.
“Con la máquina Tsugami, un torno de 5 ejes, lo que pretendemos es eliminar esa operación en el centro de mecanizado. Lo que queremos hacer es cilindrado, posicionamiento de barreno, roscado, operación de tronzado y que la pieza salga ya terminada. Todo en un solo montaje y, además, que trae su alimentador de barra. Entonces, también vamos a evitar desperdicios por corte de barra, ya que al final el sobrante es mínimo para aprovechar al máximo la materia prima”, afirma Retana.
Un ejemplo de una pieza que estaban trabajando durante mi visita era un buje con un diámetro exterior de 316, que lleva un barreno de 5 octavos. “Si hiciéramos ese trabajo en el torno tradicional, lo único que podríamos hacer es un cilindrado de interior (el barreno interior). Luego tenemos que hacer un torneado longitudinal exterior para dejarla de 316, un poco debajo de la medida. Después en una longitud de una pulgada hacemos un tronzado, posteriormente, tenemos que pasar esa pieza a un centro de mecanizado. Ahí llevamos 3 herramientas y, luego, pasamos la pieza a un centro de mecanizado, donde hacemos un barreno y una operación de roscado. Esa pieza lleva 4 barrenos a 90 grados igual a la rosca, entonces requerimos de 2 herramientas más, que es la broca y el machuelo”, explica el ingeniero Retana.
El tiempo que se tarda en el torno en hacer los cambios manuales y en el centro de mecanizado para rotar los grados, son de hasta 4 minutos por pieza. Hoy en día, la idea es que con el torno Tsugami puedan bajar hasta 45 segundos o un minuto este tipo pieza. Además, en el torno tipo suizo de Tsugami usarían las mismas herramientas para las 5 operaciones: barreno interior, careado frontal, cilindrado y tronzado.
Así, usarían las mismas herramientas, pero con la diferencia que hacen la operación en una sola máquina y en un solo montaje. Con este nuevo proceso solamente tienen que calibrar las herramientas y se liberan dimensiones. Una vez que se libera la primera pieza, se corre la producción. De acuerdo con una tabla realizada por Maquinsa, se va haciendo un muestreo para ir verificando que la medida o las tolerancias se sigan cumpliendo.
“Las herramientas que usan estas máquinas son costosas. Y para hacer una pieza muchas veces tú requieres alrededor de unos 3,000 a 4,000 dólares para hacer una sola pieza, y muchas veces son corridas únicas. Entonces, la idea de adquirir esta nueva tecnología es que podamos ingresar a un mercado con pocos números de parte, pero con mayor volumen, en el cual podemos hacer una inversión de herramientas y que estas no sirvan para una plataforma, de al menos de 3 a 4 años”, concluye el ingeniero Retana.
Maquinsa crea un programa de planeación a la medida
A Maquinsa los mismos requerimientos que tiene el sector industrial lo fueron metiendo en el proceso de crecimiento de su taller: la calidad, los tiempos de entrega y el compromiso con los clientes.
“Yo creo que el crecimiento es esa parte que nunca supimos digerir y que todos decíamos sí, aunque nos metiéramos en problemas. La misma necesidad de la industria nos fue jalando sin ninguna planeación, de tal forma que a medida que nos dimos cuenta, pues ya estábamos inmersos en un campo donde el requerimiento para estas industrias es importante y que no puedes pararle a una línea de producción porque los tienes al día aquí”, cuenta el ingeniero Retana.
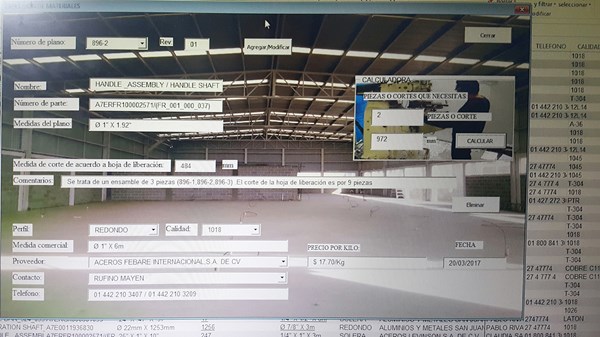
Sin embargo, la hija de Eduardo Retana llegó al taller hace un año para aportarle nuevas ideas a la empresa y cambiar muchas cosas. Mary Carmen Retana vio que en el taller hacían muchas cosas de manera reactiva, debido a que los volúmenes por número de parte que Maquinsa maneja son bajos y cambian día a día. Por esa razón, empezó a poner orden en casa. Inició con los procesos de producción creando una planificación a través de un programa:
“La manera como llevamos la producción comienza cuando se genera la orden de compra y la parte de fabricación se carga en este plan. Es lo que nos lanza para poder comprar la materia prima antes de la fecha que solicita el cliente. Como podrás ver, manejamos muchos números de parte, hablamos de 1,037, son más de 1,000 números de parte y los volúmenes son bajos. Entonces, cuando empezamos a planear, es ahí donde se vuelve caótico, porque el cambiar un herramental para hacer 42 partes y luego 38 de otro número de parte, y luego si vuelven a llegar 42 del mismo, entonces es mover y cambiar de herramientas. Lo que se hizo fue tener un balance interno de los números de parte que tenemos con mayor consumo y ver cómo fueron sus tendencias a lo largo del año. Eso nos ayuda para nosotros poder tener stocks y adelantarnos en la fabricación”, explica la ingeniera Mary Carmen sobre el programa de planeación que ella misma creó.
Este programa les ayudó a poder responder de manera rápida a los clientes y tener internamente piezas en inventario. “Ahora nosotros corremos el riesgo de tener esas piezas en stock, esperando que no se cambie de revisión, porque eso nos implicaría un retrabajo o que las piezas pasen a destrucción”, explica ella.
“Uno de los éxitos de la empresa es que pudimos visualizar y tener esa habilidad para hoy en día poder tener todas esas entregas de pequeños volúmenes. Nuestros indicadores nos dicen que estamos en 96% de entregas a tiempo al día de hoy. De tal forma que, durante estos cuatro años, Siemens nos ha reconocido como uno de sus mejores proveedores. El año pasado Tremec también nos reconoció como uno de los mejores proveedores y este es el resultado de parte de todo el equipo de trabajo” afirma el ingeniero Eduardo Retana.
La mayoría de los trabajos que actualmente hace Maquinsa son para Tremec y Siemens, además de otra compañía del sector eléctrico en San Luis Potosí y una compañía ubicada en Querétaro, del sector médico.
Como Maquinsa entrega las piezas completamente terminadas, los productos que ellos fabrican se van a procesos externos, sea de galvanizado, soldadura o fosfato. Debido a esa situación y a que ellos quieren hacer todos los procesos internamente, el ingeniero Retana adquirió un nuevo terreno donde construyó los nuevos talleres de su empresa, que estarán en funcionamiento a finales de este año.
Precisamente, allí estará línea de galvanoplastia, donde podrán hacerle acabados a todas las piezas que ellos mecanizan en el taller, además de prestarles servicio a otras empresas del sector que lo requieran.
“Afortunadamente, hoy en día todo ha salido bien y estamos cumpliendo con todas las fechas de entrega. Nos hemos venido preparando para responder cualquier eventualidad y responder a tiempo”, explica el ingeniero Eduardo Retana.
También se automatizó el cuarto de herramientas
Otro trabajo que hizo la ingeniera Mary Carmen Retana fue la creación de inventarios y una base de datos de todas las herramientas que se usan en el taller.
“Creamos inventarios y bases de datos que nos ayudan de manera automática a visualizar la vida útil de nuestra herramienta para poder mandar a reafilar. Asimismo, nos permite ver los inventarios que tenemos de insertos, y nos ayuda mucho para tener en tiempo y forma las herramientas”, explica la ingeniera.
Lo interesante y útil de este programa creado por ella, es que generan una hoja de herramientas exclusiva para cada plano, para asegurar que en la siguiente producción se va a utilizar la misma herramienta y poder tener registrados los posibles cambios, por si hay necesidad de hacer la trazabilidad y el rastreo de la herramienta.
De esa manera, en la computadora están registrados los inventarios de los consumibles y, a través de un buscador, de manera automática el Área de Compras sabe qué es lo que se requiere en el taller. Es decir, cada vez que se entrega una herramienta al taller se descarga de la base de datos para llevar la relación de la cantidad de operaciones que ha realizado cada herramienta para saber cuándo necesita reafilado o reposición.
“Tenemos un límite establecido, pues ya sabemos más o menos la vida útil de esa herramienta y mandamos en automático a afilar. Eso nos ayuda a tener un backup, y poder mandar a afilar una herramienta, que regrese y la otra, y eso es muy útil para la productividad del taller.
En el caso de los materiales, también Maquinsa cuenta con un programa desarrollado por ellos mismos. En el programa aparece el número de plano, por ejemplo el 896, donde dice que se trata de un ensamble de 3 piezas: 891-1, 896-2 y 896-3. Entonces, para el 896-1 se trata de una solera de un cuarto por uno. Ahí parece el número de metros comprados de material, el vendedor, el precio por kilo y la fecha en qué fue comprada.
“Entonces, si nosotros requerimos hacer 50 piezas, en automático nos da la explosión de qué solera y a qué proveedor debemos de confiarle”, explica la ingeniera Mary Carmen. El programa fue creado a través de Visual Basic y ellos lo llaman “Explosión de materiales”.
A pesar de que es el mismo ensamble, el material se le compra a un proveedor diferente.
Contenido relacionado
Tornos tipo suizo de herramientas vivas agregan flexibilidad
Con la adquisición de nuevos tornos tipo suizo y de herramientas vivas, Rathburn Tool & Manufacturing alcanzó un nuevo nivel de competitividad y expansión en el mercado.
Leer MásHerramientas de corte para el torneado vertical
Explore tendencias en herramientas de corte para tornos verticales CNC, esenciales para optimizar el mecanizado de materiales complejos.
Leer MásEstrategias de diversificación para talleres de mecanizado
Tras más de cuarenta años en el negocio, este taller ha aprendido a adaptarse para seguir siendo rentable.
Leer MásMazak presenta avances clave en tecnologías de mecanizado en IMTS 2024
En la IMTS 2024, Mazak destacó tres innovaciones en su línea de máquinas-herramienta: el centro de mecanizado horizontal HCN-4000 Neo, el torno multitarea HQR 200/3 Neo y la serie de máquinas tipo suizo Syncrex 25/8. Estas tecnologías están diseñadas para maximizar la productividad y precisión en una amplia gama de aplicaciones, desde la producción de piezas pequeñas y complejas hasta el mecanizado pesado.
Leer MásLea a continuación
Consideraciones para comprar un torno CNC
Los tornos CNC son una de las tecnologías de mecanizado más antiguas; sin embargo, sigue siendo útil recordar los aspectos básicos a la hora de considerar comprar una máquina de este tipo.
Leer MásPor qué usar torneado tipo suizo
¿Para qué clase de producción se usan los tornos tipo suizo? ¿En qué se diferencian de los centros de torneado convencionales? Expertos y usuarios cuentan sus experiencias.
Leer MásLa tecnología: recurso primordial para ser proveedor de la industria aeroespacial en México
Indumet Aerospace es una de las empresas pioneras en México como Tier 1 de la industria aeroespacial. La inversión en la última tecnología para el mecanizado en 5 ejes ha sido una de las claves del éxito que la ha llevado a ser proveedora de reconocidos OEM.
Leer Más