Siemens presenta solución para gestionar la “nueva normalidad” en la manufactura
La empresa desarrolló una solución que ayuda a los fabricantes a simular y administrar los riesgos de exposición de los empleados.
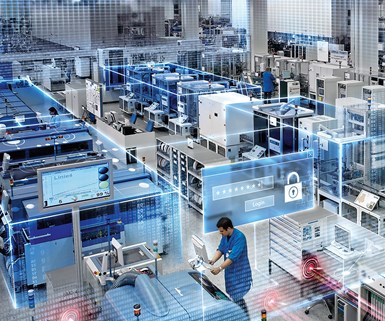
Siemens creó una nueva solución que permite a las empresas modelar de manera rápida y eficiente cómo los empleados interactúan entre sí, la línea de producción y el diseño de la planta. / Foto: Siemens.
Los fabricantes enfrentan nuevos desafíos mientras buscan reiniciar o mantener las operaciones durante la actual pandemia de COVID-19. A medida que se realizan los preparativos para la "nueva normalidad", los fabricantes deben considerar dimensiones adicionales de seguridad para los empleados, incluido el establecimiento de entornos de producción y flujos de trabajo que aborden los requisitos de distanciamiento físico, refiere la empresa Siemens por medio de un comunicado.
El documento señala que, combinando hardware y software probados, Siemens creó una nueva solución que les permite a las empresas modelar de manera rápida y eficiente cómo los empleados interactúan entre sí, la línea de producción y el diseño de la planta. La nueva solución también les permite a las organizaciones construir un gemelo digital de extremo a extremo para simular la seguridad de los trabajadores, reiterar y optimizar los diseños del espacio de trabajo y validar las medidas de seguridad y eficiencia para ayudar a las líneas de producción.
“Con Simatic RTLS (Real Time Locating Systems) de Siemens, las compañías pueden medir continuamente las distancias entre los trabajadores, proporcionar retroalimentación visual en tiempo real a los empleados con respecto a su separación de los demás y crear un registro de todos los movimientos e interacciones a lo largo del tiempo. De esta forma, facilita continuamente el distanciamiento seguro”, refiere el comunicado.
Añade que la combinación de Simatic RTLS con un gemelo digital del entorno real de manufactura les permite a las empresas modelar y simular cómo los empleados interactúan con el equipo y entre sí, permitiéndoles reiterar y optimizar la seguridad y la productividad a corto plazo, así como validar un rediseño de la operación completo antes de realizar cambios físicos más costosos.
"Estamos ayudando a nuestros clientes a crear un ambiente de trabajo seguro, lo cual es extremadamente importante, ya que buscan producir de manera eficiente y confiable en circunstancias sin precedentes", dijo Tony Hemmelgarn, Presidente y CEO de Siemens Digital Industries Software.
Agregó que la combinación de gestión de distanciamiento en tiempo real y simulaciones digitales ayudará a las empresas a mantener entornos de trabajo seguros en la actualidad y a tomar decisiones informadas sobre la optimización continua y a largo plazo.
Para implementar esta solución, los transpondedores Simatic RTLS de Siemens están incrustados en insignias que todos los empleados usan como equipo de protección personal. Los receptores RTLS ubicados durante toda la operación pueden rastrear y registrar continuamente el movimiento de la fuerza laboral. Cuando dos empleados se encuentran en un escenario de riesgo (por ejemplo, a menos de seis pies de distancia), sus insignias mostrarán una advertencia, alertándolos sobre la situación. Los datos recopilados a lo largo del tiempo se pueden analizar para identificar los “puntos críticos” donde los escenarios de riesgo ocurren con frecuencia.
“Utilizando los datos recopilados, se pueden simular nuevos diseños de manufactura o flujos de trabajo hasta que se determine uno para proporcionar los resultados deseados, que luego se pueden implementar en la operación física”, refiere el comunicado.
Más allá de esto, añade el documento, los fabricantes pueden agregar trazabilidad a la solución a través de las soluciones locales.
“Siemens está proporcionando una solución potente y de rápida implementación que ayuda a los fabricantes a tomar el control de sus operaciones y lograr mejores resultados de seguridad, productividad y costos en la era posterior a COVID-19”, comentó Raj Batra, Presidente de Digital Industries Siemens USA.
Contenido relacionado
Soluciones avanzadas de manufactura para componentes de precisión
Con cuatro nuevos centros de mecanizado de 5 ejes y dos células PH Cell Twin de DMG MORI, esta compañía refuerza su compromiso con la excelencia en la manufactura para sectores exigentes como el automotriz, médico y aeroespacial.
Leer MásDispositivos médicos en 2023: industria de crecimiento en México
México exporta casi 11,000 millones de dólares al año en dispositivos médicos con importaciones de 5,244 millones. Estados Unidos es el mercado más importante del país, con 96.7 % del total de las exportaciones.
Leer MásMéxico y Estados Unidos buscan fortalecer la cadena de proveeduría de semiconductores
Enrique Yamuni, presidente Nacional de CANIETI, dijo que los semiconductores impactan exportaciones en México por un valor aproximado de 120,000 millones de dólares.
Leer MásIndustria en México: 10 años de oportunidades y retos
En el contexto del décimo aniversario de Modern Machine Shop México, hacemos un recuento sobre el desarrollo, los retos y oportunidades de la industria manufacturera mexicana en los últimos 10 años.
Leer MásLea a continuación
Siemens anuncia cambios en su equipo directivo de México y Centroamérica
A partir del primero de julio, Alejandro Preinfalk, será el nuevo Presidente y CEO de Siemens México, Centroamérica y el Caribe.
Leer MásControl de procesos y producción en tiempos de COVID-19
De acuerdo con especialistas de Epicor las empresas están adoptando tecnologías que les ayuden en la colaboración remota.
Leer MásConsideraciones para comprar un torno CNC
Los tornos CNC son una de las tecnologías de mecanizado más antiguas; sin embargo, sigue siendo útil recordar los aspectos básicos a la hora de considerar comprar una máquina de este tipo.
Leer Más