Supere los desafíos del roscado de piezas endurecidas
El roscado de piezas endurecidas origina tiempos de ciclo prolongados y desgaste rápido de la herramienta para un taller. El Secomax CBN200 de Seco ha reducido en un tercio el tiempo de ciclo de roscado.
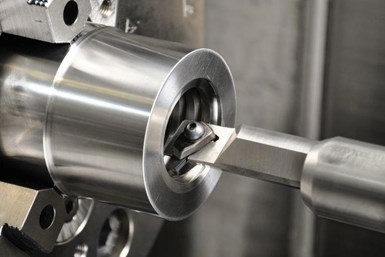
El cuerpo del portaherramientas para esta operación de roscado interno utiliza un material denso con tungsteno añadido.
Las aplicaciones para las industrias médica, aeroespacial, y de petróleo y gas comúnmente requieren componentes endurecidos que ofrecen alta resistencia, resistencia al desgaste y un acabado superficial de alta calidad.
Desafíos del mecanizado en estado blando
Sin embargo, la producción típica de tales piezas puede ser lenta y costosa, ya que a menudo se mecanizan con una forma cercana a la forma final en estado blando o “verde” y posteriormente se mecanizan, luego del endurecimiento mediante tratamiento térmico.
Múltiples pasos de proceso aumentan la posibilidad de cometer errores humanos y operativos que pueden conducir a una pieza desechada. El potencial de problemas logísticos, piezas cargadas incorrectamente o piezas deformadas debido al tratamiento térmico, lleva a los talleres a considerar procesos de mecanizado completamente internos a partir de material endurecido, lo cual les permite obtener mayor control sobre su proceso de producción de piezas en general.
La complejidad del roscado en materiales endurecidos
De acuerdo con Seco Tools, la capacidad para fresar, tornear, perforar y, en particular, roscar material endurecido demostró ser un desafío para un taller en particular.
El material era hierro enfriado con una dureza de 70 HRC. La pieza era de 5 pulgadas de diámetro con un diámetro de 2,5 pulgadas que requería una rosca interior ACME de 4 pulgadas de largo (este es un tipo de rosca grande para accionamiento, con una profundidad de rosca de aproximadamente 0,265 pulgadas). Además, la pieza requería varios orificios ciegos roscados de 1/4-20 con 0,6 pulgadas de profundidad.
El lanzamiento oportuno de una nueva línea de productos dependía de la capacidad de este taller para producir rápida y económicamente los componentes con estas operaciones. Desafortunadamente, no fue capaz de roscar las partes en su estado endurecido, a pesar de probar diversos tipos de herramental de carburo y nitruro de boro cúbico (CBN), entre otros.
El taller consideró el roscado de las piezas en su estado blando y a continuación mejorar las roscas, luego de que fueran endurecidas. Sin embargo, encontró que esto era una solución impracticable porque requería múltiples operaciones, largos ciclos de mecanizado y vidas cortas de la herramienta que prolongaban el tiempo de producción.
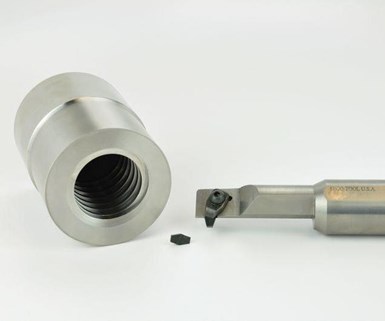
Con la pieza en estado endurecido, la operación de roscado para la rosca ACME requiere casi 40 pasadas a profundidades de corte menos profundas que cuando la pieza está en estado blando.
Cuando el taller se puso en contacto con los especialistas en herramientas de Seco, Don Halas y Aaron Eller, para pedir su ayuda, ambos descartaron inmediatamente una herramienta de carburo, porque tal herramienta se desgastaría antes de completar la forma completa de la rosca.
Innovación con insertos Secomax de Seco
En su lugar, les sugirieron el grado de inserto Secomax CBN200 estándar universal de Seco. Según se indica, este grado es muy adecuado para cortes muy interrumpidos en aceros y hierros fundidos. Para la operación de roscado interno del taller, Seco mejoró la geometría del inserto y la preparación del filo para enfrentarse al hierro frío duro y altamente abrasivo.
El inserto trapezoidal resultante, el Secomax CBN-CBD con punta, fue diseñado para ofrecer dureza, resistencia al desgaste y larga vida útil de la herramienta. De hecho, el inserto mejorado redujo el tiempo de ciclo de roscado en 33 por ciento, según indica Seco.
Bajo condiciones de piezas normales o blandas, una herramienta de carburo generaría la rosca ACME en aproximadamente 18 pasadas. Con la pieza en estado endurecido, la operación requirió casi 40 pasadas a profundidades de corte menos profundas. Ese número de pasadas, según Eller y Halas, era bastante aceptable, considerando la alternativa del primer mecanizado en estado blando.
Halas señala que esta fue la primera vez de una operación como esta para el cliente y para Seco. “Tuvimos que diseñar, producir y especificar todos los componentes, incluido el inserto, el sujetador y los parámetros de corte, específicamente para este taller y este trabajo”, indica.
Esta aplicación de roscado requiere una gran rigidez y resistencia tanto en el portaherramientas como en la máquina-herramienta que realiza la operación. Seco produjo dos versiones de un portaherramientas, hecho de un material denso y pesado, con tungsteno añadido: uno usando un estilo de sujeción de agujeros C-lock para operaciones de mecanizado confinadas y el otro usando un estilo pin-lock y grapa para aplicaciones de propósito general y de trabajo pesado.
Evolución en las operaciones de roscado de agujero ciego
El portaherramientas también tuvo un profundo efecto en las operaciones de roscado de agujero ciego de la pieza. Inicialmente, se utilizaba un taladro con punta CBN y una fresa roscadora de carburo estándar para crear los orificios roscados. Utilizando este método, el taller podía producir dos o, a veces, tres orificios roscados completos.
“Entonces decidimos poner la fresa de roscado en un portaherramientas de ajuste por encogimiento”, explica Halas. “Haciendo esto se aumentó su productividad hasta aproximadamente ocho agujeros, pero la broca continuaba soportando solo el mecanizado de hasta tres agujeros. Fue allí cuando incorporamos la interpolación circular en lugar de simplemente fresar los agujeros, lo cual proporcionó tres veces la vida útil de la herramienta en comparación con la broca”.
Este inserto trapezoidal con punta de CBN fue diseñado para ofrecer dureza, resistencia al desgaste y larga vida de la herramienta. Según se indica, ha reducido el tiempo de ciclo de roscado para la pieza endurecida en 33 por ciento.
El diámetro del agujero fresado con interpolación circular era de aproximadamente 0,2 pulgadas. La herramienta usada fue una fresa escariadora estándar de carburo sólido de Jabro, en un portaherramientas de ajuste por contracción.
Según Seco, una vez que el taller se dio cuenta de todo lo que se logró con la pieza endurecida, hizo que el fabricante de herramientas evaluara muchas de las demás operaciones de mecanizado, pidiéndole a Seco que identificara otras piezas y operaciones que podrían optimizarse a través de cambios y/o ajustes en herramientas. En los períodos de mayor demanda, el taller mecaniza ahora miles de piezas endurecidas por año, indica Seco.
“Realmente no había nada nuevo, en cuanto a lo que se refiere a la tecnología de herramientas involucrados con este proyecto”, dice Eller. “El CBN ha existido desde hace mucho tiempo, al igual que el carburo. Pero lo que fue clave para el éxito del proyecto fue que evaluamos el proceso de toda la pieza. Hemos ido desde el principio hasta el final y hemos desarrollado herramientas que optimizan todos los aspectos y le permiten al taller alcanzar sus objetivos de mecanizado”.
Contenido relacionado
Herramientas de corte para el torneado vertical
Explore tendencias en herramientas de corte para tornos verticales CNC, esenciales para optimizar el mecanizado de materiales complejos.
Leer MásConsejos para optimizar el mecanizado del acero inoxidable
Explore técnicas avanzadas y estrategias de mecanizado para el acero inoxidable, incluyendo la selección de herramientas y el ajuste de los parámetros de corte.
Leer MásReduzca costos de operación en el maquinado con luces apagadas
Estrategias efectivas para gestionar costos fijos y variables en las herramientas y asegurar la eficiencia y rentabilidad del maquinado con luces apagadas.
Leer MásHusillos auxiliares de alta velocidad: innovación y eficiencia
Explore cómo los husillos de alta velocidad optimizan el mecanizado, ofreciendo flexibilidad y ahorro energético. Conozca sus ventajas y aplicaciones.
Leer MásLea a continuación
Roscado de forma vs roscado de corte: productividad en mecanizado
El paso del roscado de corte al roscado de forma en una aplicación importante redujo los costos de herramientas en Siemens Energy y multiplicó por cien la vida útil de las herramientas.
Leer MásFresado de roscas vs roscado tradicional: análisis de eficiencia
En comparación con el roscado por macho roscador, la tecnología de fresado de roscas ofrece ventajas para mecanizar roscas en materiales exigentes, como acero para herramientas, acero inoxidable y aleaciones de alta temperatura. Aquí hay algunos consejos para establecer un proceso efectivo de fresado de roscas en esos materiales.
Leer MásOpciones de roscado para materiales duros
Aquí se presentan tres enfoques de herramientas de corte para el roscado de componentes endurecidos.
Leer Más